- Joined
- Oct 24, 2013
- Messages
- 906
This is my third forging but the first one I didn't set aside for another or toss in the scrap pile... Please critique the heck out of it as I have thick skin and am enjoying the learning aspect of this craft.
Blade Material: 5160 Leaf Spring
Handle: Elk
Design: Bowie rat-tail tang.
Hilt/Pommel: Forged; Copper, Stainless, and Bronze.
Pins: copper / stainless screws
OAL: 17.75"
Blade:
W:2.5"
L:10.5"
T: .25"
Weight: (guess) 2 pounds
I'm not happy with the end result, but I'm chalking it up to a learning experience.
Oops #1:
I'd originally gone with just the forged copper, but added the bronze after I cut the bolt welded to the tang. Had I just stuck with the copper it would have turned out a lot cleaner in the rear... The two botched phillips screws on the but are 3" in length and secured deep into the epoxy filled handle. The bolt at the end of the rat-tail is snug and wedged inside the antler to the point of not being able to be threaded any tighter due to the side walls of the bone. I peened a copper pin in place of the intended through bolt/nut as a fix.
Oops#2: I used spiderwire to fill the gaps between the antler / hilt & pommel. I need to find a better means of a cleaner filled gap...
Oops #3: went a lil crazy on jimping past my bed time... little marring on the left side of the blade...
I know its ridiculously large... this was my intent.
These mistakes wont continue onto my next project as I have a new found respect for sticking to the plan.
Please don't be shy, the only way one gets better is through knowing failure... Thank you for your advice, comments, critique, and compliments in advance... This was a fun endeavor to say the least...
Blade Material: 5160 Leaf Spring
Handle: Elk
Design: Bowie rat-tail tang.
Hilt/Pommel: Forged; Copper, Stainless, and Bronze.
Pins: copper / stainless screws
OAL: 17.75"
Blade:
W:2.5"
L:10.5"
T: .25"
Weight: (guess) 2 pounds
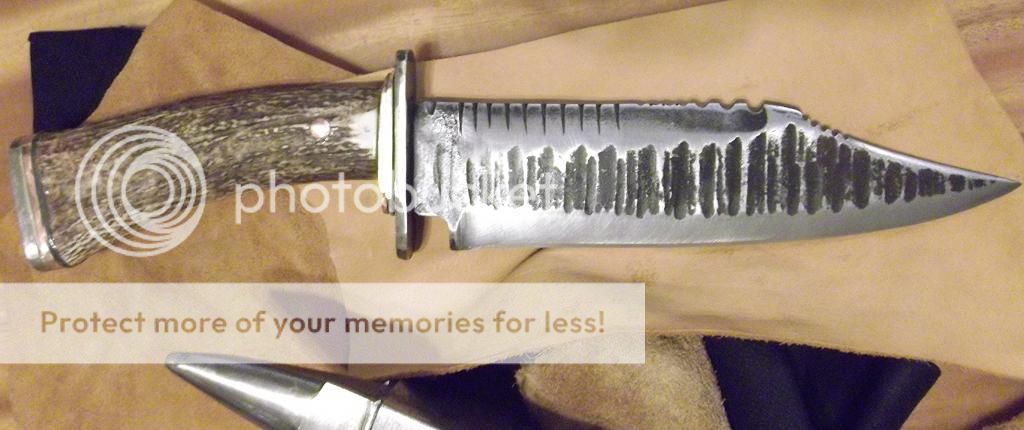
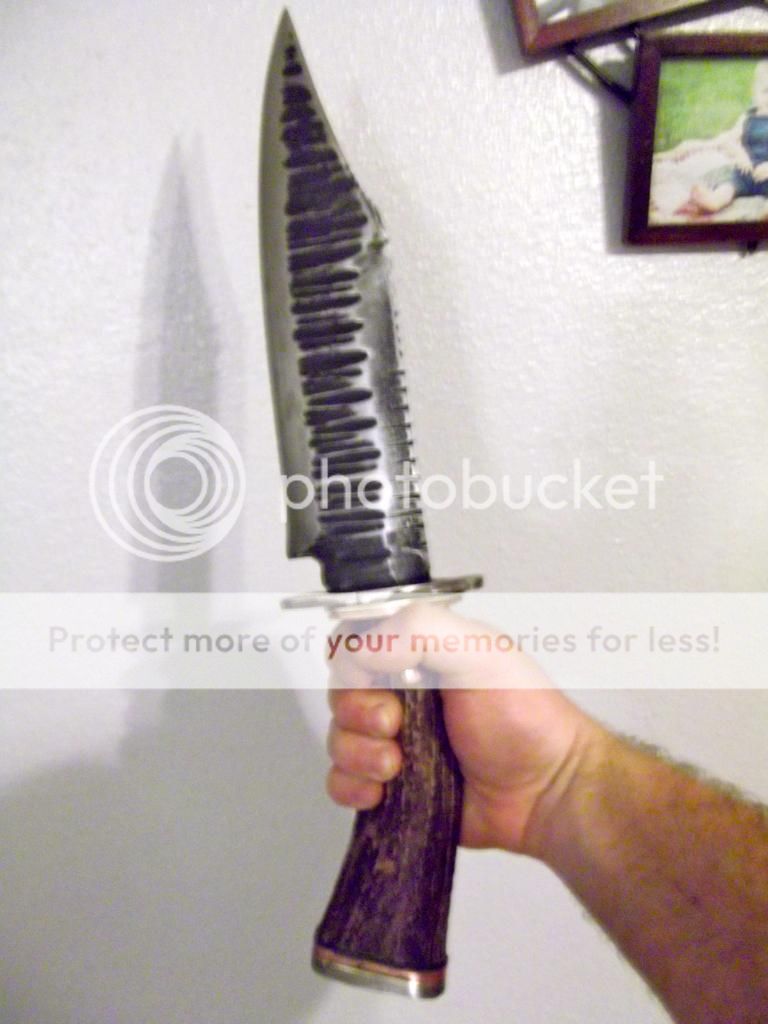


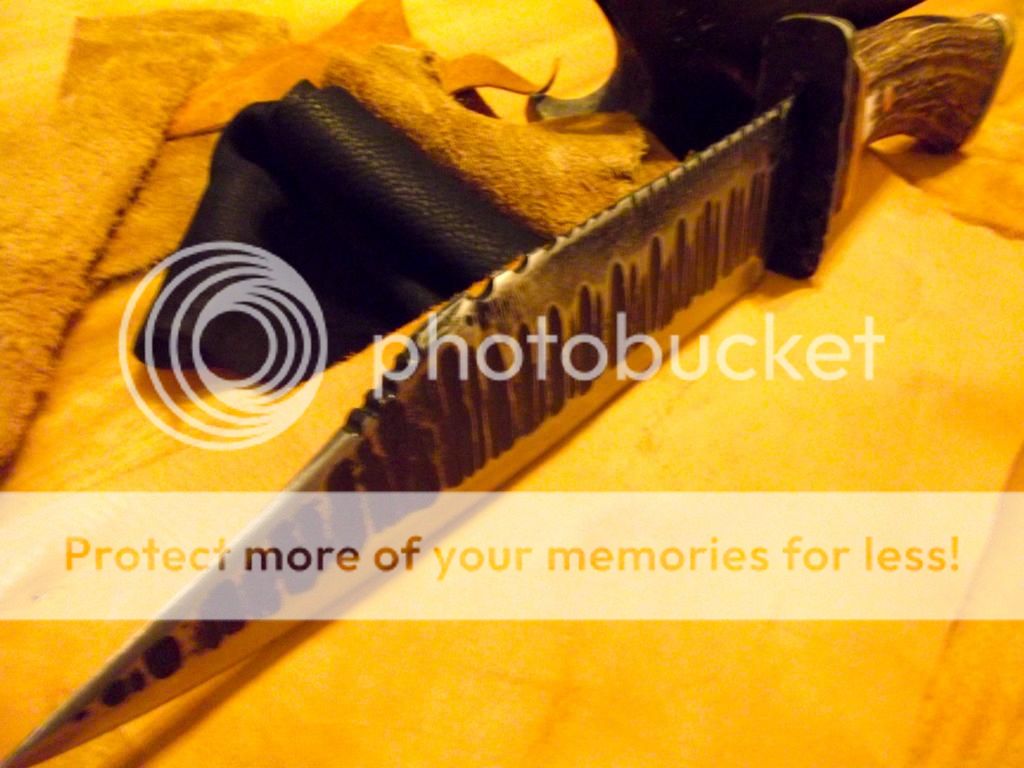


I'm not happy with the end result, but I'm chalking it up to a learning experience.
Oops #1:
I'd originally gone with just the forged copper, but added the bronze after I cut the bolt welded to the tang. Had I just stuck with the copper it would have turned out a lot cleaner in the rear... The two botched phillips screws on the but are 3" in length and secured deep into the epoxy filled handle. The bolt at the end of the rat-tail is snug and wedged inside the antler to the point of not being able to be threaded any tighter due to the side walls of the bone. I peened a copper pin in place of the intended through bolt/nut as a fix.
Oops#2: I used spiderwire to fill the gaps between the antler / hilt & pommel. I need to find a better means of a cleaner filled gap...
Oops #3: went a lil crazy on jimping past my bed time... little marring on the left side of the blade...
I know its ridiculously large... this was my intent.

These mistakes wont continue onto my next project as I have a new found respect for sticking to the plan.
Please don't be shy, the only way one gets better is through knowing failure... Thank you for your advice, comments, critique, and compliments in advance... This was a fun endeavor to say the least...
Last edited: