kuraki
Fimbulvetr Knifeworks
- Joined
- Jun 17, 2016
- Messages
- 4,679
A buddy of mine called me up because he had found this axe head on the side of the road out in the county forest. He wanted to clean it up and hadn't been having much luck with his bench grinder. So I had him come out to my shop to use my equipment. Right away I could tell it had a forge welded edge, but didn't think much of it. So he ground it clean and was asking about buffing it when I had the idea to etch it to show off the edge. I did not expect to find this:
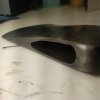
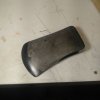
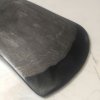
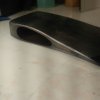
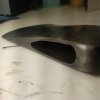