Hello everyone,
As this is my first proper post on this forum, Id like to make a little introduction. Ive been collecting knives of every sort and description for over 6 years now. At first I bought anything that struck my fancy, but lately Ive been gravitating towards the magical Ti-framelock flipper on bearings (oh, so original, duh ), CF and limited editions and so on. Furthermore Im a steel explorer, always trying to try new and exotic steels. In my pursuit of these qualities I handled, sharpened and used many limited ZTs, BMs and Spydies, one CKF knife, a couple local customs and a manure-load of normal production knives. I had all kinds of steels: M390, CTS-204P, CTS-XHP, CPM S30-110V, CPM M4 and salt bath heat treated M2 (HSS) just to name a couple. I write this not to brag, but to present my background and give some more weight to what Im about to write about the hero of this review the Hills made by Reate.
How the adventure starts packaging, first impressions and so on.
You open the package and your eyes see a simple white box with the name of your knife written by hand with a simple ballpoint. After opening said box your eyes see a high quality zip pouch, more at home with a high dollar midtech, than a basic sub 200$ production knife. Inside that sits your knife in a sealed plastic bag and a smaller one with spare parts. All in all, a nice and satisfying quality package.
IMG_0806
But thats not the only high quality thing about the knife. When you finally get it in your hands you immediately start looking it over, checking it for uneven grinds or edge, mismatched handles, some fitting issues or at least sluggish action, but there is a problem everything is just perfect! One may argue about the design, chosen blade finish etc. but every single area: blade and handle finish, grind, edge, lock geometry, overall action have been executed flawlessly.
Design and features dirty ol specs and little hidden secrets [emoji6]
After the manufacturer:
Length:8.3 Blade length:3.5 Closed length:4.7 Blade thickness:0.157Blade material:S35VN Blade material hardness:59HRCHandle material:6AL4V Clip material:6AL4V
Locking mechanism : Ti-Framelock with stainless steel insert integrated with an overtravel stop
Ball bearing washers
So we get a (IMO) perfect sized blade for EDC in a sensibly compact package (a 1:1,36 blade to handle ratio which is a very decent score). The edge occupies as much of the available blade space as possible, no pointless choils, just a sharpening notch, I like that. The blade is a bit stocky, but its more than full flat ground (the grind in the thickest place is still thinner than the stock in the pivot area), and the thickness behind the edge is around 0,02 (would like it thinner but its still very good for a production knife), so the cutting prowess is excellent. The stonewash is something of a mystery to me it is visually very intense, which will hide scratches well, but at the same time very smooth to the touch, so it doesnt cause friction during cutting. So we get the benefits of scratch resistance of a deep stonewash as on a Ritter Grip with the Sebenza-like smoothness that aids effortless cutting, neat.
The steel used is S35VN not exactly the best steel on the market but over the last year or so it has become my favorite user steel grants decent to excellent performance (on which Ill elaborate later) while keeping the cost reasonable and ensuring completely satisfying corrosion resistance. Of course Id prefer M390 or maybe Niolox (a great steel, such a shame it is so underused) but I wouldnt get it at such a price point.
The whole handle is made of 6Al4V titanium, the staple of the current market. I myself like it a lot it offers a certain high quality feel without making the knife horribly heavy (though this is not a lightweight knife). I would love to see a combination of CF+Ti on the hills it would cut the weight by an ounce or more, and, based on the Horizon D, it wouldnt raise the costs much or at all or at least get some pockets milled out on the inside of the handle but that would definitely result in a price increase. The handle is milled perfectly, complete symmetry of both handles (apart from the slight cutout for easier unlocking ofc), spotless finishing on every surface. What doesnt hit you immediately but you notice it after a while is the choice of surface finishes that hide underneath the beadblast some areas are completely smooth, some have straight or curved milling lines, more or less prominent I like that, especially as it is not random, shows that little extra care the manufacturer put into making the knife.
The lock is another current staple the Ti-Framelock with a stainless insert. It is made flawlessly, the lock interface geometry is spot on, so there is no wiggle or play and I dont expect any to show after prolonged use. Moreover, the insert is well hidden, so it doesnt disrupt the overall look. It also has an overtravel stop.
The clip is a basic titanium spring clip. I would love a deeper carry, or best a 3D machined one, but this one hides the knife reasonably well in the pocket and a carved one would jump the price a bit higher. Not much more to say here, so lets move on.
Now lets take a look at the pivot assembly and everything else that affects the action. The blade rides on a set of ceramic ball bearing washers with hardened steel races inserted into the handles to ensure longevity (additionally, they are replaceable and the knife comes with a spare set if you ever wore them down). The blade and the washers are finished very smooth, so the action is great, no grittiness noticed. Furthermore, the detent ball is also ceramic so it doesnt wear down and increase friction over time. It is also slightly smoother to begin with, so the action is really high class. The detent strength is excellent, especially as it doesnt come from the spring putting unnecessary pressure on the ball, but through proper design of the detent ball and hole and the geometry of the pivot-flipper-detent system. The pivot itself is very tightly fit to the pivot hole in the blade, so there wont be any blade play in any plane or direction, yet the finish of the meeting surfaces is done so that there is no noticeable friction there. Last but not least are the peekaboo stop pins. Its my first time seeing such a knife and I think its an ingenious solution you dont obstructions in cutting as with thumb stud stop pins and you dont need to shave away material from around the pivot area to fit with a standard stop pin, so you get a more robust knife. Moreover it enables an even cleaner look to the knife. There is only one problem with it it gets stuffed with pocket lint, so I advise cleaning it every now and then, so that your lock always engages correctly. Despite that I prefer this to any other stop pin design and hope to own more knives with it.
Reprofiling, sharpening and rope cutting test (plus some insight from use at work) a couple of words about the steel
For me, the thing that tells me the most about the steel is how it behaves on my sharpening stones. Of course it wont tell me much about toughness but Im a city dweller so I usually dont concern myself with this parameter. I use a set of diamond plates, mainly from DMT, apart from the lower grits. When I get a new knife I almost always reprofile it as I like my edge angle quite low. It took medium effort to grind the edge down, confirming the declared hardness it felt around 60 RC comparing to other knives Ive sharpened. It also felt slightly slippery on the stones which I noticed happens with higher carbide steels. While sharpening I noticed a couple things the burr appeared readily and was easy to remove without any chipping and the achievable edge is very fine yet still retains quite a bit of bite while razor sharp this shows a fine grain and carbide structure. All in all a very nice and useful blend of properties.
Now on to the rope cutting test. As an introduction I have to mention that this rope does visible damage (spots reflecting strong light) to the cutting edge after the first 10 cuts in every steel I tried (M2, CTS-204P, CPM-M4) so it's not your run of the mill natural fiber rope. I conducted the test in batches of 50 cuts after which I tested the sharpness by cutting paper a couple dozen times times to garner an average cutting proficiency. I know it's no scientific measure but it served me right and reliably up till now. The results I got are as follows: after the first fifty cuts the sharpness was still viable. It popped an occasional hair off the forearm and cut paper with rare hiccups.
The next fifty got me to a stage where the hiccups were prevalent but still the overall cutting was reasonably smooth. Of course shaving anything was out of the question.
After this stage I didn't notice more dulling, so at 150 and 200 cuts the knife still performed similarly.
Other knives I tried were the CPM-M4 CF Stryker. This was a big surprise as after the first 50 cuts it performed much worse than the Hills after a 100 and still a bit worse than the Reate at 200.
That made me abandon it and get to another knife. Next was a kitchen knife, probably made from Zapp's US2000MC which gave up after 80 cuts. I also tried the 0562CF CTS-204P (carpenters take on M390) ZT. After a 100 cuts it performed about as well as the hills at 50, unfortunately I didn't have enough rope to test it to the full, just did 50 more cuts.
A
So we may assume it holds it's edge about twice as long. This is much, but we have to take into consideration the ZT is quite a bit more expensive and the fit and finish on it is awful in comparison (especially the steel liner). This still makes me want a somewhat budget friendly knife with M390 from Reate, something like a pumped up Hills for about 30-50$ more.
As for normal performance - I used the knife as my only EDC for a month now, also at work where I had to cut up quite a bit of cardboard and remove cling wrap from dirty and dusty pallets which means cutting on sandy wood, hitting nails every now and then and other pleasantries
. Apart from right after the rope test I didn't need to sharpen the knife. Of course the edge got flattened in spots where it must have hit a grain of sand or something, but overall the knife retains it's edge really well. I didn't get to test corrosion resistance as I babied the knife a bit ^^, but I wouldn't expect any surprises from my experience with S35VN.
The Hills as a day to day companion - ergos and so on.
We already know the knife has great theoretical characteristics but do they perform as expected in real life?
Let's start from the bottom - the clip. Plain old stamped titanium clip, mounted reasonably high so the knife hides quite well in the pocket leaving just enough to grab it outside.
It's bent so that it's fairly easy to put back into the pocket but it could use a bit bigger bend at the tip to make it easier with thicker pants. Tension is well balanced. The great thing about it is that you don't feel it at all even during heavy cutting. I've never handled such a comfortable clip.
As we are already talking about handling- the handle. Two 3D-machined titanium slabs, nicely chamfered on the inside edges. The handle is lightly profiled - enough to give traction but not so as to cause discomfort in unconventional grips.
The handles are bead blasted, however they are much more resistant to scratches than eg a Sebbie. I have no idea why, but that's how it is. I haven't discovered any hot spots on the handle, it seems perfectly neutral. As I often work in gloves I also have to mention the knifes performance in such circumstances.
The flipper is very easy to actuate and thanks to the cutout, the lock bar is very easy to access even in numb, gloved fingers.
Let's get to the heart of the topic - the blade. Some might argue about it's aesthetics but it is definitely a useful shape. The grind is a more-than-full flat grind, with a consistently thin edge. I guess the steel would handle an even thinner profile, but not everyone would be comfortable using such a razor, fearing to break it. Still, what we get enables easy cutting through any medium, even thick hard stuff like a pumpkin or soft and sticky like mozzarella.
The blade finish is an intense yet smooth stonewash. It hides even deep scratches pretty well, so you can use it worry free. Then there is the questionable hump. Some may love it (like me), some may hate it, but no one can say it is pointless as it offers a great place to put your finger during precise tip work. The tip itself is a happy medium between easy penetration and toughness. The blade also has a sensible traction plan - a bit of jimping on the flipper tab to help with opening or if you wanted to choke up on the knife and some more jimping on the thumb ramp which, despite it's appearance, offers substantial traction, especially during heavy cutting.
So, to sum up - by buying the Reate Hills knife we get amazing quality, very useful design, nice materials and awesome attention to detail. If you're in the market for a sub 200$ knife and like flippers you'll be hard pressed to find a better offering. And that would be all.
Thanks for reading and feel free to ask any questions.
Cheers,
Jerzy
And some random photos of the Hills here and there
As this is my first proper post on this forum, Id like to make a little introduction. Ive been collecting knives of every sort and description for over 6 years now. At first I bought anything that struck my fancy, but lately Ive been gravitating towards the magical Ti-framelock flipper on bearings (oh, so original, duh ), CF and limited editions and so on. Furthermore Im a steel explorer, always trying to try new and exotic steels. In my pursuit of these qualities I handled, sharpened and used many limited ZTs, BMs and Spydies, one CKF knife, a couple local customs and a manure-load of normal production knives. I had all kinds of steels: M390, CTS-204P, CTS-XHP, CPM S30-110V, CPM M4 and salt bath heat treated M2 (HSS) just to name a couple. I write this not to brag, but to present my background and give some more weight to what Im about to write about the hero of this review the Hills made by Reate.
How the adventure starts packaging, first impressions and so on.
You open the package and your eyes see a simple white box with the name of your knife written by hand with a simple ballpoint. After opening said box your eyes see a high quality zip pouch, more at home with a high dollar midtech, than a basic sub 200$ production knife. Inside that sits your knife in a sealed plastic bag and a smaller one with spare parts. All in all, a nice and satisfying quality package.

But thats not the only high quality thing about the knife. When you finally get it in your hands you immediately start looking it over, checking it for uneven grinds or edge, mismatched handles, some fitting issues or at least sluggish action, but there is a problem everything is just perfect! One may argue about the design, chosen blade finish etc. but every single area: blade and handle finish, grind, edge, lock geometry, overall action have been executed flawlessly.
Design and features dirty ol specs and little hidden secrets [emoji6]
After the manufacturer:
Length:8.3 Blade length:3.5 Closed length:4.7 Blade thickness:0.157Blade material:S35VN Blade material hardness:59HRCHandle material:6AL4V Clip material:6AL4V
Locking mechanism : Ti-Framelock with stainless steel insert integrated with an overtravel stop
Ball bearing washers
So we get a (IMO) perfect sized blade for EDC in a sensibly compact package (a 1:1,36 blade to handle ratio which is a very decent score). The edge occupies as much of the available blade space as possible, no pointless choils, just a sharpening notch, I like that. The blade is a bit stocky, but its more than full flat ground (the grind in the thickest place is still thinner than the stock in the pivot area), and the thickness behind the edge is around 0,02 (would like it thinner but its still very good for a production knife), so the cutting prowess is excellent. The stonewash is something of a mystery to me it is visually very intense, which will hide scratches well, but at the same time very smooth to the touch, so it doesnt cause friction during cutting. So we get the benefits of scratch resistance of a deep stonewash as on a Ritter Grip with the Sebenza-like smoothness that aids effortless cutting, neat.
The steel used is S35VN not exactly the best steel on the market but over the last year or so it has become my favorite user steel grants decent to excellent performance (on which Ill elaborate later) while keeping the cost reasonable and ensuring completely satisfying corrosion resistance. Of course Id prefer M390 or maybe Niolox (a great steel, such a shame it is so underused) but I wouldnt get it at such a price point.
The whole handle is made of 6Al4V titanium, the staple of the current market. I myself like it a lot it offers a certain high quality feel without making the knife horribly heavy (though this is not a lightweight knife). I would love to see a combination of CF+Ti on the hills it would cut the weight by an ounce or more, and, based on the Horizon D, it wouldnt raise the costs much or at all or at least get some pockets milled out on the inside of the handle but that would definitely result in a price increase. The handle is milled perfectly, complete symmetry of both handles (apart from the slight cutout for easier unlocking ofc), spotless finishing on every surface. What doesnt hit you immediately but you notice it after a while is the choice of surface finishes that hide underneath the beadblast some areas are completely smooth, some have straight or curved milling lines, more or less prominent I like that, especially as it is not random, shows that little extra care the manufacturer put into making the knife.
The lock is another current staple the Ti-Framelock with a stainless insert. It is made flawlessly, the lock interface geometry is spot on, so there is no wiggle or play and I dont expect any to show after prolonged use. Moreover, the insert is well hidden, so it doesnt disrupt the overall look. It also has an overtravel stop.
The clip is a basic titanium spring clip. I would love a deeper carry, or best a 3D machined one, but this one hides the knife reasonably well in the pocket and a carved one would jump the price a bit higher. Not much more to say here, so lets move on.
Now lets take a look at the pivot assembly and everything else that affects the action. The blade rides on a set of ceramic ball bearing washers with hardened steel races inserted into the handles to ensure longevity (additionally, they are replaceable and the knife comes with a spare set if you ever wore them down). The blade and the washers are finished very smooth, so the action is great, no grittiness noticed. Furthermore, the detent ball is also ceramic so it doesnt wear down and increase friction over time. It is also slightly smoother to begin with, so the action is really high class. The detent strength is excellent, especially as it doesnt come from the spring putting unnecessary pressure on the ball, but through proper design of the detent ball and hole and the geometry of the pivot-flipper-detent system. The pivot itself is very tightly fit to the pivot hole in the blade, so there wont be any blade play in any plane or direction, yet the finish of the meeting surfaces is done so that there is no noticeable friction there. Last but not least are the peekaboo stop pins. Its my first time seeing such a knife and I think its an ingenious solution you dont obstructions in cutting as with thumb stud stop pins and you dont need to shave away material from around the pivot area to fit with a standard stop pin, so you get a more robust knife. Moreover it enables an even cleaner look to the knife. There is only one problem with it it gets stuffed with pocket lint, so I advise cleaning it every now and then, so that your lock always engages correctly. Despite that I prefer this to any other stop pin design and hope to own more knives with it.
Reprofiling, sharpening and rope cutting test (plus some insight from use at work) a couple of words about the steel
For me, the thing that tells me the most about the steel is how it behaves on my sharpening stones. Of course it wont tell me much about toughness but Im a city dweller so I usually dont concern myself with this parameter. I use a set of diamond plates, mainly from DMT, apart from the lower grits. When I get a new knife I almost always reprofile it as I like my edge angle quite low. It took medium effort to grind the edge down, confirming the declared hardness it felt around 60 RC comparing to other knives Ive sharpened. It also felt slightly slippery on the stones which I noticed happens with higher carbide steels. While sharpening I noticed a couple things the burr appeared readily and was easy to remove without any chipping and the achievable edge is very fine yet still retains quite a bit of bite while razor sharp this shows a fine grain and carbide structure. All in all a very nice and useful blend of properties.

Now on to the rope cutting test. As an introduction I have to mention that this rope does visible damage (spots reflecting strong light) to the cutting edge after the first 10 cuts in every steel I tried (M2, CTS-204P, CPM-M4) so it's not your run of the mill natural fiber rope. I conducted the test in batches of 50 cuts after which I tested the sharpness by cutting paper a couple dozen times times to garner an average cutting proficiency. I know it's no scientific measure but it served me right and reliably up till now. The results I got are as follows: after the first fifty cuts the sharpness was still viable. It popped an occasional hair off the forearm and cut paper with rare hiccups.

The next fifty got me to a stage where the hiccups were prevalent but still the overall cutting was reasonably smooth. Of course shaving anything was out of the question.

After this stage I didn't notice more dulling, so at 150 and 200 cuts the knife still performed similarly.


Other knives I tried were the CPM-M4 CF Stryker. This was a big surprise as after the first 50 cuts it performed much worse than the Hills after a 100 and still a bit worse than the Reate at 200.

That made me abandon it and get to another knife. Next was a kitchen knife, probably made from Zapp's US2000MC which gave up after 80 cuts. I also tried the 0562CF CTS-204P (carpenters take on M390) ZT. After a 100 cuts it performed about as well as the hills at 50, unfortunately I didn't have enough rope to test it to the full, just did 50 more cuts.
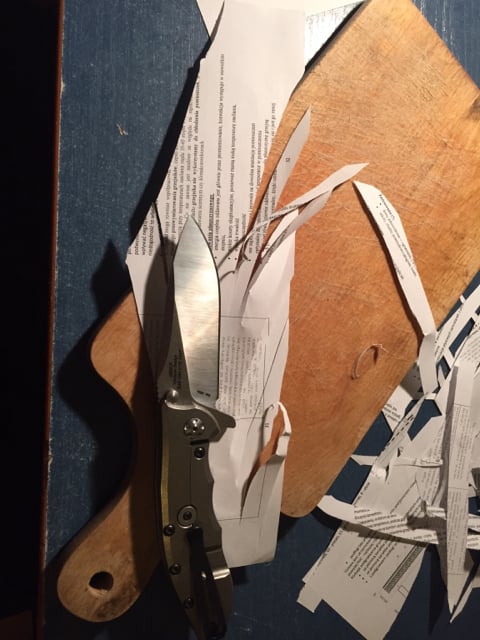
So we may assume it holds it's edge about twice as long. This is much, but we have to take into consideration the ZT is quite a bit more expensive and the fit and finish on it is awful in comparison (especially the steel liner). This still makes me want a somewhat budget friendly knife with M390 from Reate, something like a pumped up Hills for about 30-50$ more.
As for normal performance - I used the knife as my only EDC for a month now, also at work where I had to cut up quite a bit of cardboard and remove cling wrap from dirty and dusty pallets which means cutting on sandy wood, hitting nails every now and then and other pleasantries

The Hills as a day to day companion - ergos and so on.
We already know the knife has great theoretical characteristics but do they perform as expected in real life?
Let's start from the bottom - the clip. Plain old stamped titanium clip, mounted reasonably high so the knife hides quite well in the pocket leaving just enough to grab it outside.

It's bent so that it's fairly easy to put back into the pocket but it could use a bit bigger bend at the tip to make it easier with thicker pants. Tension is well balanced. The great thing about it is that you don't feel it at all even during heavy cutting. I've never handled such a comfortable clip.
As we are already talking about handling- the handle. Two 3D-machined titanium slabs, nicely chamfered on the inside edges. The handle is lightly profiled - enough to give traction but not so as to cause discomfort in unconventional grips.
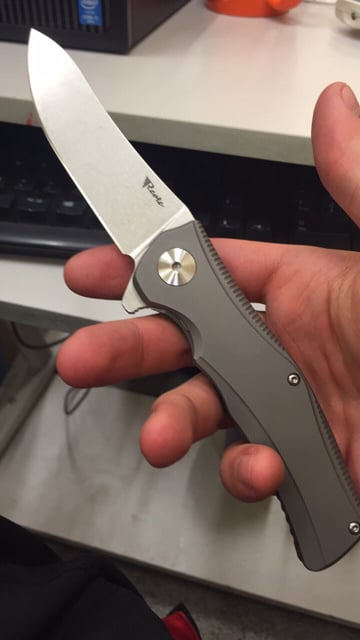
The handles are bead blasted, however they are much more resistant to scratches than eg a Sebbie. I have no idea why, but that's how it is. I haven't discovered any hot spots on the handle, it seems perfectly neutral. As I often work in gloves I also have to mention the knifes performance in such circumstances.

The flipper is very easy to actuate and thanks to the cutout, the lock bar is very easy to access even in numb, gloved fingers.
Let's get to the heart of the topic - the blade. Some might argue about it's aesthetics but it is definitely a useful shape. The grind is a more-than-full flat grind, with a consistently thin edge. I guess the steel would handle an even thinner profile, but not everyone would be comfortable using such a razor, fearing to break it. Still, what we get enables easy cutting through any medium, even thick hard stuff like a pumpkin or soft and sticky like mozzarella.
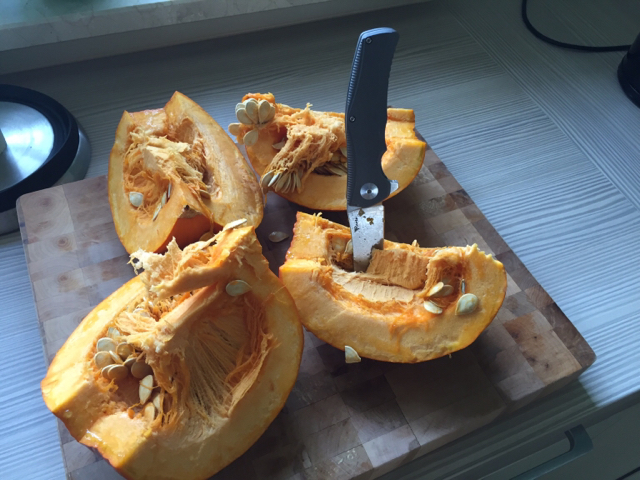
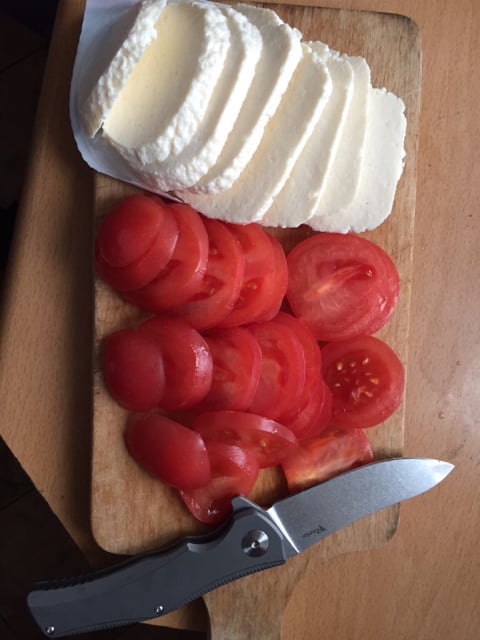
The blade finish is an intense yet smooth stonewash. It hides even deep scratches pretty well, so you can use it worry free. Then there is the questionable hump. Some may love it (like me), some may hate it, but no one can say it is pointless as it offers a great place to put your finger during precise tip work. The tip itself is a happy medium between easy penetration and toughness. The blade also has a sensible traction plan - a bit of jimping on the flipper tab to help with opening or if you wanted to choke up on the knife and some more jimping on the thumb ramp which, despite it's appearance, offers substantial traction, especially during heavy cutting.
So, to sum up - by buying the Reate Hills knife we get amazing quality, very useful design, nice materials and awesome attention to detail. If you're in the market for a sub 200$ knife and like flippers you'll be hard pressed to find a better offering. And that would be all.
Thanks for reading and feel free to ask any questions.
Cheers,
Jerzy
And some random photos of the Hills here and there

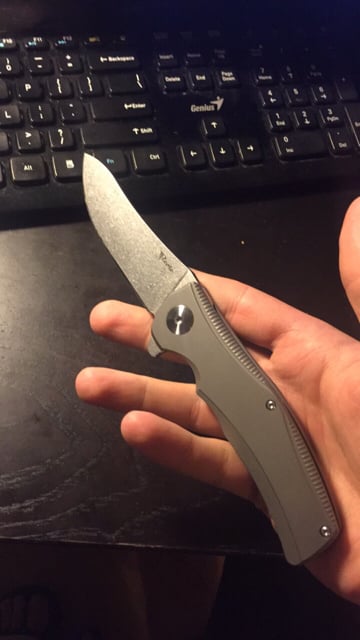
