- Joined
- Nov 25, 2007
- Messages
- 340
my blade measures .079. I purchased a 5/64" 4 fluted end mill which measures .078125 (close I know but I didn't want to go smaller out of fear of breaking). It plunged ok and made it about 3/16" before it broke. Any tips here? Do I need to get the mill up into the collet as far as I can to reduce flex. Also, looking back, I was milling off to the side of the vice ( just remembered I took a photo I will try and post) so maybe the steel flexed or chattered a bit? It seemed like it was going smooth then it just broke. Also, I have no other reason for using O1 other than that's what I had available. Should I not be trying to mill a slot in tool steel?
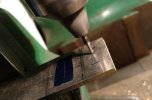
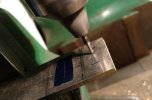