- Joined
- Feb 18, 2016
- Messages
- 2,209
I've been stalking this forum for a couple of years now. Obsessively reading, annoying everyone with questions. And I'm honored to try and give back so, here we go!
First here's what were building
First: but something to hold everything. This is what I bought
It has a handle and feet on what will be the front.
2nd step: take and angle grinder and cut the front off right behind the weld. Dont worry you'll see it. Then measure 12in back, make a line cut again. It should look like this:
Cut the brass air outlet out or if you can just unscrew it.
3rd: cut a hole at about 2oclock going almost straight in so it the flame will swirl. The hole should be half an inch bigger than whatever your burner pipe is. In this case my burner is 3/4 in so I cut a 1 1/4 hole. (10 Bucks for a hole saw at home depot)
4th: insert a 2in piece of pipe the diameter of your hole. And weld in place. (If you dont have a welder forget the 2in pipe and buy this:
Put it in upside down and screw it on)
5th: buy some 2in thick 12x24 kaowool i got mine from iyaknowsbest on Ebay. Really fast shipping and hes a good guy. Link to his Ebay store: https://ebay.com/usr/iyaknowsbest (with my particular air tank, the kaowool was just a couple inches too short In diameter. Luckily this guy also sells 2in sections. For this reason so just go ahead and get one while your at it.)
Put on some gloves and probably a respirator. Roll up the kaowool and shove it in your forge.
Now you got something like this
(Note the gap on top, not good)
6: take your refractory cement (Mizzou, satanite, greencast, kast-o-lite) and coat the kaowool. (I suggest buying a rigidizer to saturate the wool first. I didn't and I regret it. Learn from my mistakes)
I used 5 lbs of kast-o-lite and got it from here: https://hard-luck-forge-supply.myshopify.com/ they also sell rigidizer. Best prices I saw and free shipping. (Refer to their website on how to properly mix and apply your refractory)
Now we have something like this
After you make one decently thin coat let it sit for a couple of hours. Then crank on the forge for a minute or so and "bake" it on.
2nd coat:
do this 3 times.
I'm about to go in the shop and apply my 3rd coat, let it sit overnight (its 1am here) and turn on the burner for the final "bake" tomorrow.
If you plan on heat treating in your forge I suggest buying a muffle, thermocouple and pyrometer.
Muffle is just a pipe that fits in the forge. Blade and thermocouple go in pipe. Pipe gets hot and evenly heats the blade. The thermocouple is sitting next to the blade so your getting an accurate reading on the temp of the blade. This way you can optimize your heat treating process.
Thermocouple I plan on buying: https://www.omega.com/pptst/KTSS_JTSS_chb.html?bt=cart
It's the omega type K thermocouple with their XL ceramic sheath. Part number KTXL-14U-12.
Pyrometer will be
https://www.lightobject.com/mobile/JLD7100-PID-Temperature-Controller-P44.aspx
The thermocouple and pyrometer set up was recommended by @Ed Caffrey
On his website here:
https://www.caffreyknives.net/forge_pyrometer.html
EDIT to add: I plan on buying 3 hard brick firebricks 2 to close up the back and 1 as a forge floor.
And that should do it. This is is my first forge build. I'm sure it's far from perfect but its functional. And will serve me well for years. If you see an area I can improve please let me know. I hope this helps someone.
I'm a huge proponent in giving back to this community. I've got so much information I'll never be able to repay most of it.
First here's what were building
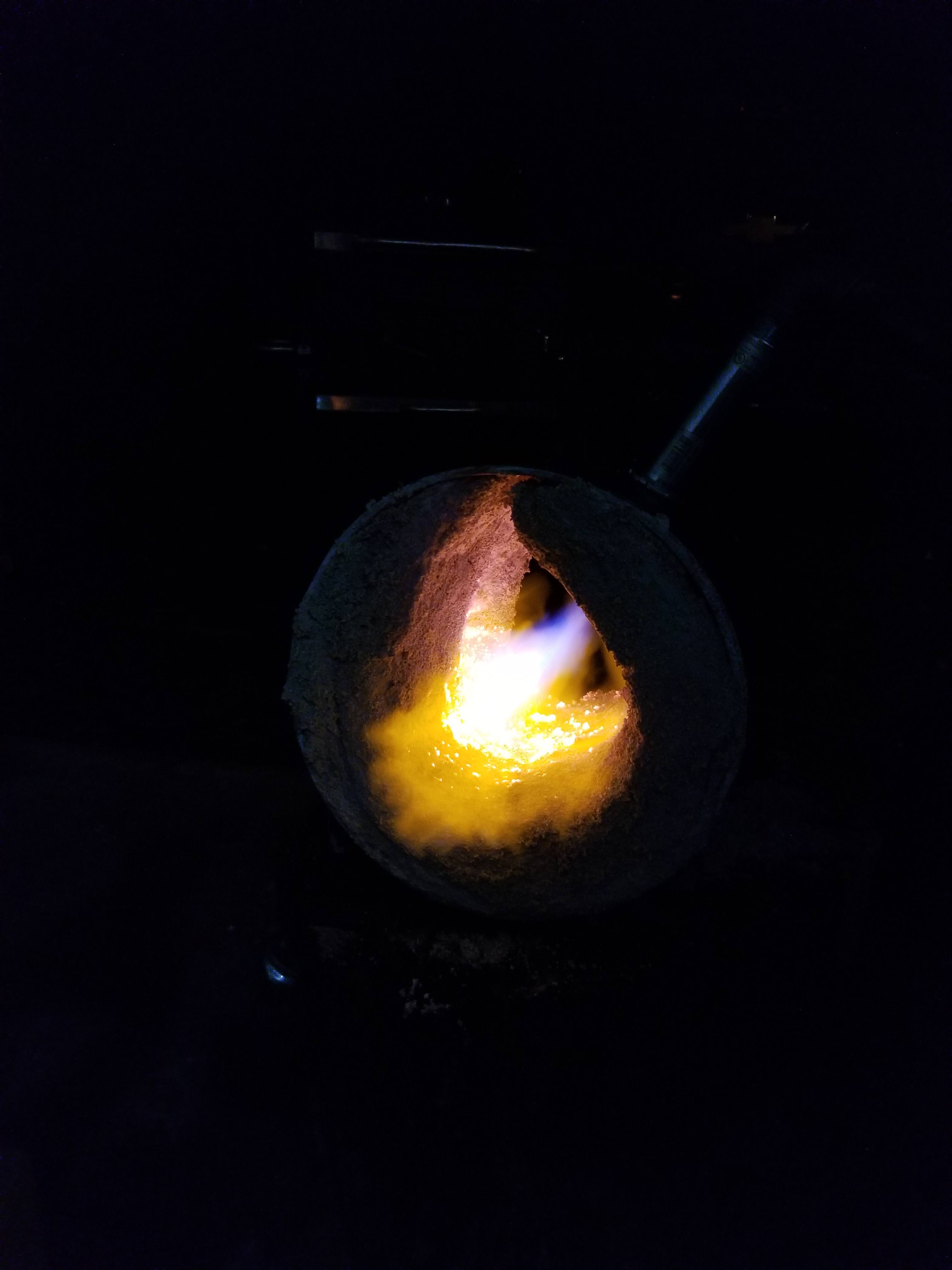
First: but something to hold everything. This is what I bought

It has a handle and feet on what will be the front.
2nd step: take and angle grinder and cut the front off right behind the weld. Dont worry you'll see it. Then measure 12in back, make a line cut again. It should look like this:

Cut the brass air outlet out or if you can just unscrew it.
3rd: cut a hole at about 2oclock going almost straight in so it the flame will swirl. The hole should be half an inch bigger than whatever your burner pipe is. In this case my burner is 3/4 in so I cut a 1 1/4 hole. (10 Bucks for a hole saw at home depot)
4th: insert a 2in piece of pipe the diameter of your hole. And weld in place. (If you dont have a welder forget the 2in pipe and buy this:

Put it in upside down and screw it on)
5th: buy some 2in thick 12x24 kaowool i got mine from iyaknowsbest on Ebay. Really fast shipping and hes a good guy. Link to his Ebay store: https://ebay.com/usr/iyaknowsbest (with my particular air tank, the kaowool was just a couple inches too short In diameter. Luckily this guy also sells 2in sections. For this reason so just go ahead and get one while your at it.)
Put on some gloves and probably a respirator. Roll up the kaowool and shove it in your forge.
Now you got something like this

(Note the gap on top, not good)
6: take your refractory cement (Mizzou, satanite, greencast, kast-o-lite) and coat the kaowool. (I suggest buying a rigidizer to saturate the wool first. I didn't and I regret it. Learn from my mistakes)
I used 5 lbs of kast-o-lite and got it from here: https://hard-luck-forge-supply.myshopify.com/ they also sell rigidizer. Best prices I saw and free shipping. (Refer to their website on how to properly mix and apply your refractory)
Now we have something like this
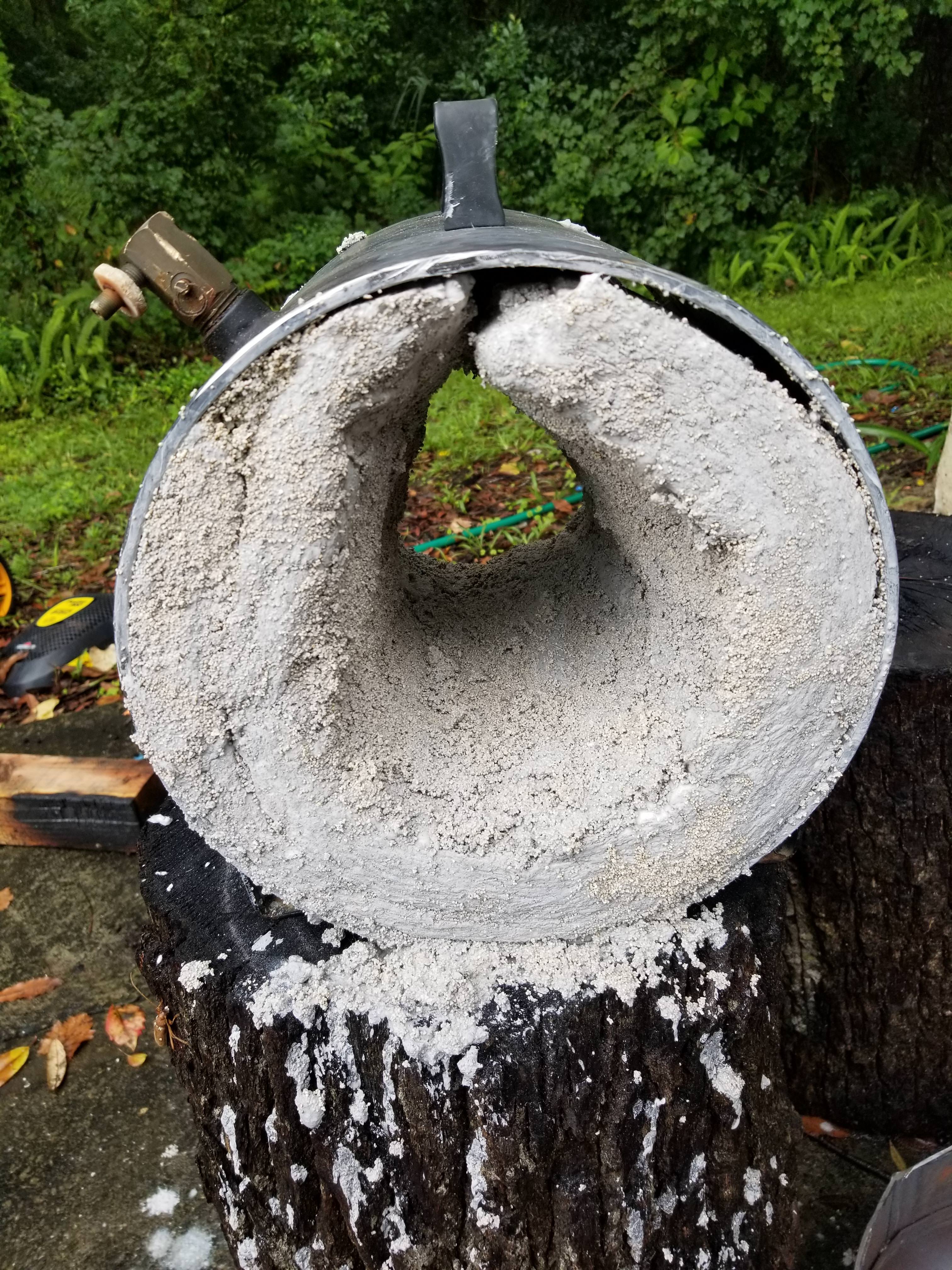
After you make one decently thin coat let it sit for a couple of hours. Then crank on the forge for a minute or so and "bake" it on.
2nd coat:
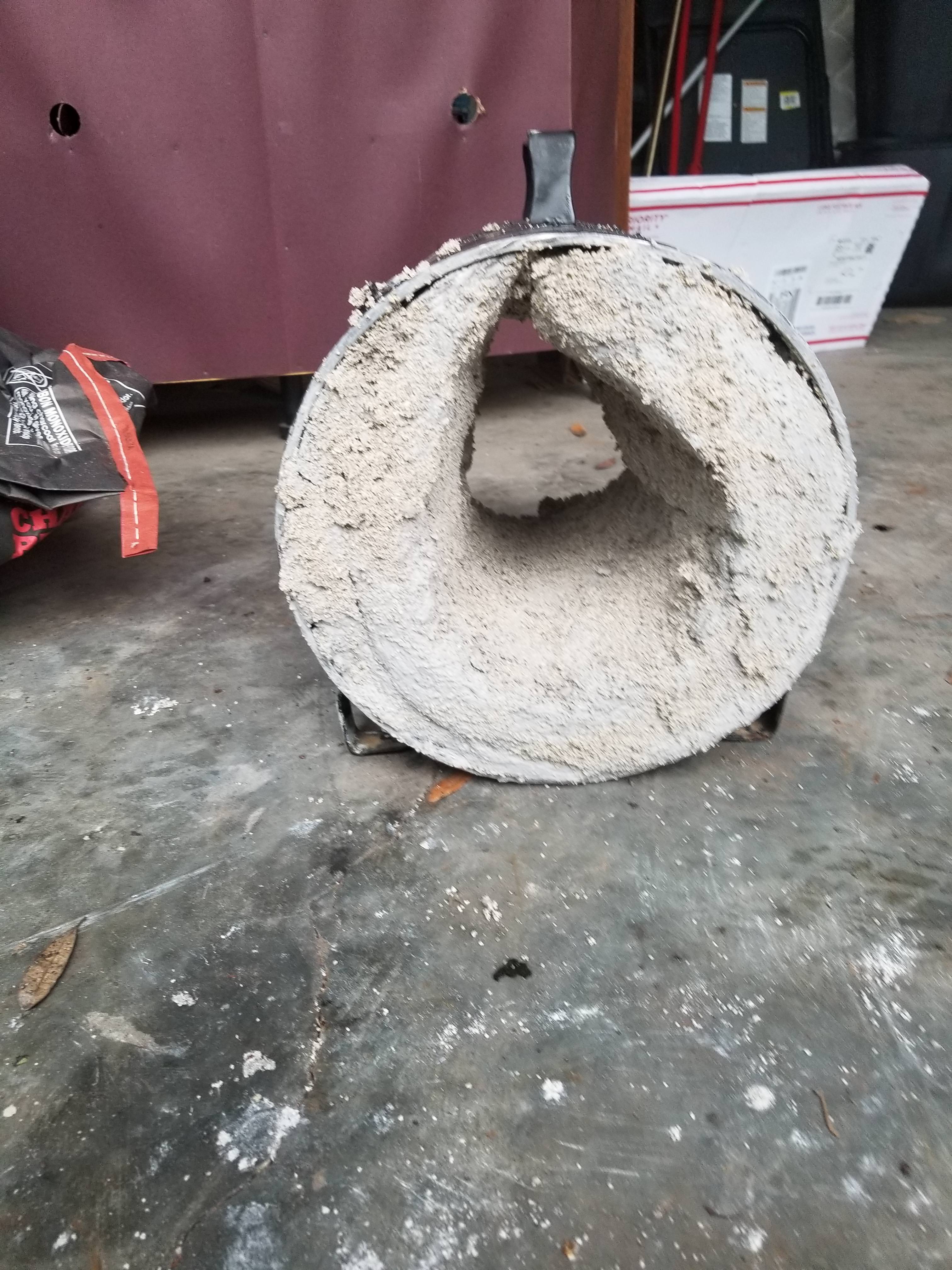
I'm about to go in the shop and apply my 3rd coat, let it sit overnight (its 1am here) and turn on the burner for the final "bake" tomorrow.
If you plan on heat treating in your forge I suggest buying a muffle, thermocouple and pyrometer.
Muffle is just a pipe that fits in the forge. Blade and thermocouple go in pipe. Pipe gets hot and evenly heats the blade. The thermocouple is sitting next to the blade so your getting an accurate reading on the temp of the blade. This way you can optimize your heat treating process.
Thermocouple I plan on buying: https://www.omega.com/pptst/KTSS_JTSS_chb.html?bt=cart
It's the omega type K thermocouple with their XL ceramic sheath. Part number KTXL-14U-12.
Pyrometer will be
https://www.lightobject.com/mobile/JLD7100-PID-Temperature-Controller-P44.aspx
The thermocouple and pyrometer set up was recommended by @Ed Caffrey
On his website here:
https://www.caffreyknives.net/forge_pyrometer.html
EDIT to add: I plan on buying 3 hard brick firebricks 2 to close up the back and 1 as a forge floor.
And that should do it. This is is my first forge build. I'm sure it's far from perfect but its functional. And will serve me well for years. If you see an area I can improve please let me know. I hope this helps someone.
I'm a huge proponent in giving back to this community. I've got so much information I'll never be able to repay most of it.
Last edited: