So I went to the Bladeshow over the weekend and saw a couple of interesting new attachments. Burr King added a 90 degree rotating base attachment. It looks extremely robust, and it seems to fit the trend of 2x72 grinders that can be used horizontally.
They've also added a surface grinder attachment, and they were showing it flattening a 3-4 foot bar. It can even move side to side with a push of a lever to accommodate bars that are wider then 2 inch. It might give the TW Surface Grinder some competition.
Speaking of which. The Travis Wuertz booth was debuting their super-fan-cooled-rotary-platen-adjustable-grinding-jig thingy. This thing is amazing. It's a rotary platen that has a solid carbide platen behind the rubber belt. The platen gets air cooled with a fan that is rotated by the rubber belt itself. The work rest angle can be adjusted with a knob that sits under it. It comes with a jig that holds the knife at any angle you want for beveling. Through some kind of dark magic, this setup basically eliminates chatter from grinding. That means you can take a fully-hardened unbeveled knife from 60 grit to 9 micron in about 10 minutes. A few minutes on the buffer and you have a mirror finish. I should also note that the TW-90 is one of the quietest grinders I've ever heard.
It can be mounted on the TW-90 (obviously), 1.5" arms (KMG, etc...), the Hardcore Grinder, etc.
And you get all of this for the jaw-dropping, eye watering price of:
(this is the show special, it'll retail for over $3000)
The theory behind it is that it vastly simplifies what is arguably the highest learning curve in knifemaking: grinding clean, precise, repeatable bevels in a timely fashion. The pricing is probably meant to reflect the amount of time saved on grinding and especially hand finishing.
Did anybody else see this at the show, what were your thoughts?

They've also added a surface grinder attachment, and they were showing it flattening a 3-4 foot bar. It can even move side to side with a push of a lever to accommodate bars that are wider then 2 inch. It might give the TW Surface Grinder some competition.
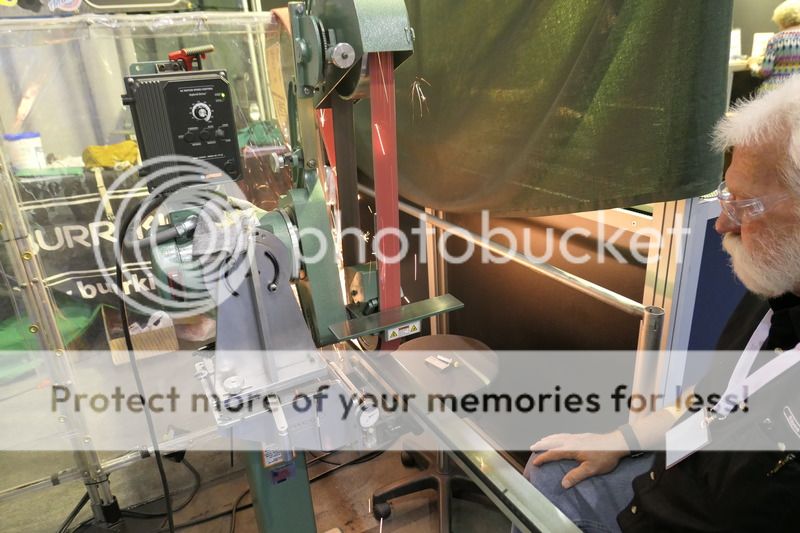
Speaking of which. The Travis Wuertz booth was debuting their super-fan-cooled-rotary-platen-adjustable-grinding-jig thingy. This thing is amazing. It's a rotary platen that has a solid carbide platen behind the rubber belt. The platen gets air cooled with a fan that is rotated by the rubber belt itself. The work rest angle can be adjusted with a knob that sits under it. It comes with a jig that holds the knife at any angle you want for beveling. Through some kind of dark magic, this setup basically eliminates chatter from grinding. That means you can take a fully-hardened unbeveled knife from 60 grit to 9 micron in about 10 minutes. A few minutes on the buffer and you have a mirror finish. I should also note that the TW-90 is one of the quietest grinders I've ever heard.


It can be mounted on the TW-90 (obviously), 1.5" arms (KMG, etc...), the Hardcore Grinder, etc.
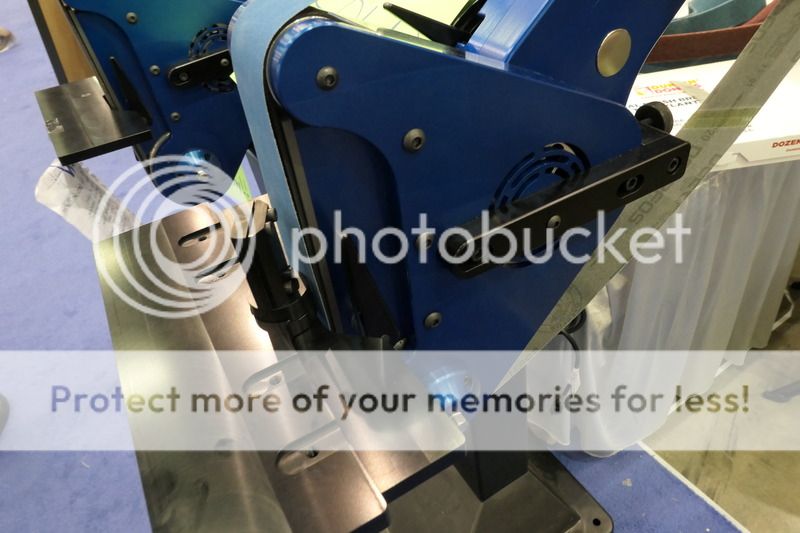
And you get all of this for the jaw-dropping, eye watering price of:
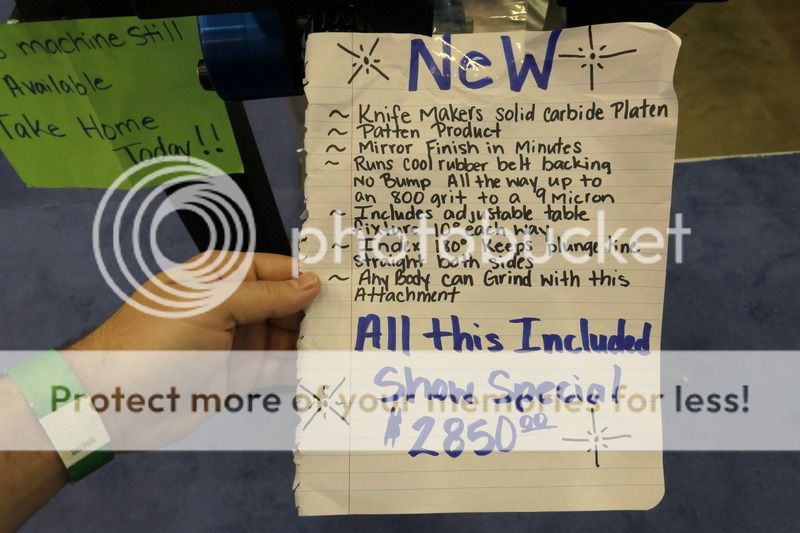
(this is the show special, it'll retail for over $3000)
The theory behind it is that it vastly simplifies what is arguably the highest learning curve in knifemaking: grinding clean, precise, repeatable bevels in a timely fashion. The pricing is probably meant to reflect the amount of time saved on grinding and especially hand finishing.
Did anybody else see this at the show, what were your thoughts?