- Joined
- Oct 29, 2006
- Messages
- 2,912
I made this pair of knives from a 3" ball bearing and handled them from a single block of Koa. So I made matching sheaths.
Still learning and I can never seem to get it "perfect". It's so frustrating.
Still there's something in these that I feel is a bit more refined.
A ways to go yet but I feel like there's progress. You can't see it but these are the nicest edges I've done to date.
Still learning and I can never seem to get it "perfect". It's so frustrating.
Still there's something in these that I feel is a bit more refined.
A ways to go yet but I feel like there's progress. You can't see it but these are the nicest edges I've done to date.
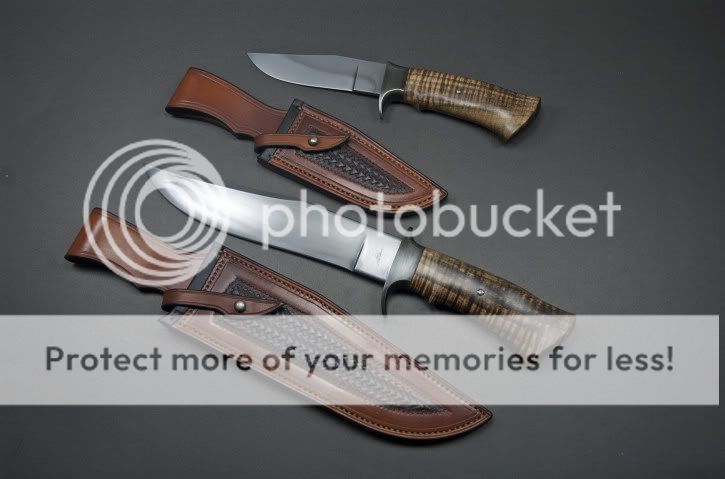


