- Joined
- Oct 29, 2006
- Messages
- 2,912
I was asked by a fellow at work to make him a Tanto as a gift for his father. As we work in a woodworking shop, he wanted to do the mounting himself so I did the blade and habaki.
He looked through my books and really wanted the Shinogi-Zukuri style of blade even though it's not usual in a Tanto length blade.
This one is right on the line for length measuring at exactly 1 shaku or 30.3cm or just under 12".
It was a struggle and it sure is a detriment having only videos and books to look at but I learned so much about sword geometry making this one.
The steel is Don Hanson's W2 and was water quenched.
The finish is a hybrid approach with sandpaper and etching. I did however make a version of this handy little tool, a Narume-Dai, for doing the kissaki.
Here's some pics.
He looked through my books and really wanted the Shinogi-Zukuri style of blade even though it's not usual in a Tanto length blade.
This one is right on the line for length measuring at exactly 1 shaku or 30.3cm or just under 12".
It was a struggle and it sure is a detriment having only videos and books to look at but I learned so much about sword geometry making this one.
The steel is Don Hanson's W2 and was water quenched.
The finish is a hybrid approach with sandpaper and etching. I did however make a version of this handy little tool, a Narume-Dai, for doing the kissaki.

Here's some pics.


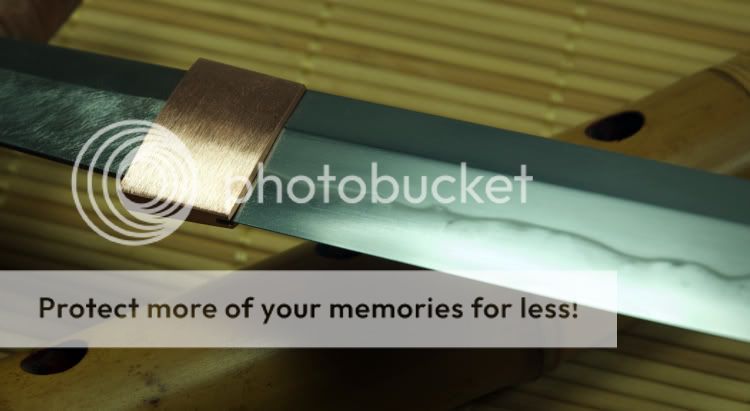


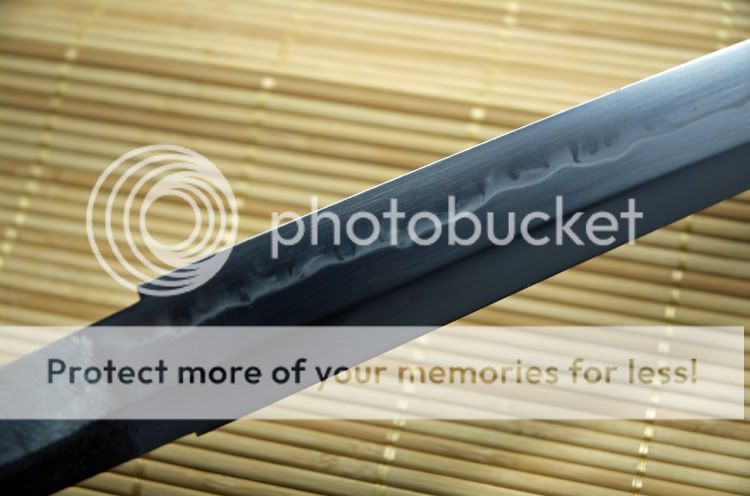
Last edited: