milesofalaska
Knifemaker / Craftsman / Service Provider
- Joined
- Dec 4, 2010
- Messages
- 514
A skinner utility knife with an animal shape. Could be an otter (fish knife).
Blade is tail, not rivet in handle eye. Custom cast fish guard copper and white bronze. In keeping with someone who camps and goes fishing. Chose 1095 steel. How much detail here. I torch harden, only treat the edge, leave back soft. As ai bring up to temp, as I pass into over 900 degree, I mess with the steel on an anvil. Copper brass forged in but only along the back so as not to mess with the integrity of the edge. I hammer with pattern mallet. I try to keep the temperature even so as not to mess with stress and needing to normalize. I keep bringing up to critical past non magnetic (about 100 degrees hotter), Let it cool down a tad, quench in Parks. As it drops down through the 800 degree mark or there-abouts I remove . I want to slow everything down as I come in on 400 degrees.
I put in freezer before temper. I do one temper, 310 degrees (first hint of color shows just to deal with some stress not reduce hardness much) but not much since I did not stress out the entire blade. I do a cryo deep cold treat and another temper, then a 3rd temper. Overkill? I do 2 dozen blades at a time. Well I feel I did stuff to the steel not usually done so am unsure of the effects, extra precautions do no harm and I feel help make up for any indiscretions , errors in my experiments. Over time, field tests show the details of ‘how I do it’ seem to work. Passes flex test, get up to 400 strokes on brass rod tests, and is super hard edge without sacrificing brittle. File does not touch edge, so assume Rockwell over 60. One test is to hammer blade through a brass rod without chipping or dulling.
If anyone has knowledge and wishes to discuss my process I’m interested. Is there a better stage to do the cryo treat, Can hammering on the steel be done at a better temperature? I do not know the rules well. I make blades, test them. I suppose it took 20 years to learn what I could have learned in a year if I listened. The older I get, the less I know. Very little is set in stone. Anyhow…
The red is enamel baked on down in low spots, has not worn off on previous field tests. So much for the steel. Wood is local Alaska birch I cut, dye, stabilize myself. (Cactus juice) . Have this on a wood stand instead of sheath, so it can be displayed when not in use. Could be a kitchen knife for someone who only dreams of a life of fishing. My main customer base seems to be the tourist industry, think they want ‘story knives.’ I can make that happen! Put my story telling abilities to good use. Ha!
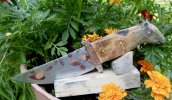
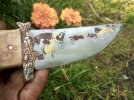
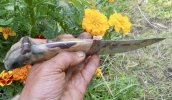
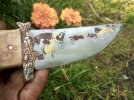
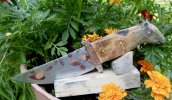
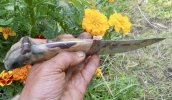
Blade is tail, not rivet in handle eye. Custom cast fish guard copper and white bronze. In keeping with someone who camps and goes fishing. Chose 1095 steel. How much detail here. I torch harden, only treat the edge, leave back soft. As ai bring up to temp, as I pass into over 900 degree, I mess with the steel on an anvil. Copper brass forged in but only along the back so as not to mess with the integrity of the edge. I hammer with pattern mallet. I try to keep the temperature even so as not to mess with stress and needing to normalize. I keep bringing up to critical past non magnetic (about 100 degrees hotter), Let it cool down a tad, quench in Parks. As it drops down through the 800 degree mark or there-abouts I remove . I want to slow everything down as I come in on 400 degrees.
I put in freezer before temper. I do one temper, 310 degrees (first hint of color shows just to deal with some stress not reduce hardness much) but not much since I did not stress out the entire blade. I do a cryo deep cold treat and another temper, then a 3rd temper. Overkill? I do 2 dozen blades at a time. Well I feel I did stuff to the steel not usually done so am unsure of the effects, extra precautions do no harm and I feel help make up for any indiscretions , errors in my experiments. Over time, field tests show the details of ‘how I do it’ seem to work. Passes flex test, get up to 400 strokes on brass rod tests, and is super hard edge without sacrificing brittle. File does not touch edge, so assume Rockwell over 60. One test is to hammer blade through a brass rod without chipping or dulling.
If anyone has knowledge and wishes to discuss my process I’m interested. Is there a better stage to do the cryo treat, Can hammering on the steel be done at a better temperature? I do not know the rules well. I make blades, test them. I suppose it took 20 years to learn what I could have learned in a year if I listened. The older I get, the less I know. Very little is set in stone. Anyhow…
The red is enamel baked on down in low spots, has not worn off on previous field tests. So much for the steel. Wood is local Alaska birch I cut, dye, stabilize myself. (Cactus juice) . Have this on a wood stand instead of sheath, so it can be displayed when not in use. Could be a kitchen knife for someone who only dreams of a life of fishing. My main customer base seems to be the tourist industry, think they want ‘story knives.’ I can make that happen! Put my story telling abilities to good use. Ha!
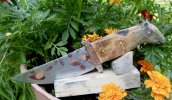
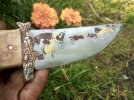
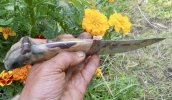
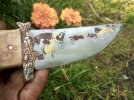
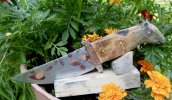
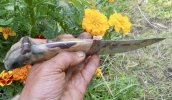