Hengelo_77
Basic Member
- Joined
- Mar 2, 2006
- Messages
- 6,217
I want to work with mammoth ivory for the first time.
In the back there are some small cracks. Should I fill them with super glue of will the epoxy from epoxying to the liner do the same?
(I will use a thin G10 liner)
And the stripes on the surface, do they go all the way trough or will I lose them if I contour the handle?
In the back there are some small cracks. Should I fill them with super glue of will the epoxy from epoxying to the liner do the same?
(I will use a thin G10 liner)
And the stripes on the surface, do they go all the way trough or will I lose them if I contour the handle?
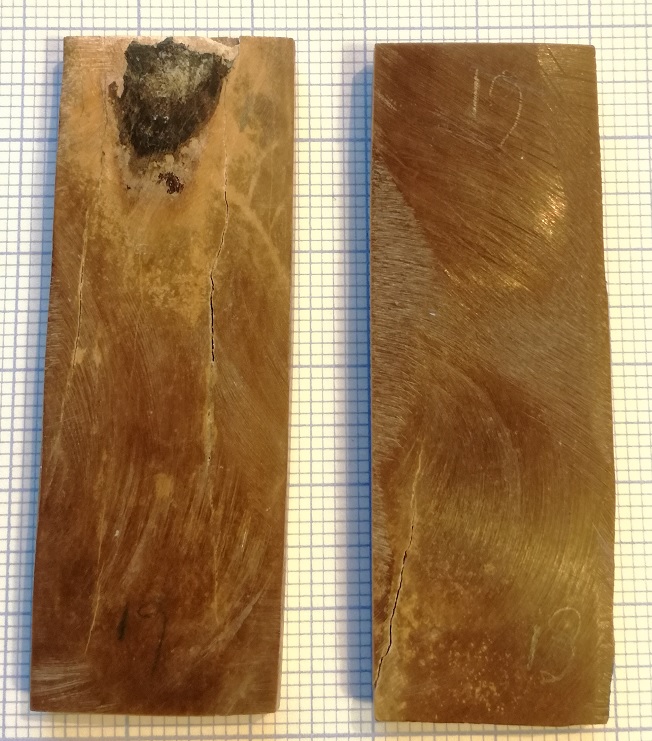
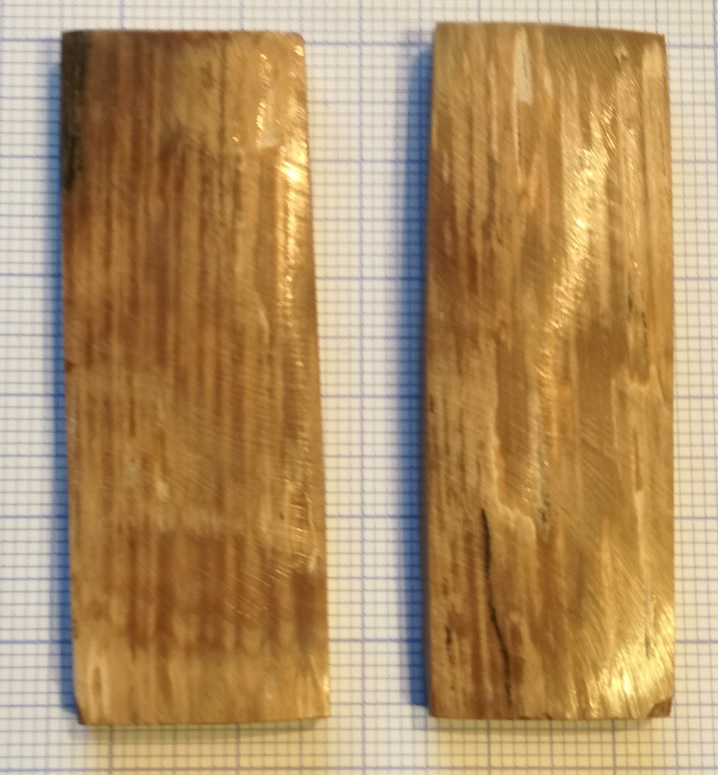