fq55
Knifemaker / Craftsman / Service Provider
- Joined
- Feb 27, 1999
- Messages
- 2,308
I actually had some time and decided to do something that had been on my list for years.
Make a sheath for one of my prized possessions. A PJ Tomes Clip Point Hunter that I carried on my second tour in Iraq.
The original sheath had stitching come come loose and was not in the best shape
Let me preface this by saying that I do not have the proper tools or materials and made due as best I could. I’m not thrilled with the results as the sheath is a bit ugly but in a way it makes sense.
I used one of
Horsewright
sheaths as inspiration.
The material I used were 5.5oz Wickett & Craig tan English Bridle and Horween 2oz Roadmaster.
I just used what I had and at the moment this Bridle was the thickest Veg tanned leather I have on hand.
Here is my sheath I have from Horsewright
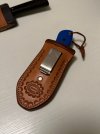
First thing I did was take the original sheath apart to use as a template.
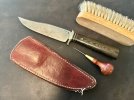
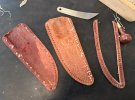
I didn’t know how good my tracing would be so I decided to trace on the flesh side. I traced only one side and used that as my template for the other panel.
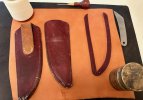
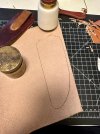
I used a utility knife holder to cut the straight lines and a Warren Thomas Kiridashi for the round portion.
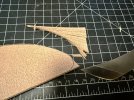
Now for the lining I had some Horween roadmaster leftovers that I thought would work well. It’s a very soft distressed cow leather that hides scuffs well.
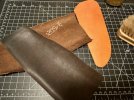
I don’t use barge cement and instead have used intercom eco stick 1816B with good results. Time will tell if it’s good for this application.
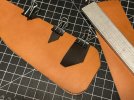
I let this dry for a bit and to be continued down below.
Make a sheath for one of my prized possessions. A PJ Tomes Clip Point Hunter that I carried on my second tour in Iraq.
The original sheath had stitching come come loose and was not in the best shape
Let me preface this by saying that I do not have the proper tools or materials and made due as best I could. I’m not thrilled with the results as the sheath is a bit ugly but in a way it makes sense.
I used one of

The material I used were 5.5oz Wickett & Craig tan English Bridle and Horween 2oz Roadmaster.
I just used what I had and at the moment this Bridle was the thickest Veg tanned leather I have on hand.
Here is my sheath I have from Horsewright
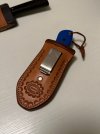
First thing I did was take the original sheath apart to use as a template.
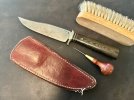
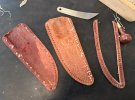
I didn’t know how good my tracing would be so I decided to trace on the flesh side. I traced only one side and used that as my template for the other panel.
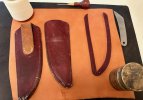
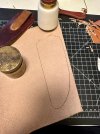
I used a utility knife holder to cut the straight lines and a Warren Thomas Kiridashi for the round portion.
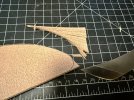
Now for the lining I had some Horween roadmaster leftovers that I thought would work well. It’s a very soft distressed cow leather that hides scuffs well.
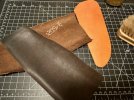
I don’t use barge cement and instead have used intercom eco stick 1816B with good results. Time will tell if it’s good for this application.
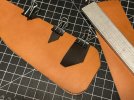
I let this dry for a bit and to be continued down below.
Last edited: