- Joined
- Jul 22, 2021
- Messages
- 119
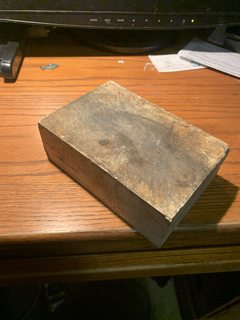
I found a rather beefy wetstone in a restaurant cellar awhile back. I suspect the stone is from the 60's or maybe even older. I don't know why a wetstone would be so thick at only 6" long. Overall dimensions are 6" X 4" X 2" , and appears to be mostly flat and fine textured. Is there a certain kind of file required to flatten it, or can I use sandpaper on a flat surface? It seems like a soft stone, and I'm not even sure it will sharpen the supersteel knives i tend to carry.
What will the usefulness be with a soft, perhaps 1200 grit stone? Also, how do I determine if it really is a wetstone, or oiled stone?
Thank for any insight!