- Joined
- Jan 21, 2005
- Messages
- 2,396
I set out Friday in search of some carbon steel scrap pipe for a forge, because what I was planning to use didn't pan out, when I stumbled onto what may be the perfect makeshift anvil. It is some kind of coupling I guess used in heavy lifting with cranes. A similar piece hade "4340-6" stamped into it, so I'm assuming this hunk of steel is forged 4340?
It weighs 194 lbs, I can still move it around, pick it up, etc., without too much strain, and it has a good clear ring, sharp edges, and great hammer rebound. I also found all the scrap pipe and steel I could ever want, the yard even cuts to size for a nominal fee. The anvil cost $64.
Here's some pics:
It weighs 194 lbs, I can still move it around, pick it up, etc., without too much strain, and it has a good clear ring, sharp edges, and great hammer rebound. I also found all the scrap pipe and steel I could ever want, the yard even cuts to size for a nominal fee. The anvil cost $64.
Here's some pics:

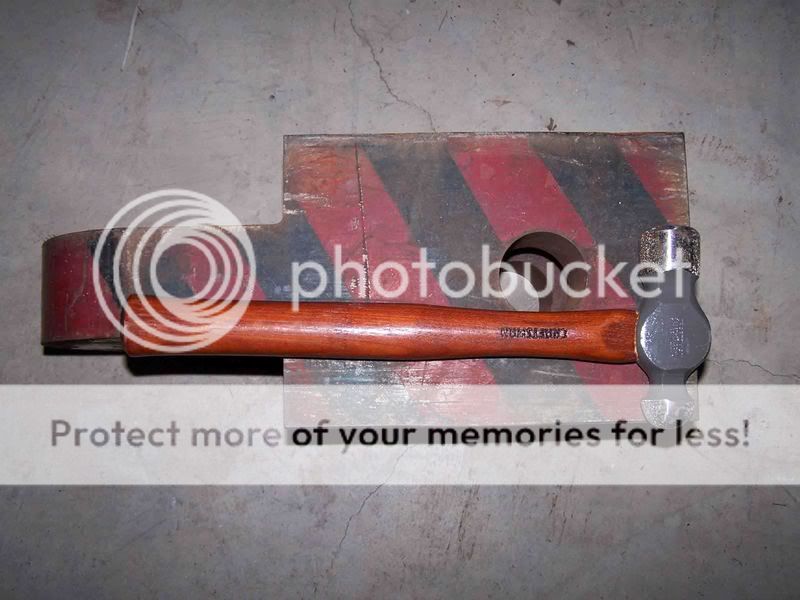