- Joined
- Jun 8, 2006
- Messages
- 254
I pulled an old 1x42 sander out of retirement and looked it over and found the tracking pulley had a crack. Soooo, cause I had the right size aluminum stock and machines I thought I would make all 3 pulleys from aluminum and eliminate that ever happening again. Not sure what I need it for yet. My Question : On the tracking pulley don't they have a slight crown in the center ? I cut about a 3 degree crown in one and stamped it with a C so not to mix it up. Does anybody have knowledge of how much crown in a 1" wide 3 1/2" pulley would be ? Heres a couple pics.
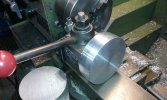
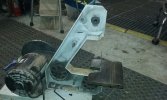
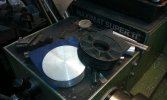
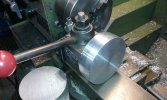