- Joined
- Apr 18, 2011
- Messages
- 4,925
Hey guys, I just wrapped up my latest tanto and tried a couple new things (for me) along the way. It's done at this point, but I will post a few of the pics I snapped along the way. I have to give a shout out to Dan Keffeler and David Mirabile for all of the inspiration, they are innovators in every sense of the word.
I don't have a lot of blade build picks, but I have covered that process pretty thoroughly in my previous threads.
Here is the blade, ground, hand sanded and ready for HT.

Fresh out of cryo

I have been playing with solid edge designing tsuba for waterjet. Here is my first design, and the one I will be using for this build.
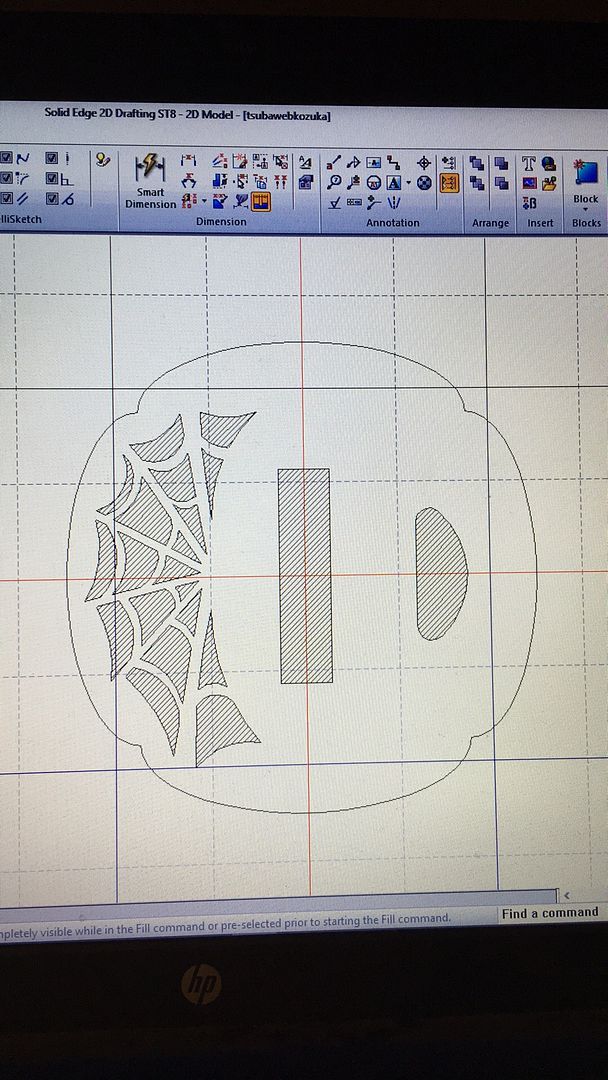
Here is the tsuba fit to the blade with the hammered copper seppa.

Next up, before I finish the blade, get started on the saya. I am using Tero tuf for the body of the sheath. In my opinion it is the perfect modern material for a saya. It is extremely durable, and it's non abrasive nature means it wont harm the blade. It is made of a low friction wear material, perfect for this.
Tracing the blade onto the material.

I went with a 3 pc construction method (no worries about splitting the saya on bad draw cut). Here I am milling the middle layer down to the proper thickness.
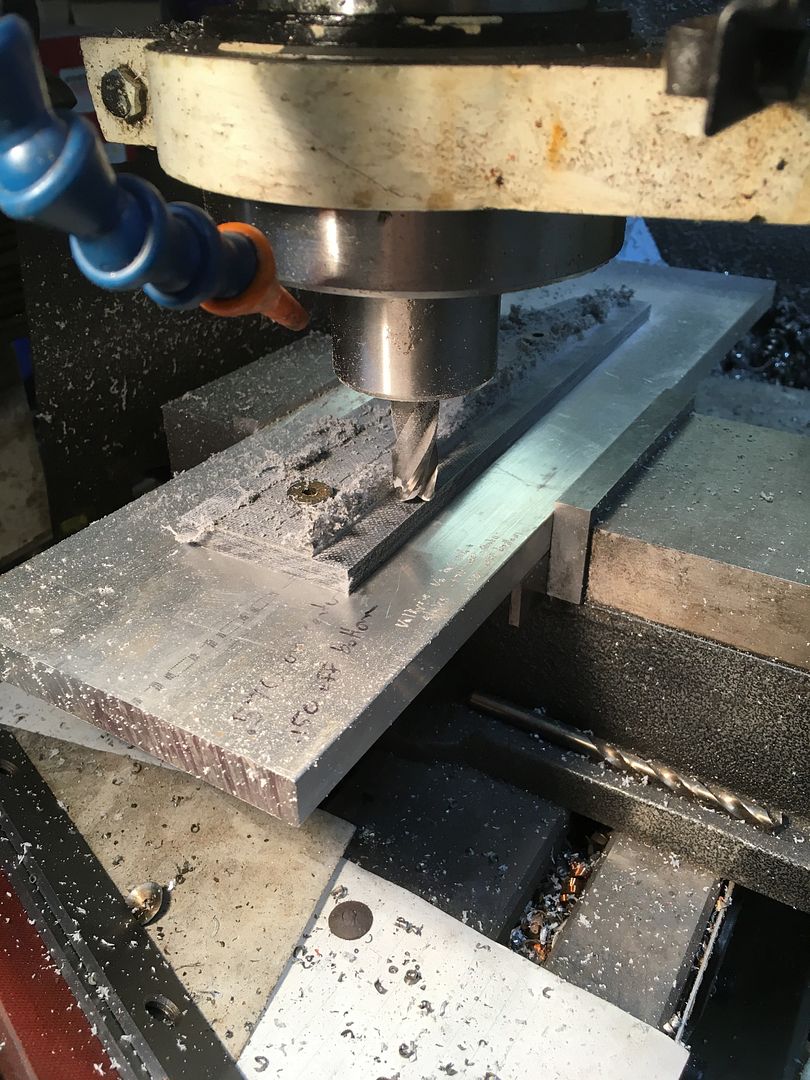
Drilling the holes for alignment.

Cut and fit to the blade. I use carbon fiber pins for alignment and structure in the construction.

more to come.......
I don't have a lot of blade build picks, but I have covered that process pretty thoroughly in my previous threads.
Here is the blade, ground, hand sanded and ready for HT.

Fresh out of cryo

I have been playing with solid edge designing tsuba for waterjet. Here is my first design, and the one I will be using for this build.
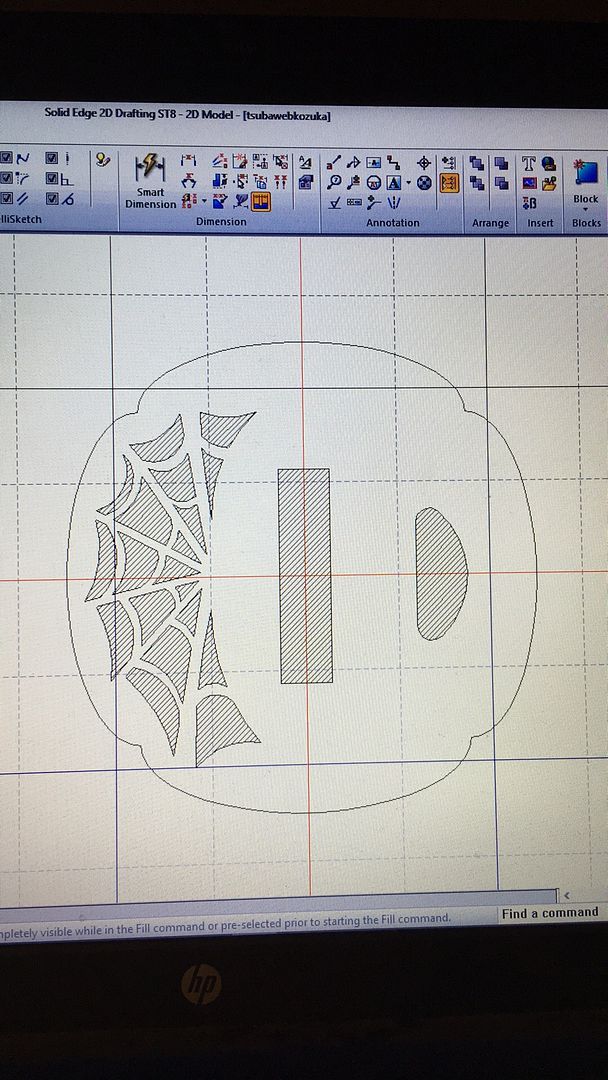
Here is the tsuba fit to the blade with the hammered copper seppa.

Next up, before I finish the blade, get started on the saya. I am using Tero tuf for the body of the sheath. In my opinion it is the perfect modern material for a saya. It is extremely durable, and it's non abrasive nature means it wont harm the blade. It is made of a low friction wear material, perfect for this.
Tracing the blade onto the material.

I went with a 3 pc construction method (no worries about splitting the saya on bad draw cut). Here I am milling the middle layer down to the proper thickness.
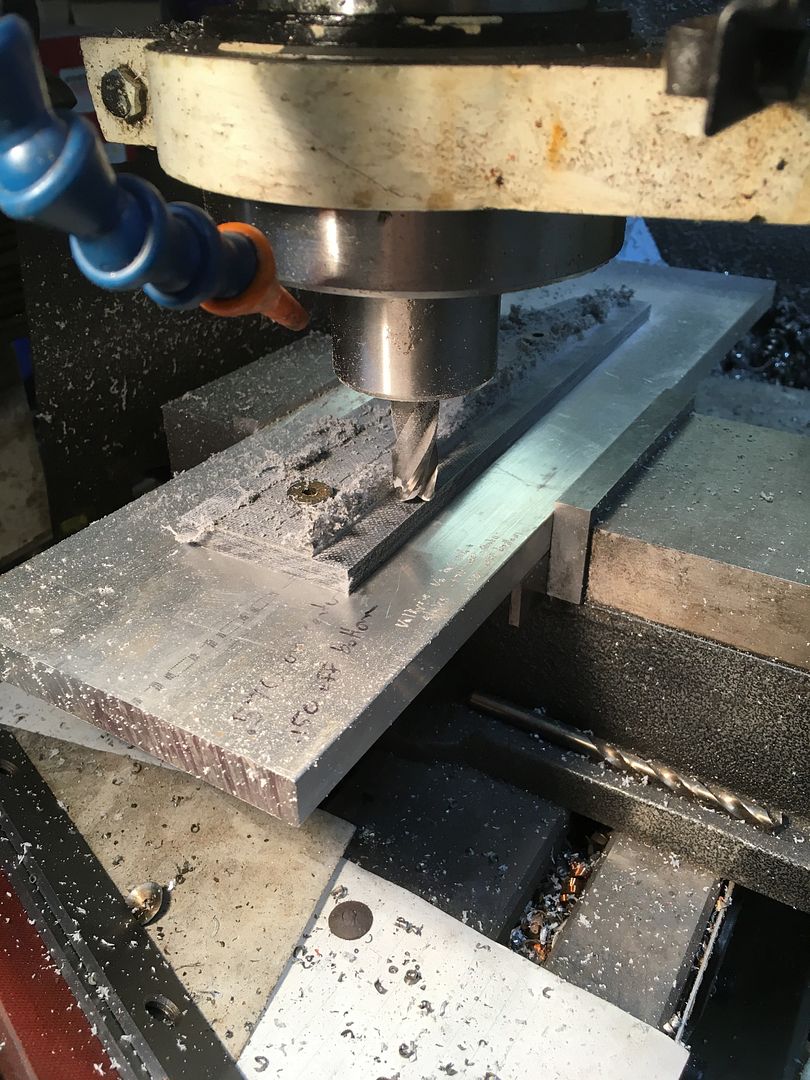
Drilling the holes for alignment.

Cut and fit to the blade. I use carbon fiber pins for alignment and structure in the construction.

more to come.......