- Joined
- Apr 19, 2005
- Messages
- 5,533
I had an idea from the great photos of the insides of the Stumps 110 special. Anyone have any "inside" photos of the workings of any Buck knives, lets have a thread. I know some of you 'modifiers' should have a few. BUT, I am going to practice what I preach and start a new thread. I have titled the thread so someone doing a search might be able to grab the tread from out of the air of history. Explain what you are showing. I will start. Stumps can inject his photo of the 110 if he wants. 300Bucks
How blades are attached in Model 300s. Bolsters are sliced thru the blade pins.
Model 301, first model made by Schrade under contract by Buck. Made using hidden bolster pin method. 'Swinden Key'.

Here is a photo of the side of the Schrade made Buck, the blades were put on the key pin, then both 'rivet like heads' were formed and then the heads slipped into the liner keyhole. This way no bolster pins show. But, they had issues with the strength of the brass.
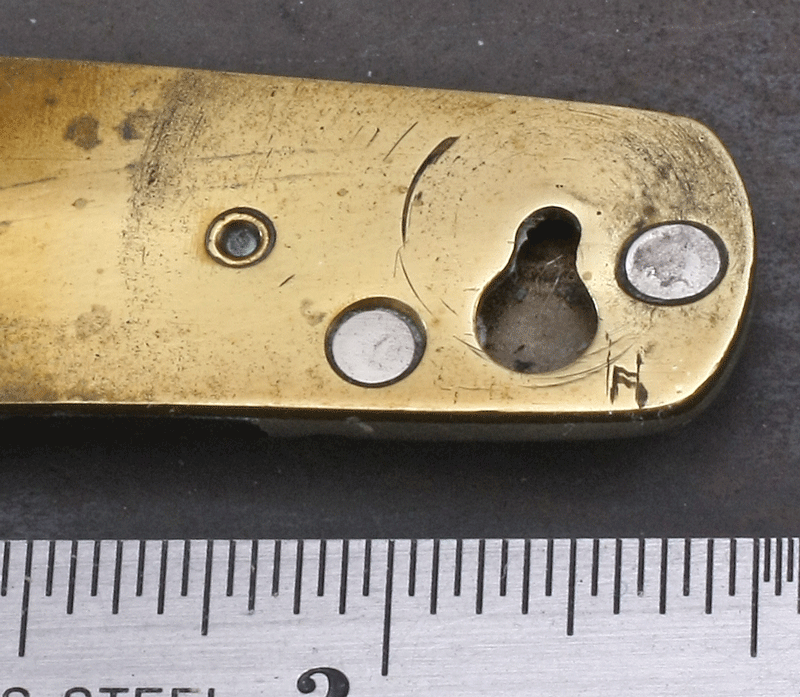
Next in line is the method Camillus made Buck 300's, using the thru the bolster pin method. You can see how the pin's were flared at the ends to hold in place. This is why if you drive out a pin (and enlarge the bolster holes), you have to have a heck of a time getting the new pin to fill the bolster hole to the edge.

The Buck factory made method using three springs. Top to bottom, left to right. Blade, pin, blade, spring. Spring, pin, spring. Blade, pin, blade, spring. As you can see in the middle, the spring takes up the full space on this end, the end with no blade.

Finally for my part, this is a photo inside the modern Buck 300, the SS liner has funnel like holes that plastic pins formed with the knife scale go thru and then are pressed and melted to be flat to hold the scale to the liner.
Come on know some of you at least have some production Model 100 fixed blade blade's you can show how the handle scales are attached.
How blades are attached in Model 300s. Bolsters are sliced thru the blade pins.
Model 301, first model made by Schrade under contract by Buck. Made using hidden bolster pin method. 'Swinden Key'.

Here is a photo of the side of the Schrade made Buck, the blades were put on the key pin, then both 'rivet like heads' were formed and then the heads slipped into the liner keyhole. This way no bolster pins show. But, they had issues with the strength of the brass.
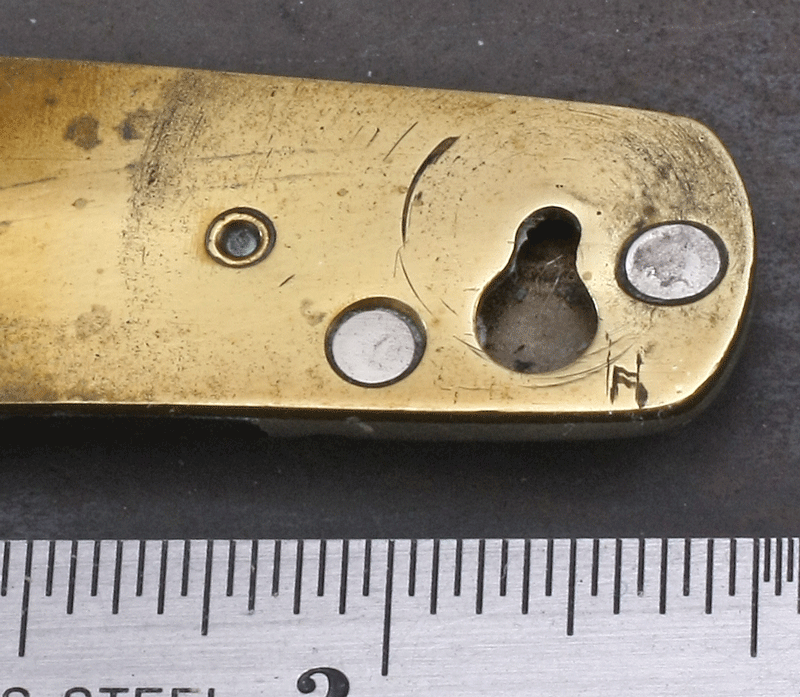
Next in line is the method Camillus made Buck 300's, using the thru the bolster pin method. You can see how the pin's were flared at the ends to hold in place. This is why if you drive out a pin (and enlarge the bolster holes), you have to have a heck of a time getting the new pin to fill the bolster hole to the edge.

The Buck factory made method using three springs. Top to bottom, left to right. Blade, pin, blade, spring. Spring, pin, spring. Blade, pin, blade, spring. As you can see in the middle, the spring takes up the full space on this end, the end with no blade.

Finally for my part, this is a photo inside the modern Buck 300, the SS liner has funnel like holes that plastic pins formed with the knife scale go thru and then are pressed and melted to be flat to hold the scale to the liner.

Come on know some of you at least have some production Model 100 fixed blade blade's you can show how the handle scales are attached.
Last edited: