- Joined
- Oct 18, 2018
- Messages
- 7,877
A bit embarrassed about asking this, but I've made enough knives by now that I feel I Should have a better grasp of this....
How do you finish your Large sweeping Inside radius? Where my finger is pointing I like to have a gentle, radius where it leaves the handle, and enters the blade going to the point. On top/spine.
Idk how big it is, I'm guessing 10-20 feet in diameter, idk?
Funny, but small inside radius I'm good at finishing with files, and Dremel. It's the huge ones I get more visibly "wavey"
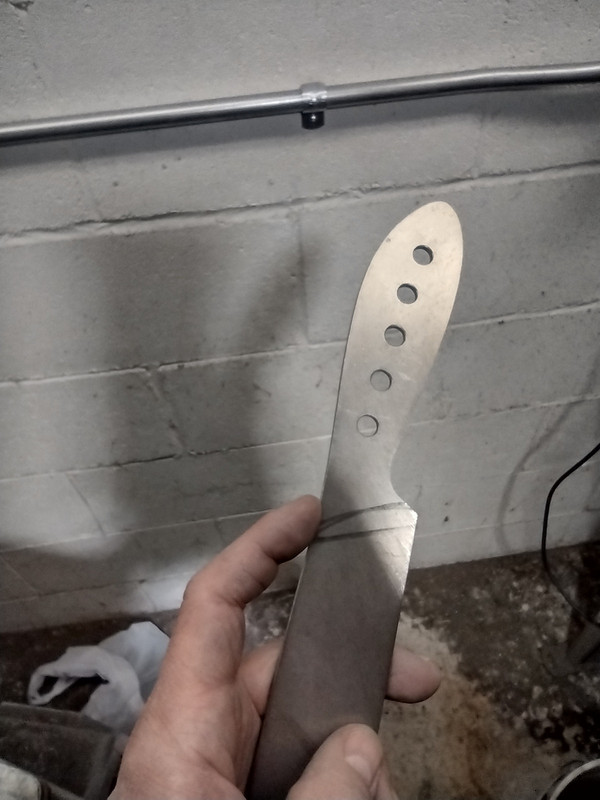
Currently I profile it just fine on my 2x72 belt running perpendicular. I'm good at that.
Then I clean it up running parallel on my belt, but I can only do so much on my metal platen wheels.
It's pretty rough. Would rubber contact wheels make much of a difference? (I have a small 3" one somewhere, but I really haven't used it much.)
So then I try cleaning them up and blend the profile with a diamond file. I try smoothing out the peaks and valleys, but it's kinda wavey. Slightly. Definitely not crisp.
I don't need for it to be perfect, as my knives aren't finished to the extreme. But I want to continue to step up my game. This has been bugging me.
How do you finish your Large sweeping Inside radius? Where my finger is pointing I like to have a gentle, radius where it leaves the handle, and enters the blade going to the point. On top/spine.
Idk how big it is, I'm guessing 10-20 feet in diameter, idk?
Funny, but small inside radius I'm good at finishing with files, and Dremel. It's the huge ones I get more visibly "wavey"
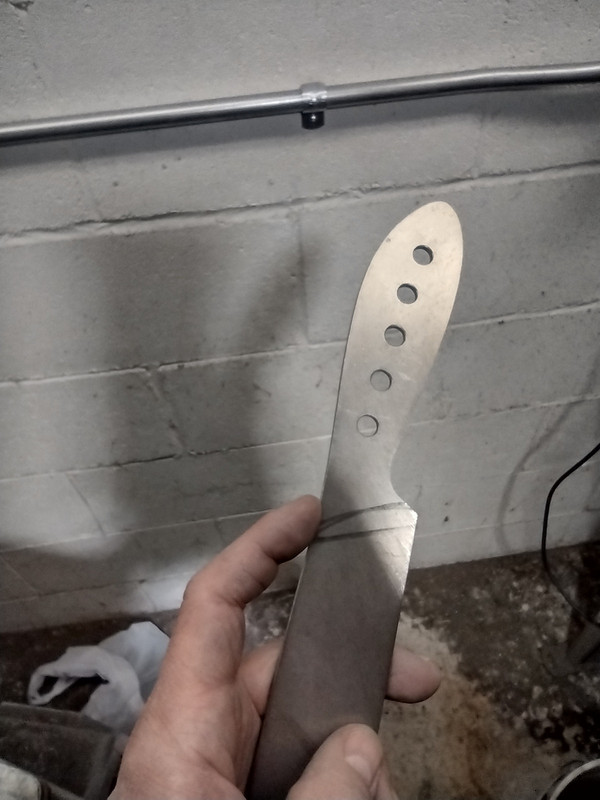
Currently I profile it just fine on my 2x72 belt running perpendicular. I'm good at that.
Then I clean it up running parallel on my belt, but I can only do so much on my metal platen wheels.
It's pretty rough. Would rubber contact wheels make much of a difference? (I have a small 3" one somewhere, but I really haven't used it much.)
So then I try cleaning them up and blend the profile with a diamond file. I try smoothing out the peaks and valleys, but it's kinda wavey. Slightly. Definitely not crisp.
I don't need for it to be perfect, as my knives aren't finished to the extreme. But I want to continue to step up my game. This has been bugging me.