We have successfully using digital-controlled low temp salt pot for quenching and tempering carbon steel like 52100, 5160 or O1 for a while.
It is definitely a great and worth equipment since it will significantly reduce chance of distortion by large margin. By quenching the blade at slightly above MS and equalize for short time resulting a harder as quenched and noticeable tougher blade too. It properly beacuse the slower and more uniformly distribution of martenite forming and auto tempering effect.
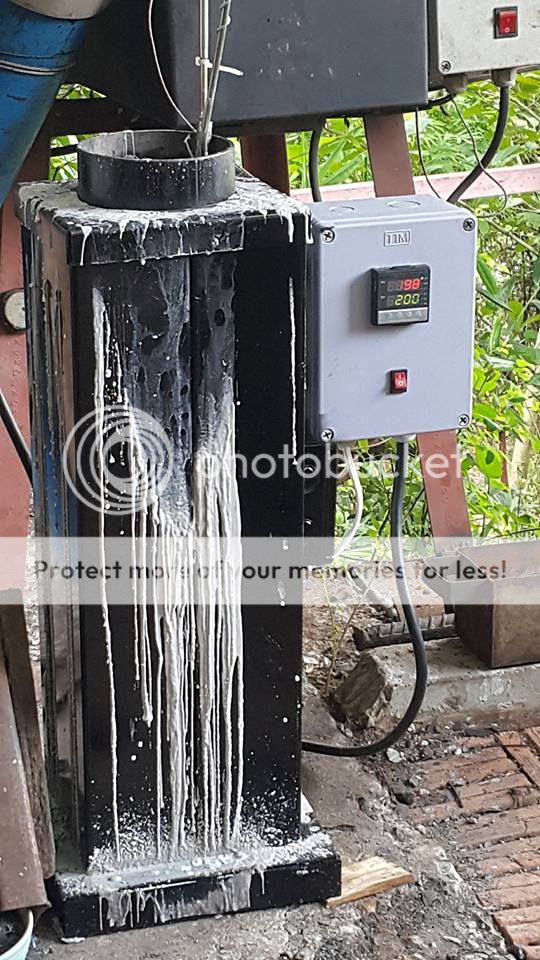
The next project would be high temp salt for austenitizing purpose but this time I aimed for HTing stainless/high speed steel.
The reason why I want to try high-temp salt because in theory, molten salt HTing will significantly shorten the soaking time thus minimize grain growth and primary carbide agglomeration. Potentially better and finer grain that can't be achieved with vacuum or atmosphere HT environment.
But the high temp salt pot gonna be much more dangerous and challenging. I have never seen any knife makers who use salt to HTing high alloy steel before. I pretty sure Cashen, Wheeler and others ABS member who use high temp salt are only working with low alloy carbon steel.
But to operated 2200F salt may require some knowledge about material properties that why I need to ask for suggestion here. Noted that I would use digital-controlled electric kiln to do the pre-heating.
From what I planned, the heating method would be gas-fired immersion tubes. The tube gonna be salt container.
The dimension of the tube would be about 8" diameter x 24" x 0.5" wall thickness. But I'm not sure if 304 or 416 tube has heat/corrosion resistance enough to withstand the direct fire and 2000F+ molten salt in long term.
Anyone have knowledge or experience about that? Otherwise I may have to get titanium tube which will cost me over 2,000 USD just fore the tube alone.
The second part is the quench media. Low temp salt would be the ideal but my molten salt can be operated at only 650F maximum. From what I have seen most HSS/cold work data sheet require quenching in 1000F molten salt. Not sure what will happen if I quench them in 400F salt?
I would appreciate any opinion especially from the expert who working and having real experience in these filed like Larrin or Devin Thomas.
It is definitely a great and worth equipment since it will significantly reduce chance of distortion by large margin. By quenching the blade at slightly above MS and equalize for short time resulting a harder as quenched and noticeable tougher blade too. It properly beacuse the slower and more uniformly distribution of martenite forming and auto tempering effect.
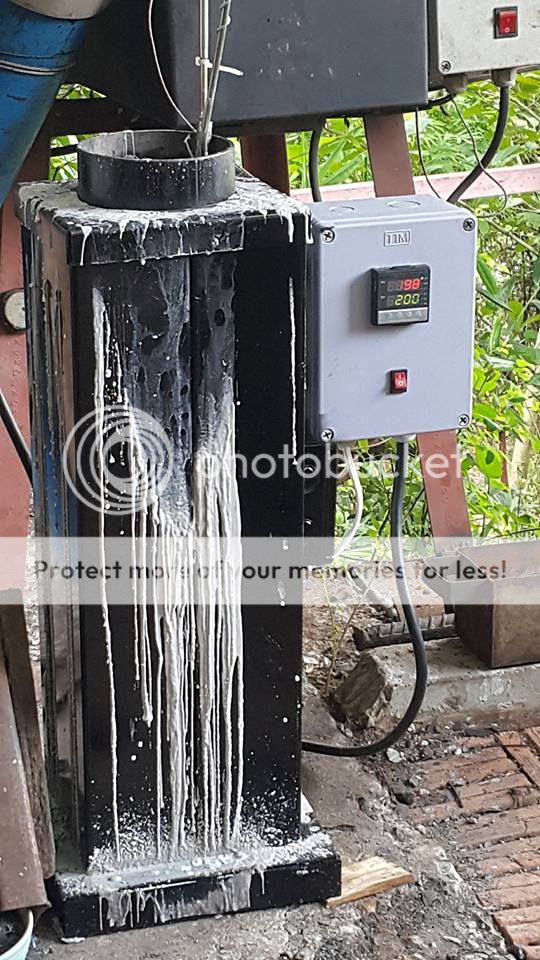
The next project would be high temp salt for austenitizing purpose but this time I aimed for HTing stainless/high speed steel.
The reason why I want to try high-temp salt because in theory, molten salt HTing will significantly shorten the soaking time thus minimize grain growth and primary carbide agglomeration. Potentially better and finer grain that can't be achieved with vacuum or atmosphere HT environment.
But the high temp salt pot gonna be much more dangerous and challenging. I have never seen any knife makers who use salt to HTing high alloy steel before. I pretty sure Cashen, Wheeler and others ABS member who use high temp salt are only working with low alloy carbon steel.
But to operated 2200F salt may require some knowledge about material properties that why I need to ask for suggestion here. Noted that I would use digital-controlled electric kiln to do the pre-heating.
From what I planned, the heating method would be gas-fired immersion tubes. The tube gonna be salt container.
The dimension of the tube would be about 8" diameter x 24" x 0.5" wall thickness. But I'm not sure if 304 or 416 tube has heat/corrosion resistance enough to withstand the direct fire and 2000F+ molten salt in long term.
Anyone have knowledge or experience about that? Otherwise I may have to get titanium tube which will cost me over 2,000 USD just fore the tube alone.
The second part is the quench media. Low temp salt would be the ideal but my molten salt can be operated at only 650F maximum. From what I have seen most HSS/cold work data sheet require quenching in 1000F molten salt. Not sure what will happen if I quench them in 400F salt?
I would appreciate any opinion especially from the expert who working and having real experience in these filed like Larrin or Devin Thomas.
Last edited: