Hi guys, my name is Jacob and I am a new hobbyist knife maker. I have made a few knives already but haven't really known what I was doing. I guess I just got lucky with the knives I made so far. Here are some pics of past knives.
Two sashimi knives made from W2, differentially hardened.
1095 slicer, differentially hardened.
I recently made a knife but I noticed that the sharp edge doesn't last very long. I was hoping someone could possible help enlighten me on what I am doing wrong. I am using a propane forge.
I am currently working with 1095 steel and I do stock removal.
My basic process is to profile and grind the knife and leave about 1/16 inches on the edge. I then normalize 2-3 times, each time going to barely dull orange non-magnetic (at night time). Then I clean the blade up, clay it with refractory cement and heat it up to slightly past non-magnetic and quench in warm water. I file test, remove some scale then I temper in my oven at about 400F for one hour, two times.
I did this for the above knife and I sharpened it to 4K, stropped it on leather, but found that the nice refined toothy edge goes away almost immediately. The edge is still sharp enough to cut paper but feels very smooth compared to when freshly stropped. Is this a problem with perhaps overheating the blade before quench and bad crystalline structure?
I also just failed a quench and broke the blade to take a look at the cross section. Thought I would post it to see what you guys think and if the grain size is ok or too large.
The transition is there but I somehow feel that the grain size is not what it could be. Is it just that I don't have the equipment to precisely control the HT?
I know I have a lot of questions but I have read other similar topics on this forum and others but I haven't really seen any topics that address this particular problem clearly.
Thanks,
Jake

Two sashimi knives made from W2, differentially hardened.
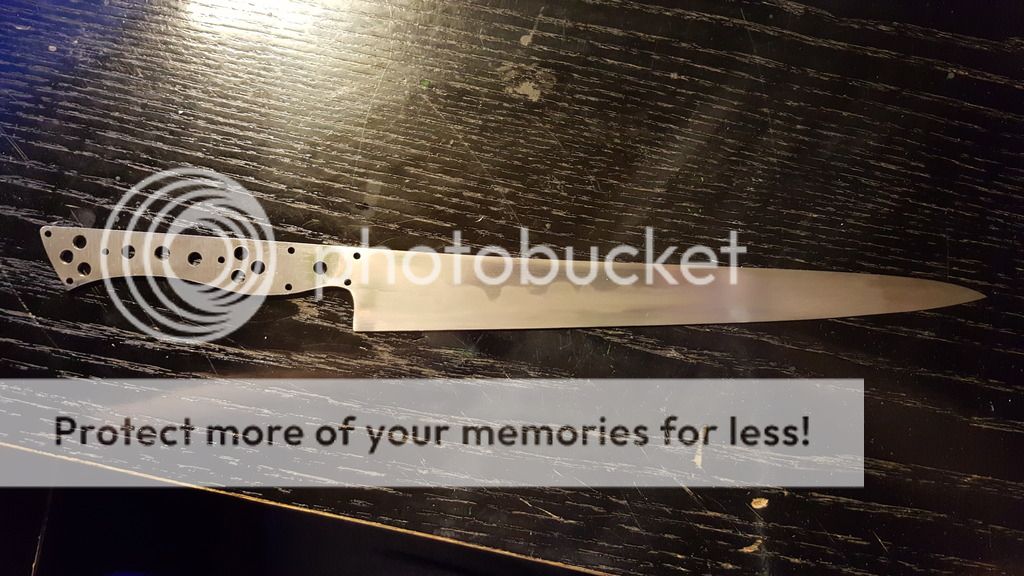

1095 slicer, differentially hardened.
I recently made a knife but I noticed that the sharp edge doesn't last very long. I was hoping someone could possible help enlighten me on what I am doing wrong. I am using a propane forge.
I am currently working with 1095 steel and I do stock removal.
My basic process is to profile and grind the knife and leave about 1/16 inches on the edge. I then normalize 2-3 times, each time going to barely dull orange non-magnetic (at night time). Then I clean the blade up, clay it with refractory cement and heat it up to slightly past non-magnetic and quench in warm water. I file test, remove some scale then I temper in my oven at about 400F for one hour, two times.

I did this for the above knife and I sharpened it to 4K, stropped it on leather, but found that the nice refined toothy edge goes away almost immediately. The edge is still sharp enough to cut paper but feels very smooth compared to when freshly stropped. Is this a problem with perhaps overheating the blade before quench and bad crystalline structure?
I also just failed a quench and broke the blade to take a look at the cross section. Thought I would post it to see what you guys think and if the grain size is ok or too large.

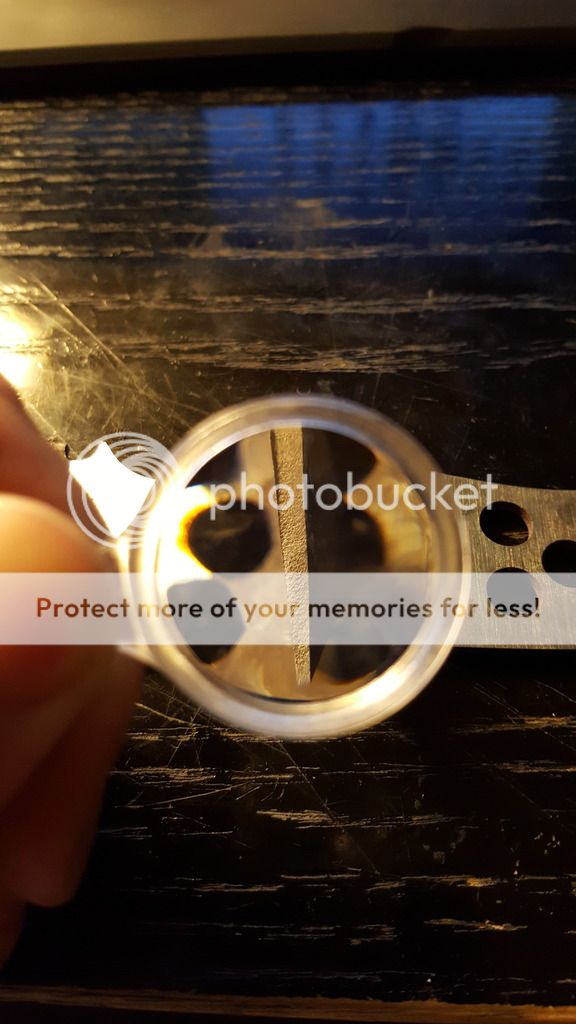
The transition is there but I somehow feel that the grain size is not what it could be. Is it just that I don't have the equipment to precisely control the HT?
I know I have a lot of questions but I have read other similar topics on this forum and others but I haven't really seen any topics that address this particular problem clearly.
Thanks,
Jake