Tony Mont
Knifemaker / Craftsman / Service Provider
- Joined
- Apr 15, 2018
- Messages
- 1,488
I recently had some unexpected grain size and would like some help because I cannot figure this out.
The test knife in question had this heat treatment protocol (it was a forged blade):
1) 1600F-870C for 15 minutes and air cool
2) 1450F-787C for 15 minutes and air cool
3) 1380F-748C for 30 minutes and let it cool overnight in the oven
4) Aus temp 1500F-815C for 10 minutes and quenched in parks 50 oil
5) 2x2hours temper at 400F-200C
This is the grain structure I ended up with.
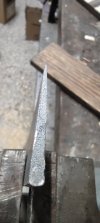
This morning, I made 5 coupons and began testing different protocols. I will explain my thought process on each test. All the coupons were marked with the corresponding number to avoid any mix ups. All pictures were taken using the macro setting on my phone.
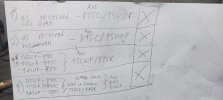
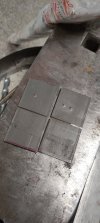
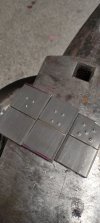
I usually put my knives in the oven while it heats up, that's why I decided the first two coupons would have the same treatment but one of them heated up along with the kiln and the second one was put inside after the kiln was up to temperature. I did this to check whether the kiln had a hot spot while it heats up or not.
On the left it's coupon #1 and on the right it's my test knife. The grain is similar in both which made me curious, I've never had steel to have such a bad grain structure from the "as received" status.
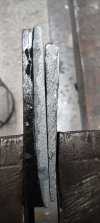
From left to right: coupon #1, knife from the test and coupon #2. This coupon was again heated to 1500F-815C from the as received condition but put in the kiln once it was up to temp. Even though it looks better in the picture, it's the same exact grain structure as the first. When the coupons were freshly broken, they had a lighter colour which makes it look like a finer grain. A few minutes later when all of them had the same darker colour, their true nature revealed.
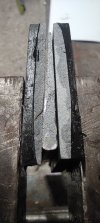
Coupon #2 on the left and coupon #3 on the right. Coupon #3 was cycled 3 times from the as received condition:
1650F for 10 minutes and cool to black
1550F for 10 minutes and cool to black
1450F for 10 minutes and cool to black
The idea behind this protocol was to add another lower cycle compared to my test knife. Once again, nothing changed. I know it looks better in the picture but it was not.
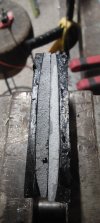
Here are all the coupons so far, from left to right coupon #1, coupon #2, coupon #3.
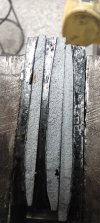
Finally, coupon #4. On this one, I did the same three cycles as coupon #3 and then added another one at 1365F and let it cool in the oven (is this slow enough for a DET anneal?)
On this coupon there might have been the slightest improvement. However, I would not call it acceptable. The grain structure was still visible with the naked eye.
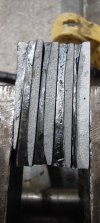
From my understanding, the last coupon should have given me a fine pearlite structure, right?
What would be your suggestions?
EDIT: forgot to attach the pictures.
Thank you in advance!
The test knife in question had this heat treatment protocol (it was a forged blade):
1) 1600F-870C for 15 minutes and air cool
2) 1450F-787C for 15 minutes and air cool
3) 1380F-748C for 30 minutes and let it cool overnight in the oven
4) Aus temp 1500F-815C for 10 minutes and quenched in parks 50 oil
5) 2x2hours temper at 400F-200C
This is the grain structure I ended up with.
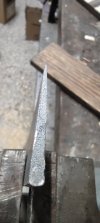
This morning, I made 5 coupons and began testing different protocols. I will explain my thought process on each test. All the coupons were marked with the corresponding number to avoid any mix ups. All pictures were taken using the macro setting on my phone.
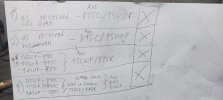
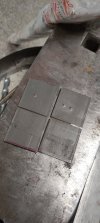
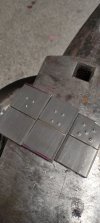
I usually put my knives in the oven while it heats up, that's why I decided the first two coupons would have the same treatment but one of them heated up along with the kiln and the second one was put inside after the kiln was up to temperature. I did this to check whether the kiln had a hot spot while it heats up or not.
On the left it's coupon #1 and on the right it's my test knife. The grain is similar in both which made me curious, I've never had steel to have such a bad grain structure from the "as received" status.
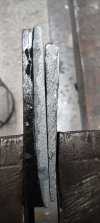
From left to right: coupon #1, knife from the test and coupon #2. This coupon was again heated to 1500F-815C from the as received condition but put in the kiln once it was up to temp. Even though it looks better in the picture, it's the same exact grain structure as the first. When the coupons were freshly broken, they had a lighter colour which makes it look like a finer grain. A few minutes later when all of them had the same darker colour, their true nature revealed.
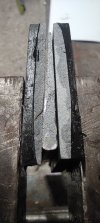
Coupon #2 on the left and coupon #3 on the right. Coupon #3 was cycled 3 times from the as received condition:
1650F for 10 minutes and cool to black
1550F for 10 minutes and cool to black
1450F for 10 minutes and cool to black
The idea behind this protocol was to add another lower cycle compared to my test knife. Once again, nothing changed. I know it looks better in the picture but it was not.
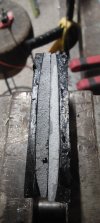
Here are all the coupons so far, from left to right coupon #1, coupon #2, coupon #3.
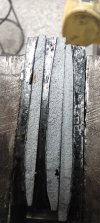
Finally, coupon #4. On this one, I did the same three cycles as coupon #3 and then added another one at 1365F and let it cool in the oven (is this slow enough for a DET anneal?)
On this coupon there might have been the slightest improvement. However, I would not call it acceptable. The grain structure was still visible with the naked eye.
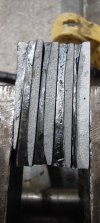
From my understanding, the last coupon should have given me a fine pearlite structure, right?
What would be your suggestions?
EDIT: forgot to attach the pictures.
Thank you in advance!