- Joined
- Dec 4, 2013
- Messages
- 891
This is the second knife I have completed. This one is a gift for a fella in Skidmore MO that let's a group of us come up and deer, turkey hunt on his acerage and drink beer and tell lies in his shop he calls the coon shack . He is big into trapping so I made him the not sure what to call it kind of caping knife.
OAL: 6 1/2
2 5/8 cutting edge
Steel: 1080+ .133 thick
Heat treat by Darrin Sanders
Zebra wood scales finished with truoil and brass pins
This baby is sharp!! I kind of surprised my self how sharp I got it but I'm a newbie so this is all new experiences.
Thanks for looking comments welcome. Good or bad
Justin Presson


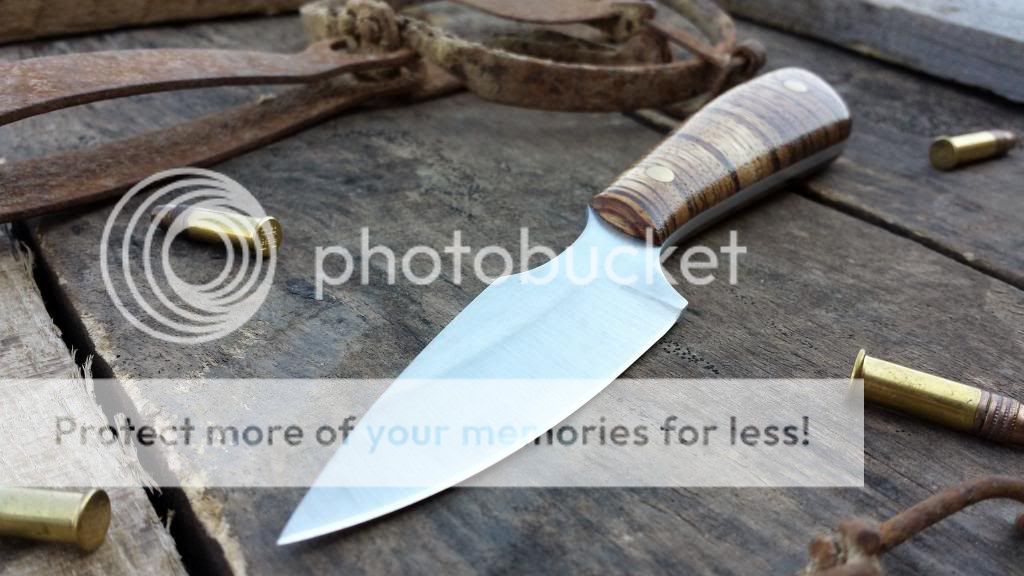


I hope the pics loaded right did it from my phone
OAL: 6 1/2
2 5/8 cutting edge
Steel: 1080+ .133 thick
Heat treat by Darrin Sanders
Zebra wood scales finished with truoil and brass pins
This baby is sharp!! I kind of surprised my self how sharp I got it but I'm a newbie so this is all new experiences.
Thanks for looking comments welcome. Good or bad
Justin Presson


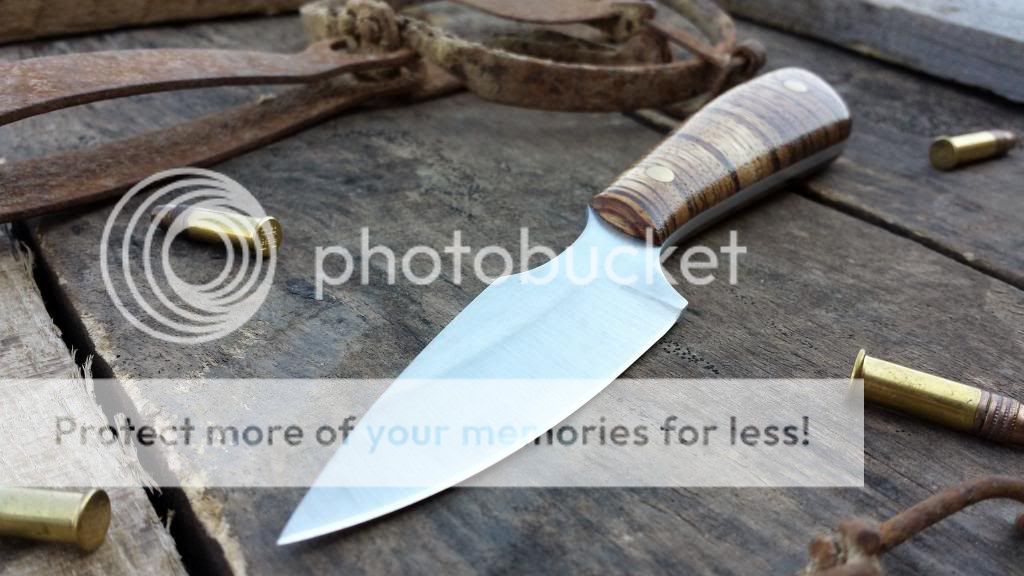


I hope the pics loaded right did it from my phone

Last edited: