BluntCut MetalWorks
Knifemaker / Craftsman / Service Provider
- Joined
- Apr 28, 2012
- Messages
- 3,462
I've two goals for this test
1. To get an idea the factor of rope attributes in dulling a knife.
1a. strength/hardness + toughness/resilent/elastic
1b. abrasive/wear
2. How production & my blades perform within the context of this test and no more than that.
Setup pic (1/2" sisal rope feeds through a 1/2 hole in the wood, clamp to table)
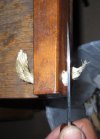
Air cut the loose end of the rope next to the wood (i.e. no backing). There will be quite a bit of lateral force in this kind of cutting, edge lateral deflection & scraping are the 2 major damaging physics to the blade apex. If the rope is abrasive, lateral rubbing/scraping will induce accelerated dulling affect, more than from the draw (normal/perdendicular) impact/saw. Strong+tough will quickly roll or chip the edge.
Knife performance result be measure by total length of rope cut. Test end when a knife consecutively fail three times to cut 2 of 3 strands of the 1/2 rope. Each cut consists of a draw stroke (i.e. pull or push but not both/sawing). Measurement begin when an edge has been adapted/tuned to this task. Really, there is no point to quickly roll an edge and declare this steel does poorly. I am looking for reasonably best possible edge geometry per specific steel against this task, not same bevel angle & grit for all steels.
If each test take way too much time & rope, I'll abandon this test. Since the answer is rope neither hard nor tough nor abrasive.
I've a few production knives for baseline, however blade profile & geometry will have variations:
bm: 940 s30v; pardue d2. spyderco: cf zdp-189, endura vg-10. paring sg-2, paring skd-11
Knives I made for baseline (same profile):
s90v, 20cv/m390, d2/k110, (maybe later on s110v, elmax, cpm-154, k390)
Recent super quenched knives:
52100, CruforgeV
Interested/suggestions/BC-stop-spam-BF? I would like to hear from you :thumbup:
1. To get an idea the factor of rope attributes in dulling a knife.
1a. strength/hardness + toughness/resilent/elastic
1b. abrasive/wear
2. How production & my blades perform within the context of this test and no more than that.
Setup pic (1/2" sisal rope feeds through a 1/2 hole in the wood, clamp to table)
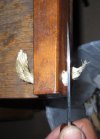
Air cut the loose end of the rope next to the wood (i.e. no backing). There will be quite a bit of lateral force in this kind of cutting, edge lateral deflection & scraping are the 2 major damaging physics to the blade apex. If the rope is abrasive, lateral rubbing/scraping will induce accelerated dulling affect, more than from the draw (normal/perdendicular) impact/saw. Strong+tough will quickly roll or chip the edge.
Knife performance result be measure by total length of rope cut. Test end when a knife consecutively fail three times to cut 2 of 3 strands of the 1/2 rope. Each cut consists of a draw stroke (i.e. pull or push but not both/sawing). Measurement begin when an edge has been adapted/tuned to this task. Really, there is no point to quickly roll an edge and declare this steel does poorly. I am looking for reasonably best possible edge geometry per specific steel against this task, not same bevel angle & grit for all steels.
If each test take way too much time & rope, I'll abandon this test. Since the answer is rope neither hard nor tough nor abrasive.
I've a few production knives for baseline, however blade profile & geometry will have variations:
bm: 940 s30v; pardue d2. spyderco: cf zdp-189, endura vg-10. paring sg-2, paring skd-11
Knives I made for baseline (same profile):
s90v, 20cv/m390, d2/k110, (maybe later on s110v, elmax, cpm-154, k390)
Recent super quenched knives:
52100, CruforgeV
Interested/suggestions/BC-stop-spam-BF? I would like to hear from you :thumbup:
Last edited: