- Joined
- Feb 16, 2010
- Messages
- 3,668
For a long time, it's been believed that a large, high speed centrifugal blower is needed for a blown burner. Normally, it's a Dayton producing 178CFM. Here is a tested and proven 200k burner running off a 12vdc blower at 20 watts. A simple and cheap pwm speed controller adjusts the blower speed, instead of a gate valve.
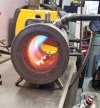
18" shell, 16" long x 5" chamber
Single 45CFM blower with .062" orifice @ 20 PSI producing 200k BTU (too big) split into two channels
It runs fine down to about 25k BTU
Plicast LWI 24 chamber
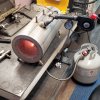
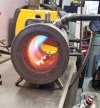
18" shell, 16" long x 5" chamber
Single 45CFM blower with .062" orifice @ 20 PSI producing 200k BTU (too big) split into two channels
It runs fine down to about 25k BTU
Plicast LWI 24 chamber