Dear all,
I am studding burners for a few days now, and I'm having no success with my burner building. I'm facing some troubles and I will be thankful if it will be possible for you to give me some advice. Please find enclosed some picture of my setup: The pipe dimensions are written on them (a bit too small...). The gas I'm using is normal cooking gas (butane?) as I don't have access to propane, which I understand is the popular one in the states.
As you can see, I use a blower; the main problem at the moment is that I can not get a stable burners flame, more a regular cooking flame (that sometimes jump out of the forge opening). There is no "dragons breath" when I ignite the burner, I mean that the flame is just not strong enough. I tried everything regarding regulating, fine tuning and so, but just can't get the burner to give a classic blue loud burner flame. Often the flame that I have tuned (after hard work...) shuts off without any reason, and often it is burning in "pulsing", i.e. pulses of regular "kitchens cooking flame" that beats out of the opening. Sometimes I can smell the gas, and I understand that it is not totally burned.
1. Is this butane gas ok or must I switch to propane?
2. Is it possible to combine a venturi system into this blower setup?
3. Shell I drop the blower idea and switch fully to venturi?
I thank you very very much in advance and appreciate your time - Michael.
I am studding burners for a few days now, and I'm having no success with my burner building. I'm facing some troubles and I will be thankful if it will be possible for you to give me some advice. Please find enclosed some picture of my setup: The pipe dimensions are written on them (a bit too small...). The gas I'm using is normal cooking gas (butane?) as I don't have access to propane, which I understand is the popular one in the states.
As you can see, I use a blower; the main problem at the moment is that I can not get a stable burners flame, more a regular cooking flame (that sometimes jump out of the forge opening). There is no "dragons breath" when I ignite the burner, I mean that the flame is just not strong enough. I tried everything regarding regulating, fine tuning and so, but just can't get the burner to give a classic blue loud burner flame. Often the flame that I have tuned (after hard work...) shuts off without any reason, and often it is burning in "pulsing", i.e. pulses of regular "kitchens cooking flame" that beats out of the opening. Sometimes I can smell the gas, and I understand that it is not totally burned.
1. Is this butane gas ok or must I switch to propane?
2. Is it possible to combine a venturi system into this blower setup?
3. Shell I drop the blower idea and switch fully to venturi?
I thank you very very much in advance and appreciate your time - Michael.
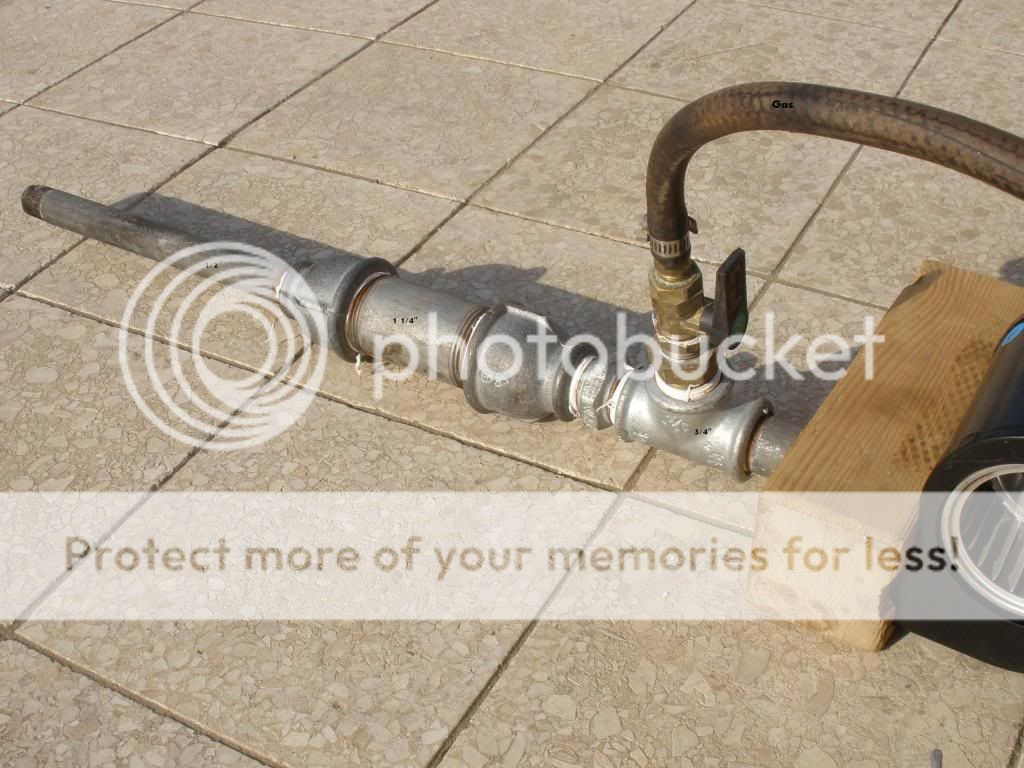

