- Joined
- Mar 28, 2013
- Messages
- 1,730
She's here, she's here! Think it may be a bhojpure, not a longleaf. Runs at about 17" unless I'm measuring it wrong. Might bring it up to them, might not. This monster is 1/2" thick with a 3" belly though so I'm not complaining. The tang runs just long enough for me to squeak a nearly full tang handle and it came with not one, but TWO sets of negari script, not sure if that's normal or not. The blade came in good shape since I didn't hand select, the spine has contact marks and the edge is dull but it's to be expected. Anyways I'll just shut up.
This script is near where the blade drops:
And this is near the tang.
The materials so far:
One 8" copper tube (to be sliced, diced, and hammered into a bolster).
Various epoxies for handle securing, natural pine epoxy included, with authentic altoid can.
One: large forest full of trees for a handle! I have some maple and poplar chopped up already, one of those will become said handle, using poplar for the scabbard.
One: ye olde Longleaf khukuri blade (arrives Tuesday).
Hammers, files, rasps, that stuff. Handles don't make themselves now do they?
WD40 and a SOS pad for crud decrudding!
Missing anything?

This script is near where the blade drops:

And this is near the tang.
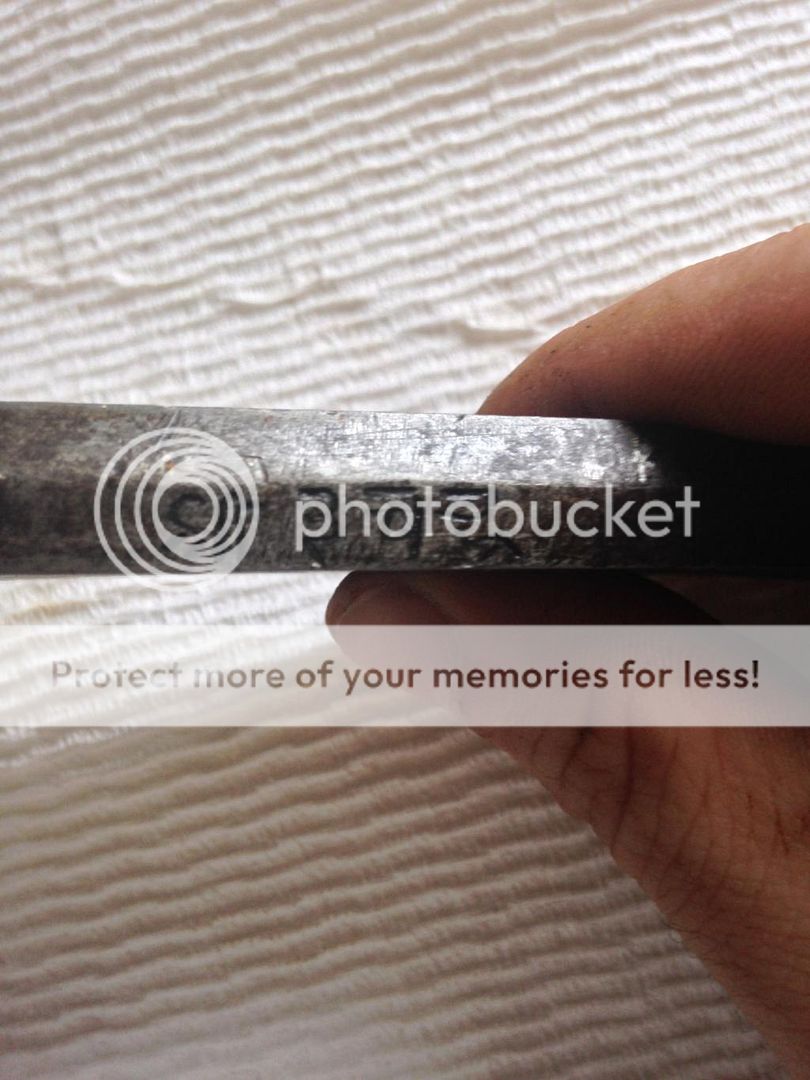
The materials so far:
One 8" copper tube (to be sliced, diced, and hammered into a bolster).
Various epoxies for handle securing, natural pine epoxy included, with authentic altoid can.
One: large forest full of trees for a handle! I have some maple and poplar chopped up already, one of those will become said handle, using poplar for the scabbard.
One: ye olde Longleaf khukuri blade (arrives Tuesday).
Hammers, files, rasps, that stuff. Handles don't make themselves now do they?
WD40 and a SOS pad for crud decrudding!
Missing anything?
Last edited: