- Joined
- Dec 7, 2008
- Messages
- 7,187
Some woods if cut correctly will show really cool flecks or patterns like snakeskin. Some of the more obvious woods are oak, sycamore and lacewood.
One of the other forum members in Hawaii has some macadamia logs he will be cutting. Macadamia is one of the woods that can show the flecks when cut correctly. This post is a copy of the message I sent to him advising how to cut the wood.
For illustration purposes I am using 2 pieces of lacewood cut from the same chunk of wood. The end grain is facing you at the bottom.
The medullar rays are the lines going horizontally and the growth rings are the vertical lines. The growth rings are the circles you see when looking at the end of a log. The medullar rays radiate outward from the center of the log to the outer surface. They will be perpendicular to the growth rings. Most woods that have distinct medullar rays will produce flecks if the lumber is cut to follow the rays. Examples, oak, sycamore and lacewood. Looking at the surface of these 2 blocks you can see the difference in the flecks when the rays are followed vs when the cut is off by even a slight angle. I hope this makes sense. Please excuse the spelling.
There is contradictory information on the internet as to what is quarter sawing and what is rift sawing. What I call quarter sawing is cutting perpendicular to the growth rings as seen in the left block. Rift sawing is at an angle to the growth rings like the right block.
One of the other forum members in Hawaii has some macadamia logs he will be cutting. Macadamia is one of the woods that can show the flecks when cut correctly. This post is a copy of the message I sent to him advising how to cut the wood.
For illustration purposes I am using 2 pieces of lacewood cut from the same chunk of wood. The end grain is facing you at the bottom.
The medullar rays are the lines going horizontally and the growth rings are the vertical lines. The growth rings are the circles you see when looking at the end of a log. The medullar rays radiate outward from the center of the log to the outer surface. They will be perpendicular to the growth rings. Most woods that have distinct medullar rays will produce flecks if the lumber is cut to follow the rays. Examples, oak, sycamore and lacewood. Looking at the surface of these 2 blocks you can see the difference in the flecks when the rays are followed vs when the cut is off by even a slight angle. I hope this makes sense. Please excuse the spelling.
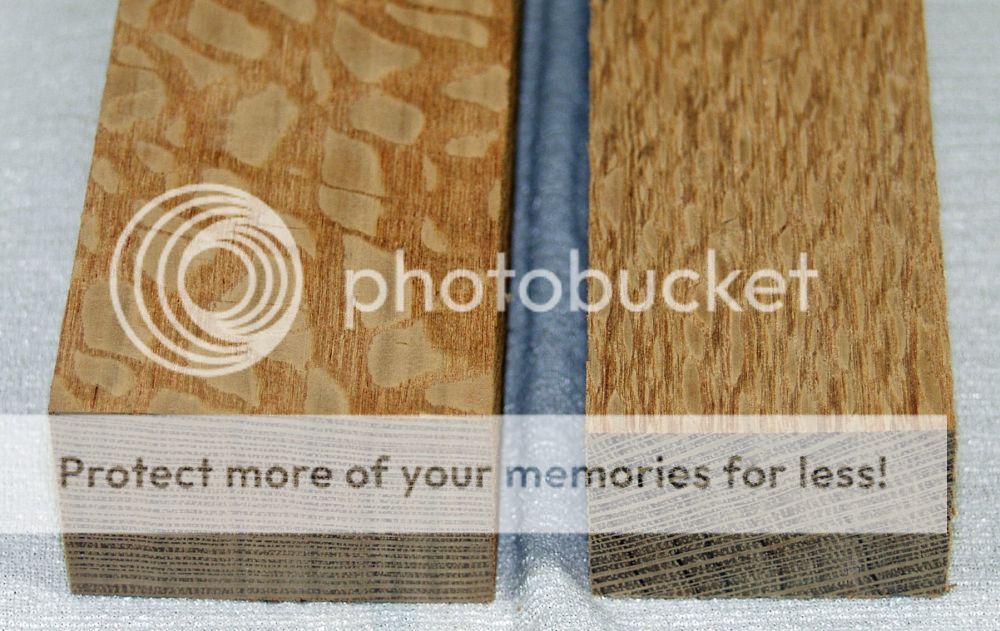
There is contradictory information on the internet as to what is quarter sawing and what is rift sawing. What I call quarter sawing is cutting perpendicular to the growth rings as seen in the left block. Rift sawing is at an angle to the growth rings like the right block.