Joshua Fisher
Knifemaker / Craftsman / Service Provider
- Joined
- Mar 27, 2018
- Messages
- 1,508
As the title suggests I’m thinking of making/modifying some press dies to mimic Japanese power hammer dies. My hope is to be able to use these for the blade forging process to both widen and lengthen a bar but hopefully make keeping cores and cladding even on San mai bars. My big question would be is this even a feasible idea or on a thin blade is the press just going to pull out too much heat for this to work, I’d think having both die surfaces domed would help move thin material but I don’t know if I’m just being too optimistic. Here is a photo of what I’d like to end up with and some available dies that I could modify. 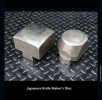
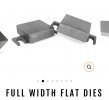
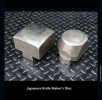
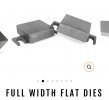