Hello, long time reader of the forum. First time posting here. I am about to start a 2x72 belt grinder build. It is KMG clone based on the "knife-grinder.pdf" plans by Michael Clerc. My goal is building a high quality, but cost effective grinder. Under $1k for all parts and materials.
After reviewing the plans, I found a few items that didn't exactly line up, plus I want it to be direct drive with a VFD, so I decided to model it and make the modifications. Worst case, once I finish, I can put out some plans and drawings.
I am picking up the 0.75" material tomorrow to start piecing together the frame. That should keep me busy for a few days. I will finish the rest of the modeling (tooling arms, roller wheels, etc...) as I go.
Before I start, I was looking for anyone who has already built one of these to provide any feedback or things they would have changed if they did it over again?
Below is the grinder frame:
Also, I don't like how the tracking adjustment screw lands half way on the hole for the tracking wheel shaft. I will likely move this to fall in the center of the shaft or down below the shaft.
Let me know if anyone has any other feedback or suggestions on improvements? Thanks.
After reviewing the plans, I found a few items that didn't exactly line up, plus I want it to be direct drive with a VFD, so I decided to model it and make the modifications. Worst case, once I finish, I can put out some plans and drawings.
I am picking up the 0.75" material tomorrow to start piecing together the frame. That should keep me busy for a few days. I will finish the rest of the modeling (tooling arms, roller wheels, etc...) as I go.
Before I start, I was looking for anyone who has already built one of these to provide any feedback or things they would have changed if they did it over again?
Below is the grinder frame:


Also, I don't like how the tracking adjustment screw lands half way on the hole for the tracking wheel shaft. I will likely move this to fall in the center of the shaft or down below the shaft.
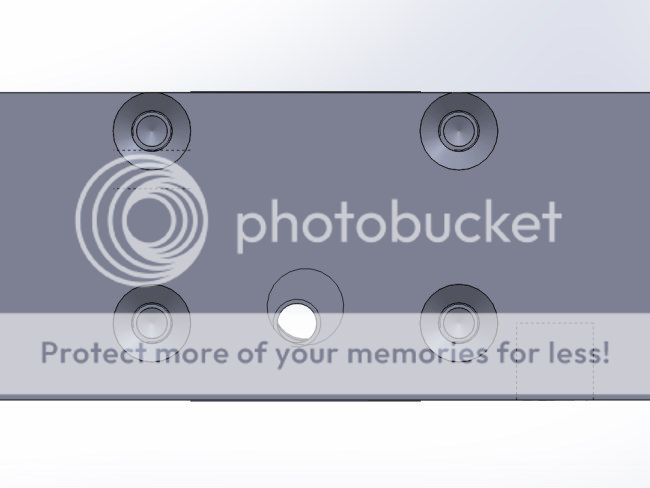
Let me know if anyone has any other feedback or suggestions on improvements? Thanks.