- Joined
- Apr 8, 2020
- Messages
- 2,099
Really small.
So I finally got back into my room and I decided to declare my love of knives for all to see.
Got me some wax and started shaping:
That's probably pretty close to what I'll be using. Usually I work in twos, you know, just in case something happens to the first one. Blue wax is not exactly the best as it's the softest so it's kinda hard to get details in there. I think I need to work the handle a bit.
The thing here is to get everything in the wax, that way you don't have to mess with the metal after it's cast.
I also still need to work the ring.
I work in lost wax silver casting so the little wharnie with be attached to the wax ring, plastered up and then burned out. The plaster mold goes into a centrifuge where silver is injected to mold.
That's my lightning bolt ring for scale. I cast that oh about four years ago.
My knife ring will look the same; it's sized for my middle finger though it'll work on index too.
Hopefully I'll be done by Thursday.
Stay tuned!
I also have another wrap around design in mind.
So I finally got back into my room and I decided to declare my love of knives for all to see.
Got me some wax and started shaping:
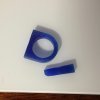
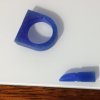
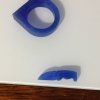
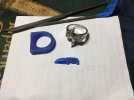
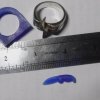
That's probably pretty close to what I'll be using. Usually I work in twos, you know, just in case something happens to the first one. Blue wax is not exactly the best as it's the softest so it's kinda hard to get details in there. I think I need to work the handle a bit.
The thing here is to get everything in the wax, that way you don't have to mess with the metal after it's cast.
I also still need to work the ring.
I work in lost wax silver casting so the little wharnie with be attached to the wax ring, plastered up and then burned out. The plaster mold goes into a centrifuge where silver is injected to mold.
That's my lightning bolt ring for scale. I cast that oh about four years ago.
My knife ring will look the same; it's sized for my middle finger though it'll work on index too.
Hopefully I'll be done by Thursday.
Stay tuned!
I also have another wrap around design in mind.