- Joined
- Jan 20, 2018
- Messages
- 34
Hi there,
I wanted to use my propane tank gas forge for the first time and started to slowly heat it up, but apparently I didn't let the cement dry long enough, resulting in a loud "bang", a huge flame and a hole in my cement walling.
First of all, do you think the big flame that shot out of both ends of the forge was caused by the cement coming off or the other way round?
Second, how do I fix the holes? Should I just put some new cement into them and hope that everything bonds together nicely?
I'm a little bit lost, so any help would be greatly appreciated
Jonas
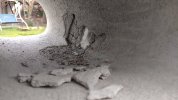
I wanted to use my propane tank gas forge for the first time and started to slowly heat it up, but apparently I didn't let the cement dry long enough, resulting in a loud "bang", a huge flame and a hole in my cement walling.
First of all, do you think the big flame that shot out of both ends of the forge was caused by the cement coming off or the other way round?
Second, how do I fix the holes? Should I just put some new cement into them and hope that everything bonds together nicely?
I'm a little bit lost, so any help would be greatly appreciated

Jonas
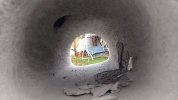
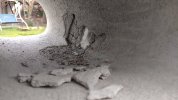