Hi. I have recently took a class on forge welding, as a a project I have forge welded a billet of 1084 with 15N20 jacket. It looks good, I don't see any delams, so I started cutting out a knife shape and at some point, after a basic surface grind I have decided to etch it in ferric chloride to see the contrast. The chloride I'm using is diluted and I only kept my blank in it for a couple of minutes, but the result I got is not really what I expected.
What I expected was for the 15N20 to be white or shiny or anything. But the color of the whole billet is pretty uniform gray, as you can see here:
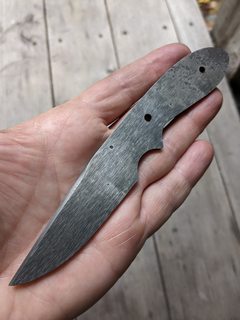
If you look at the edge, there is a slight line that shows the border between the steels and 1084 is very slightly darker then 15N20, but nowhere near the contrast I would expect.

Of course, the knife is still not hardened, I need to polish it a lot more and keep it in the ferric chloride for longer. But my questions are:
1) Would that be enough? Or should I do something else to bring out the contrast?
2) Why is it so uniform? If one of the steels were a mild steel I would chalk it up to carbon migration, but they are both high carbon steels.
Any help would be highly appreciated.
Thank you!
Luka
What I expected was for the 15N20 to be white or shiny or anything. But the color of the whole billet is pretty uniform gray, as you can see here:
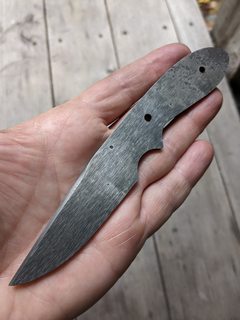
If you look at the edge, there is a slight line that shows the border between the steels and 1084 is very slightly darker then 15N20, but nowhere near the contrast I would expect.

Of course, the knife is still not hardened, I need to polish it a lot more and keep it in the ferric chloride for longer. But my questions are:
1) Would that be enough? Or should I do something else to bring out the contrast?
2) Why is it so uniform? If one of the steels were a mild steel I would chalk it up to carbon migration, but they are both high carbon steels.
Any help would be highly appreciated.
Thank you!
Luka