Alright,
a few weeks ago I visited the Kelgin Co-Op in PF, TN. Steven Ball helped me do a railroad spike knife and learned quite a bit, now that I'm home using my own forge (forced air venturi) I'm having a few troubles with getting the hammering down. I'm using a 3 lb. shop hammer, and a welding pick hammer (to dimple and then use the larger hammer to push the metal outwards..) As you can see, not good at symmetry yet, nor can I make the metal go where I want it to.
Comments, etc. greatly welcome...also, the tip/edge is too thin on this piece and won't last during the HT so it's a trash piece..
Thanks,
Christopher A. Ford
a few weeks ago I visited the Kelgin Co-Op in PF, TN. Steven Ball helped me do a railroad spike knife and learned quite a bit, now that I'm home using my own forge (forced air venturi) I'm having a few troubles with getting the hammering down. I'm using a 3 lb. shop hammer, and a welding pick hammer (to dimple and then use the larger hammer to push the metal outwards..) As you can see, not good at symmetry yet, nor can I make the metal go where I want it to.
Comments, etc. greatly welcome...also, the tip/edge is too thin on this piece and won't last during the HT so it's a trash piece..


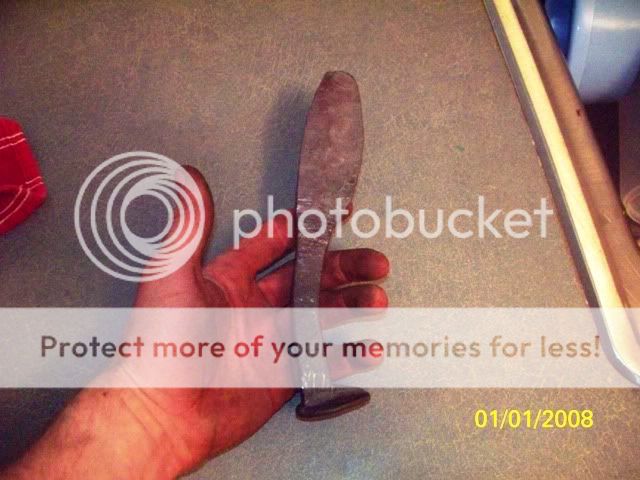


Thanks,
Christopher A. Ford