- Joined
- Apr 12, 2006
- Messages
- 2,506
I'm working on a chunky quasi-wakizashi for the USN Gathering coming up with alarming rapidity, and thought I would document something interesting that happens when I do a quasi-Japanese blade. My apologies for the quality of the cell phone pictures.
One of the factors to take into consideration when making a Japanese-style blade is the sori, or amount of curvature that is formed during heat treatment. In a traditional blade using tamahagane steel in a water quench, the blade is straight when it come out of the fire and curves first down toward the edge then up toward the spine. It can be very stressful and there's a high rate of traditional blades tearing themselves apart in the quench. With an oil quench, a blade tends to get negative sori, curving toward the edge.
So, with this 5160 wakizashi, I gave it more curvature than I wanted and let the negative sori straighten it. The soapstone mark on the anvil shows where the spine was prior to the quench. I've never had a blade crack from sori in a canola quench.
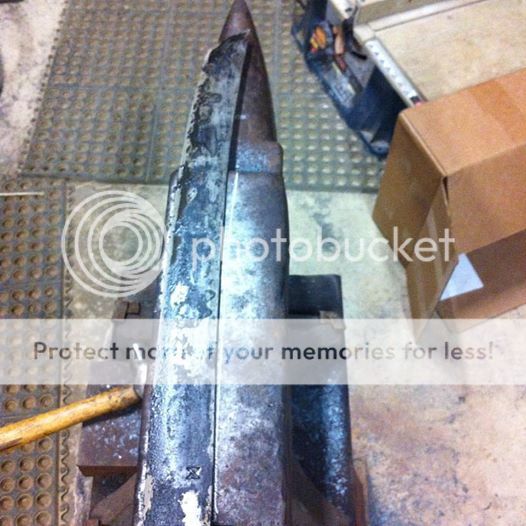
While at the base of the blade near the blade/tang transition there has been almost no change, about 2/3 of the way down it has moved about a 1/4". It seems like this happens by far the most with the quasi-Japanese blades I do. It's like they know...
I've gotten pretty good at gauging how much extra curvature to have to get the blade to straighten up to where I want it, but I don't do too many in this style.

One of the factors to take into consideration when making a Japanese-style blade is the sori, or amount of curvature that is formed during heat treatment. In a traditional blade using tamahagane steel in a water quench, the blade is straight when it come out of the fire and curves first down toward the edge then up toward the spine. It can be very stressful and there's a high rate of traditional blades tearing themselves apart in the quench. With an oil quench, a blade tends to get negative sori, curving toward the edge.
So, with this 5160 wakizashi, I gave it more curvature than I wanted and let the negative sori straighten it. The soapstone mark on the anvil shows where the spine was prior to the quench. I've never had a blade crack from sori in a canola quench.
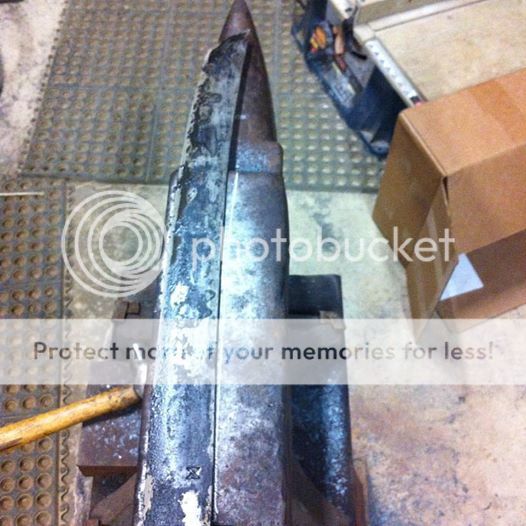
While at the base of the blade near the blade/tang transition there has been almost no change, about 2/3 of the way down it has moved about a 1/4". It seems like this happens by far the most with the quasi-Japanese blades I do. It's like they know...

