- Joined
- Aug 2, 2010
- Messages
- 1,611
Hey, I just recieved an order I made from Auber Instruments about a week ago for a pyrometer, thermocouple, ceramic covered probe, along with a ceramic sheath for the probe. I had no idea that the probe and ceramic sheath would be as big and long as they are, I expected something about 1/4" in diameter, but this is about 3/8" dia (the ceramic covered probe istself) and the ceramic sheath is 3/4" dia and they are both a foot long
.. Anyway, I took a few pictures of everything I recieved as well as a couple pics of my forge so I could hopefully get some help and advice as to how to install this to my forge and where would be the best place for it to go. I should add that I ordered this mainly for heat treating my blades (1095, 1084, W2, 52100 etc.) and not so much for forging, so I can adjust my burner etc. to get a good HT temp in my forge, not for automatic selenoid controlled forge heating or w/e it's called lol.
So first, here is what I ordered (I chose the ceramic probe with the ceramic sheath option) : http://www.auberins.com/index.php?main_page=product_info&cPath=17&products_id=199
And here is a serperate page on the ceramic probe and wire and ceramic block it came with (I also got the ceramic sheath but that will be self explanitory in the pics I will provide of everything below) : http://www.auberins.com/index.php?main_page=product_info&cPath=20_3&products_id=39
Ok so here are a couple pictures I took of it all together :

And another....

And here are a couple pictures of my forge so I can get some help as to where and how I should attach it...

And another view to get an idea of it's size and length...
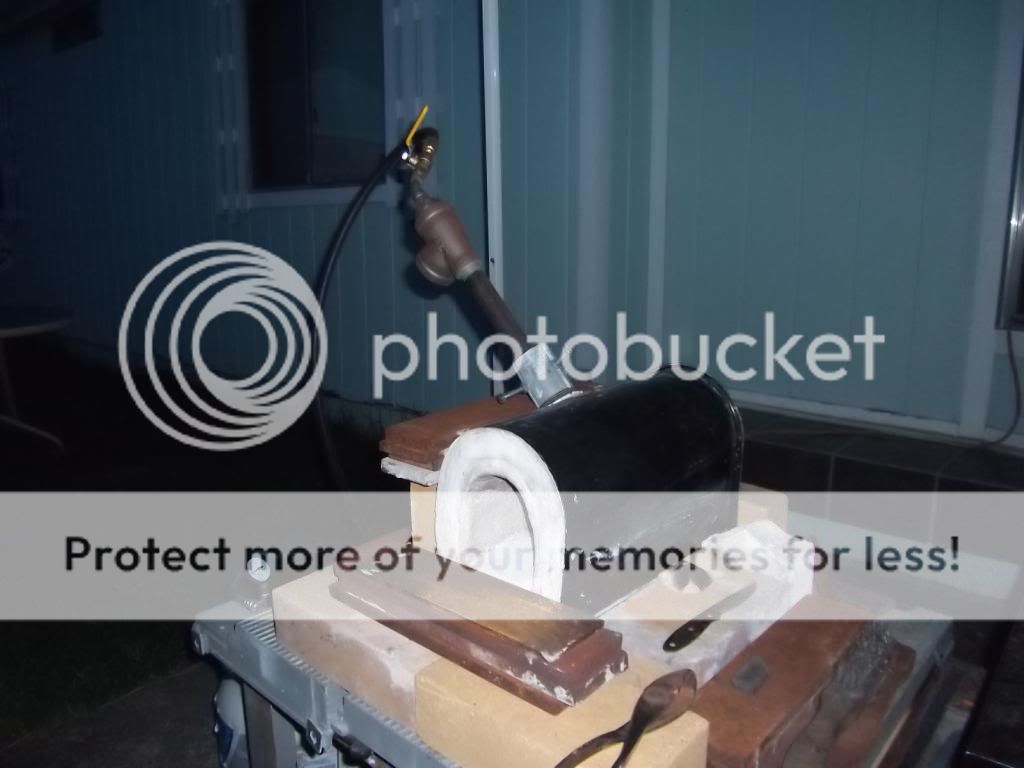
Alright so there ya have it, I really need some help as to how I should go about hooking it up to my forge, like should I drill a big 3/4" hole in the side of my forge to fit the ceramic sheath or should I just lay in it through the small back opening of my forge etc. ? I really appreciate any and all help I can get for this, I wanna hook it up ASAP! But I want to do it right so I don't ruin the thermocouple etc. or ruin my forge by drilling large holes in the sides of it. BTW This was what was recommended to me by the guy I emailed who works there, I told him I was lookin for something I could use in my propane forge for heat treating knives. Thanks!
-Paul

So first, here is what I ordered (I chose the ceramic probe with the ceramic sheath option) : http://www.auberins.com/index.php?main_page=product_info&cPath=17&products_id=199
And here is a serperate page on the ceramic probe and wire and ceramic block it came with (I also got the ceramic sheath but that will be self explanitory in the pics I will provide of everything below) : http://www.auberins.com/index.php?main_page=product_info&cPath=20_3&products_id=39
Ok so here are a couple pictures I took of it all together :

And another....

And here are a couple pictures of my forge so I can get some help as to where and how I should attach it...

And another view to get an idea of it's size and length...
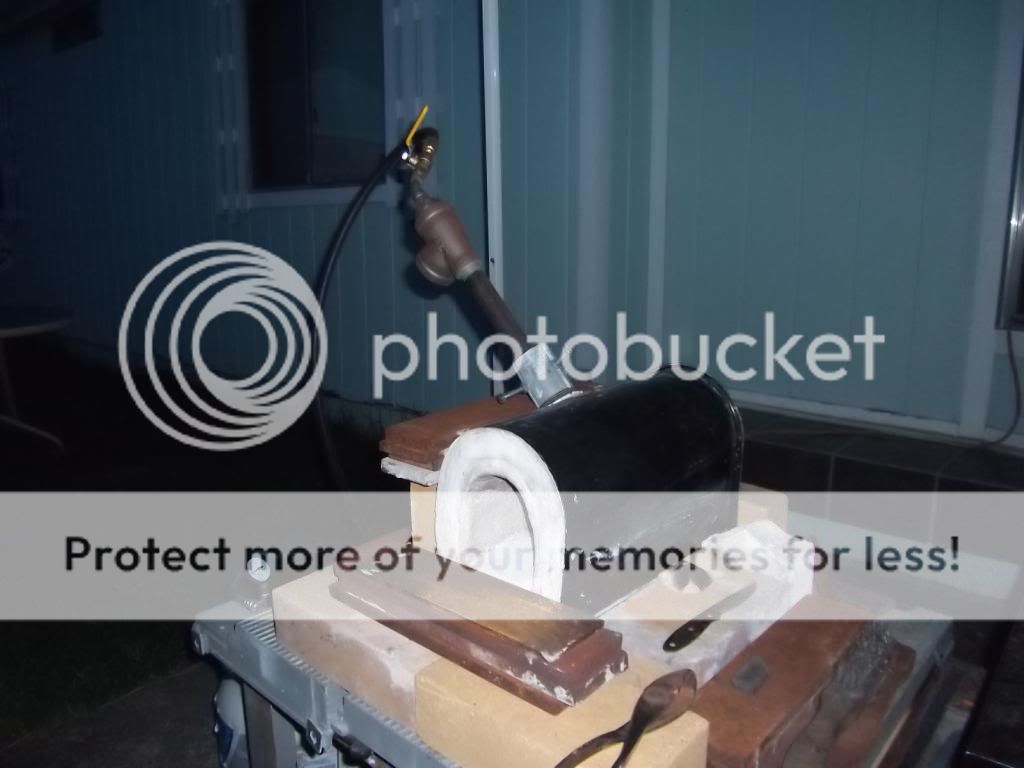
Alright so there ya have it, I really need some help as to how I should go about hooking it up to my forge, like should I drill a big 3/4" hole in the side of my forge to fit the ceramic sheath or should I just lay in it through the small back opening of my forge etc. ? I really appreciate any and all help I can get for this, I wanna hook it up ASAP! But I want to do it right so I don't ruin the thermocouple etc. or ruin my forge by drilling large holes in the sides of it. BTW This was what was recommended to me by the guy I emailed who works there, I told him I was lookin for something I could use in my propane forge for heat treating knives. Thanks!

-Paul
Last edited by a moderator: