- Joined
- Jul 3, 2022
- Messages
- 145
Hi everyone, I am an apprentice bladesmith with ABS with about 1 year down and 2 to go before I can submit knives for my journeyman examination. With only 2 attempts to make a blade, a reasonable person might assume that I am counting unhatched chicks. I have been rebuilding machines, fabricating kit grinders, designing and stocking most things a bladesmith needs for the smooth means of seeing a drawing come to life. The knife community has been out of this world and so many of them have kept me out of the ditches.
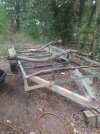
It took me quite a while to find a suitable shop frame on two axles; But, they are atually a thing. It also took me quite awhile to treat and repaint the metal on account of my concerns over spontaneous human combustion these past couple of months. So, now I get to go to the steel yard and get some angle and plate to shore up support for the heavier machines. The Harig 612 is 900lbs and the press is based in 1.5 x 5 cold finished flat bar; So, it will most likely go north of 1K.. I can calc the area of the steel that gets left after I get that big boy together. Press is going to have 25 tons with a frame that can upgrade to 50. I just like a big bowl for my ice cream, I reckon.
I would like to keep this project in front of anyone wants to follow it. My initial idea being perhaps I might be useful to the newer smiths, being that I have learned so much about the tooling side from never having a metal oriented background.
Wait until we homemade hoist that griinder onto this thing! LOL!!!
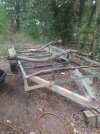
It took me quite a while to find a suitable shop frame on two axles; But, they are atually a thing. It also took me quite awhile to treat and repaint the metal on account of my concerns over spontaneous human combustion these past couple of months. So, now I get to go to the steel yard and get some angle and plate to shore up support for the heavier machines. The Harig 612 is 900lbs and the press is based in 1.5 x 5 cold finished flat bar; So, it will most likely go north of 1K.. I can calc the area of the steel that gets left after I get that big boy together. Press is going to have 25 tons with a frame that can upgrade to 50. I just like a big bowl for my ice cream, I reckon.
I would like to keep this project in front of anyone wants to follow it. My initial idea being perhaps I might be useful to the newer smiths, being that I have learned so much about the tooling side from never having a metal oriented background.
Wait until we homemade hoist that griinder onto this thing! LOL!!!