Mistwalker
Gold Member
- Joined
- Dec 22, 2007
- Messages
- 19,029
The following is a series of images that tell the story of the weekly road to the Friday sales posts in the Fiddleback Forge sub-forum. It is a series of photos that illustrates the effort, level of craftsmanship, and love for the craft that goes into the knives that are handcrafted by Andy Roy and his team at Fiddleback Forge. I hope you enjoy viewing them as much as I enjoyed taking and going through them.
Some things to note here are; the absence of automated machinery, and the attention to detail that is paid, it's a very hands-on process.
As well as the temperature conditions at times. You will notice a space heater in use even while a lot of physical exertion is being expended, and if you look close you will see ice building up on the inside of a face shield. As I said, this is a very dedicated group of individuals who work very hard performing a job they love dearly, into order to produce highly functional works of art.
Since by most accounts a knife is defined as a sharpened piece of steel with a handle, obviously the first step is to shape the steel. This process begins with tracing patterns of blade profiles onto dykem coated steel stock.
Those are then cut into individual pieces, and the knife blanks profiled out on a belt grinder.
Once shaped the the blanks are scribed, and then the holes are drilled for the pins and bullseye.
As you can see, the dykem is also applied the the blade end of the blank on the opposite for the grinding of the primary bevels. The the tangs are tapered and the primary bevels ground. Watching Andy grind the bevels was something to see. The man is very talented.
Next, the shaped blanks go into the oven for heat treatment, then the quench, and afterward allowed to cool.
The heat treated blanks are then scribed for grinding, and then they are cleaned up with the grinds being taken to the next stage.
Some things to note here are; the absence of automated machinery, and the attention to detail that is paid, it's a very hands-on process.
As well as the temperature conditions at times. You will notice a space heater in use even while a lot of physical exertion is being expended, and if you look close you will see ice building up on the inside of a face shield. As I said, this is a very dedicated group of individuals who work very hard performing a job they love dearly, into order to produce highly functional works of art.
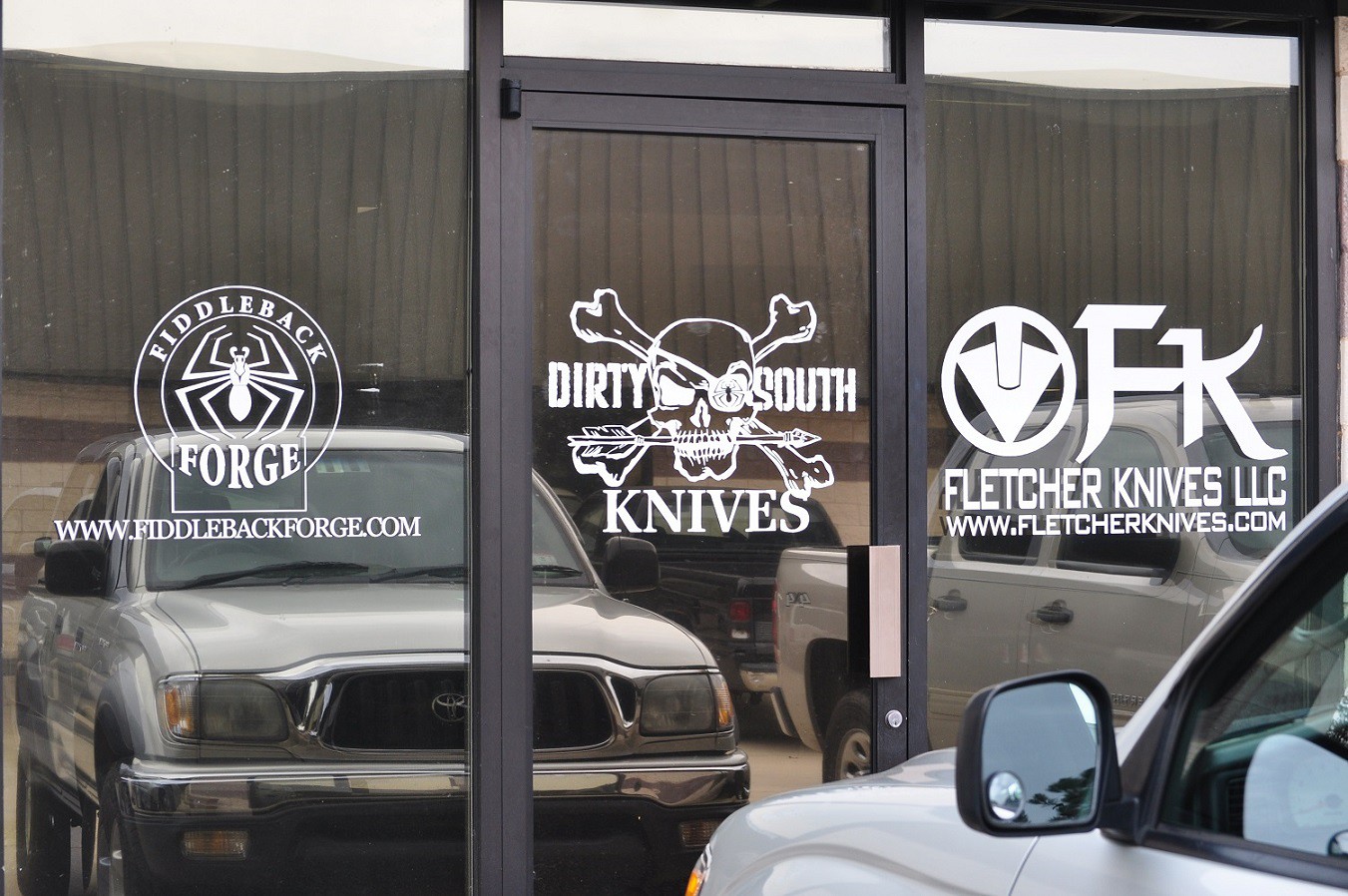
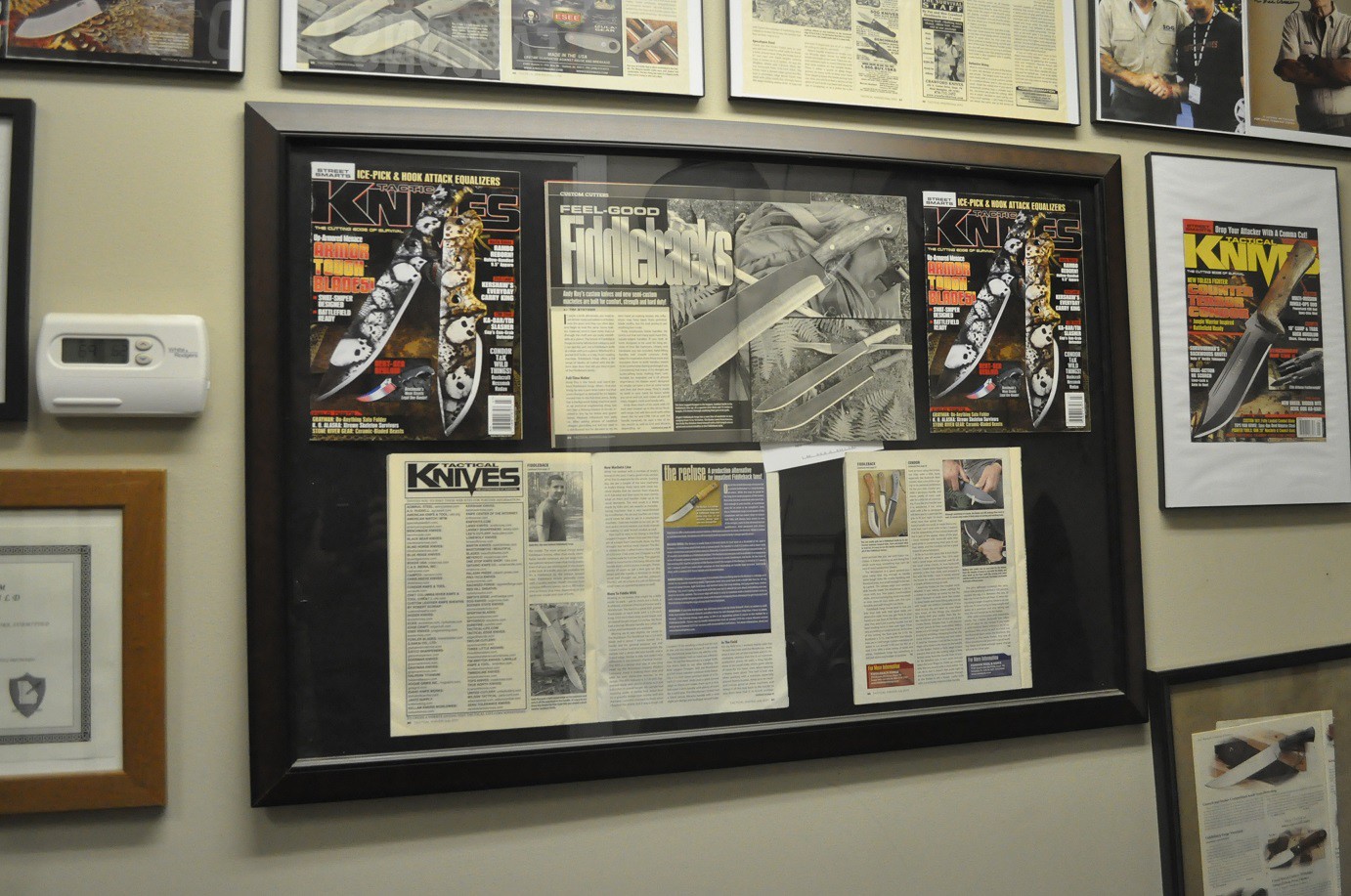
Since by most accounts a knife is defined as a sharpened piece of steel with a handle, obviously the first step is to shape the steel. This process begins with tracing patterns of blade profiles onto dykem coated steel stock.
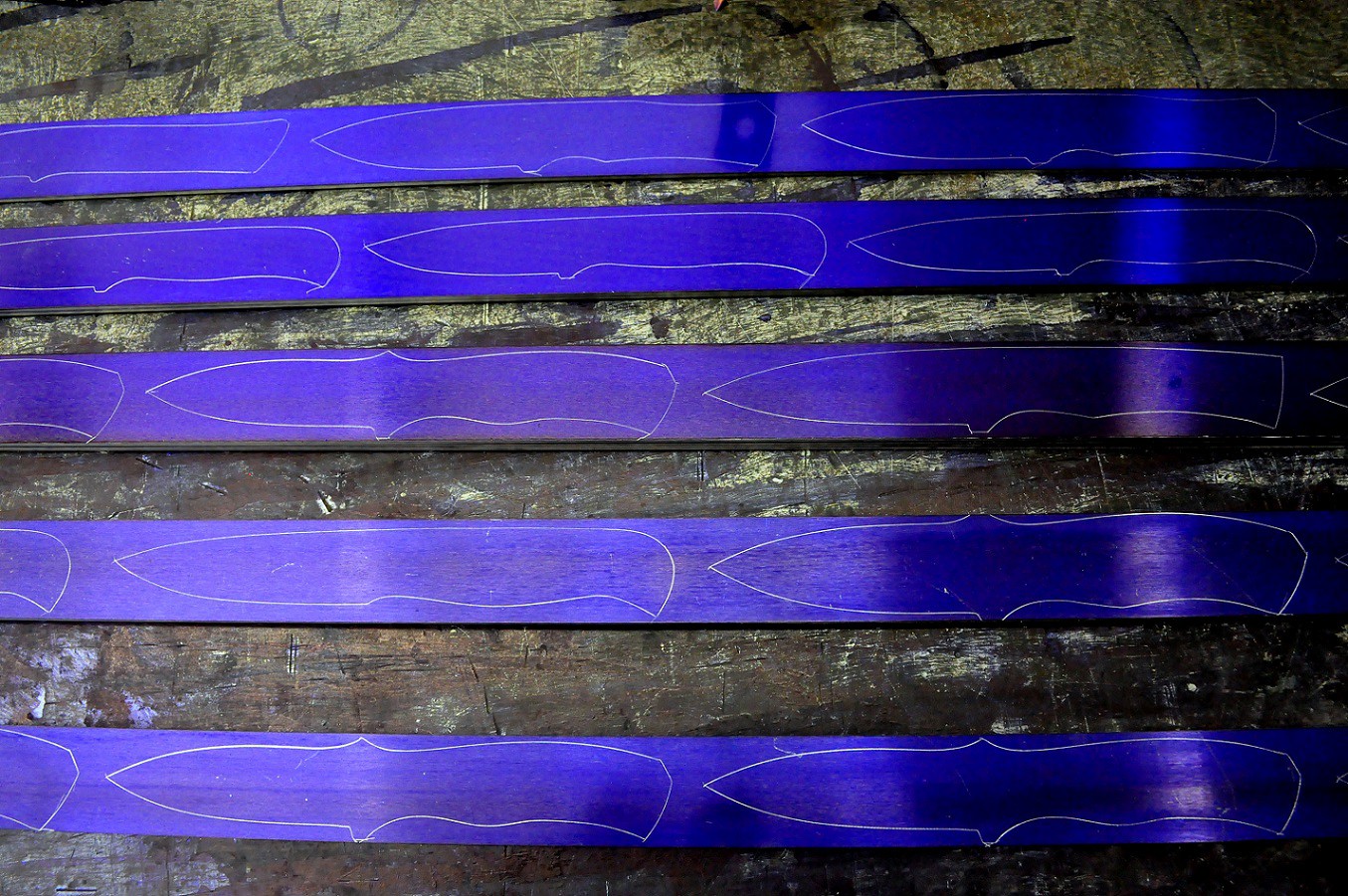
Those are then cut into individual pieces, and the knife blanks profiled out on a belt grinder.
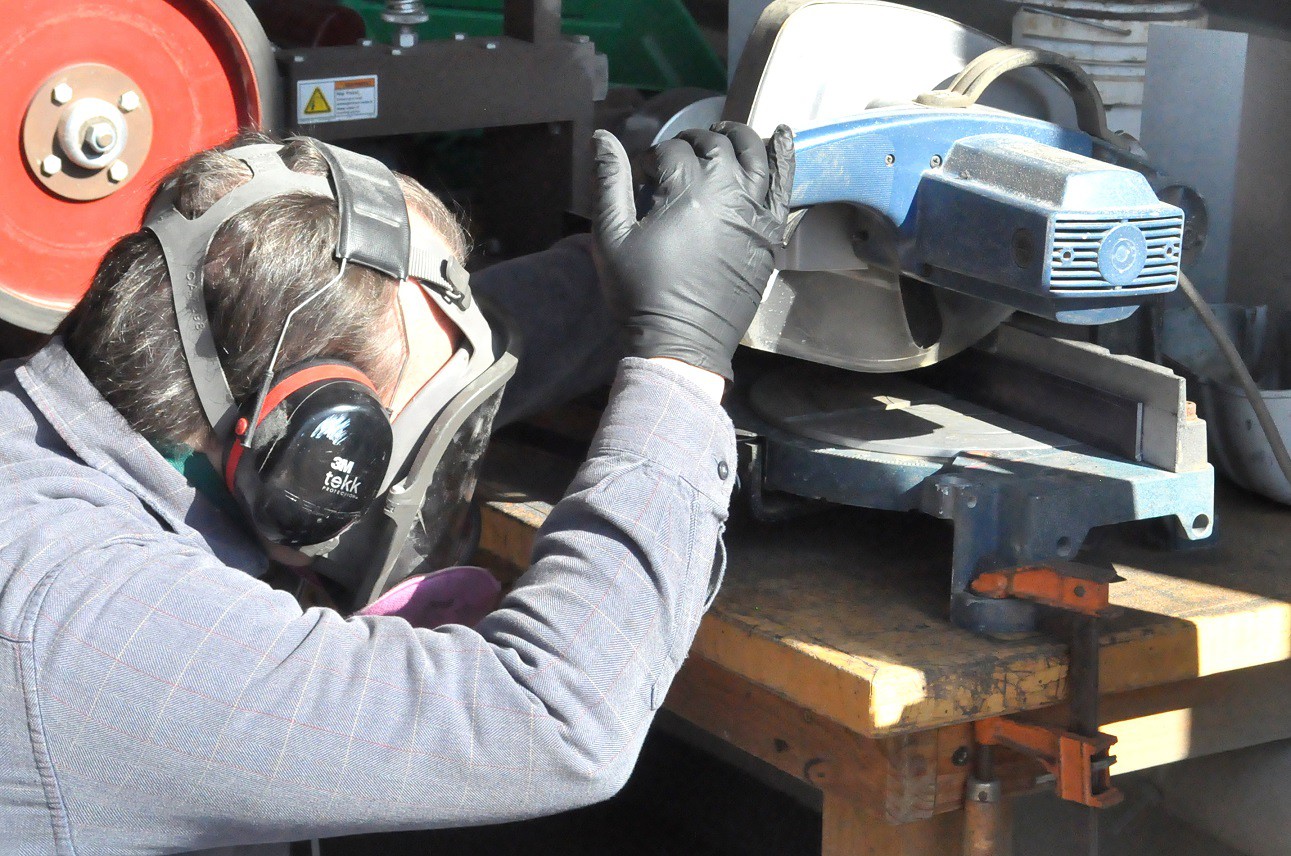
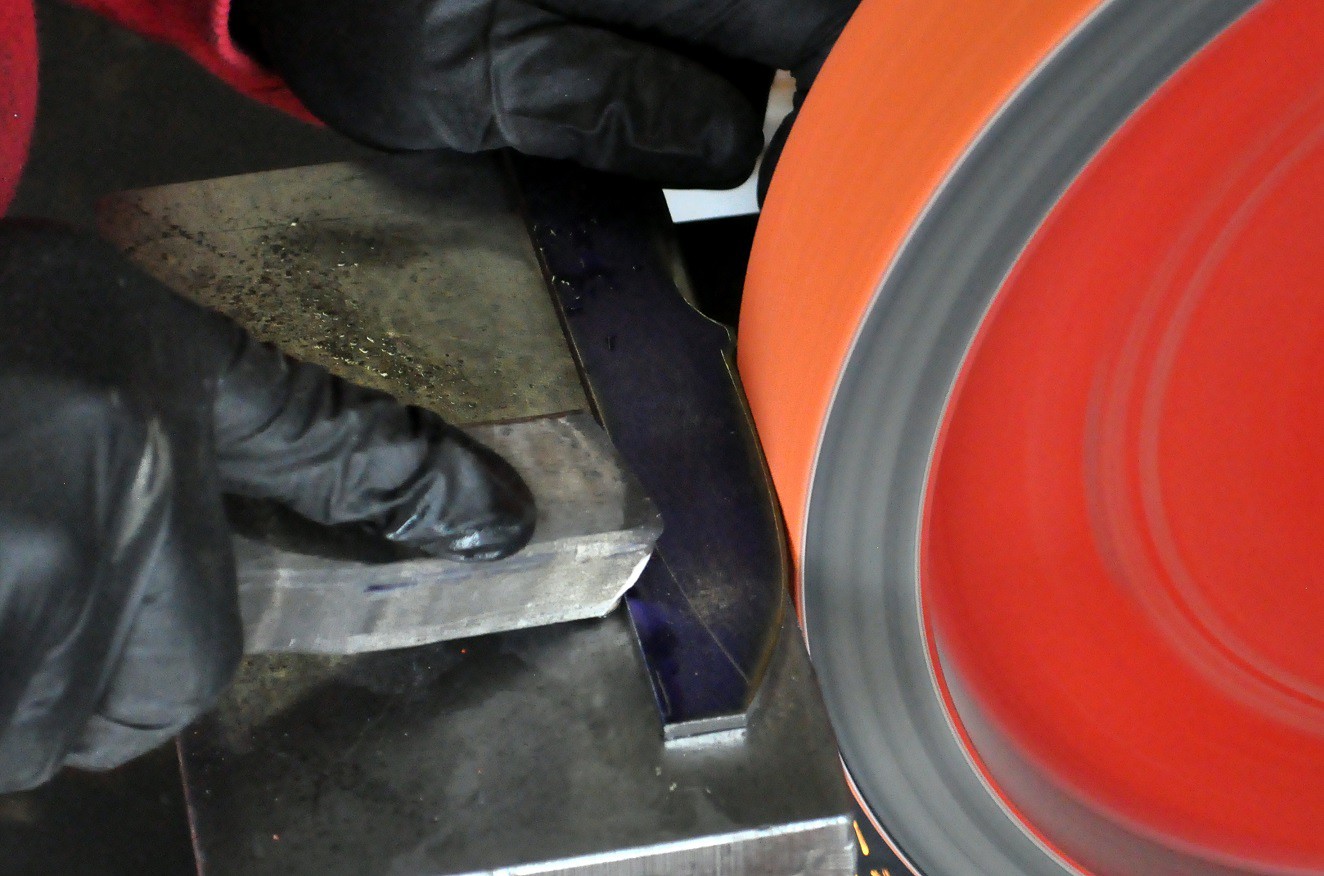
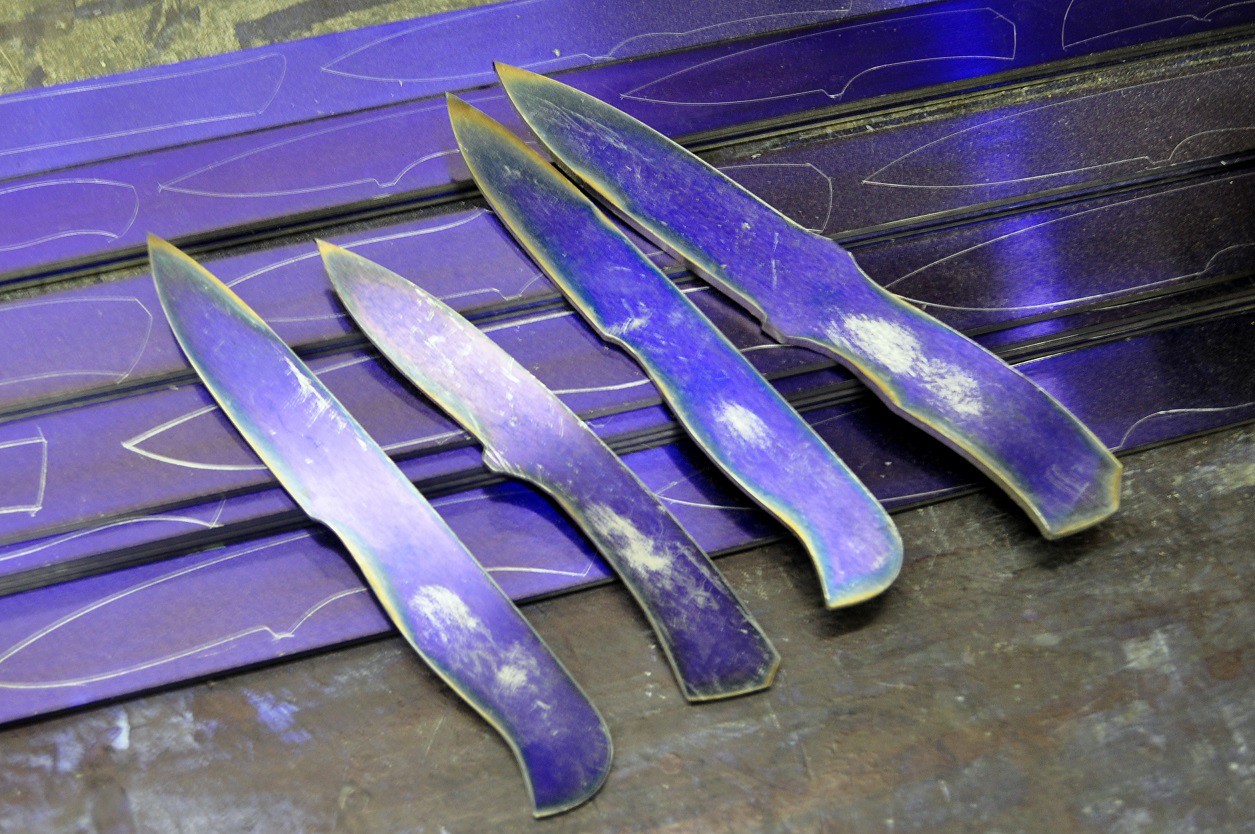
Once shaped the the blanks are scribed, and then the holes are drilled for the pins and bullseye.
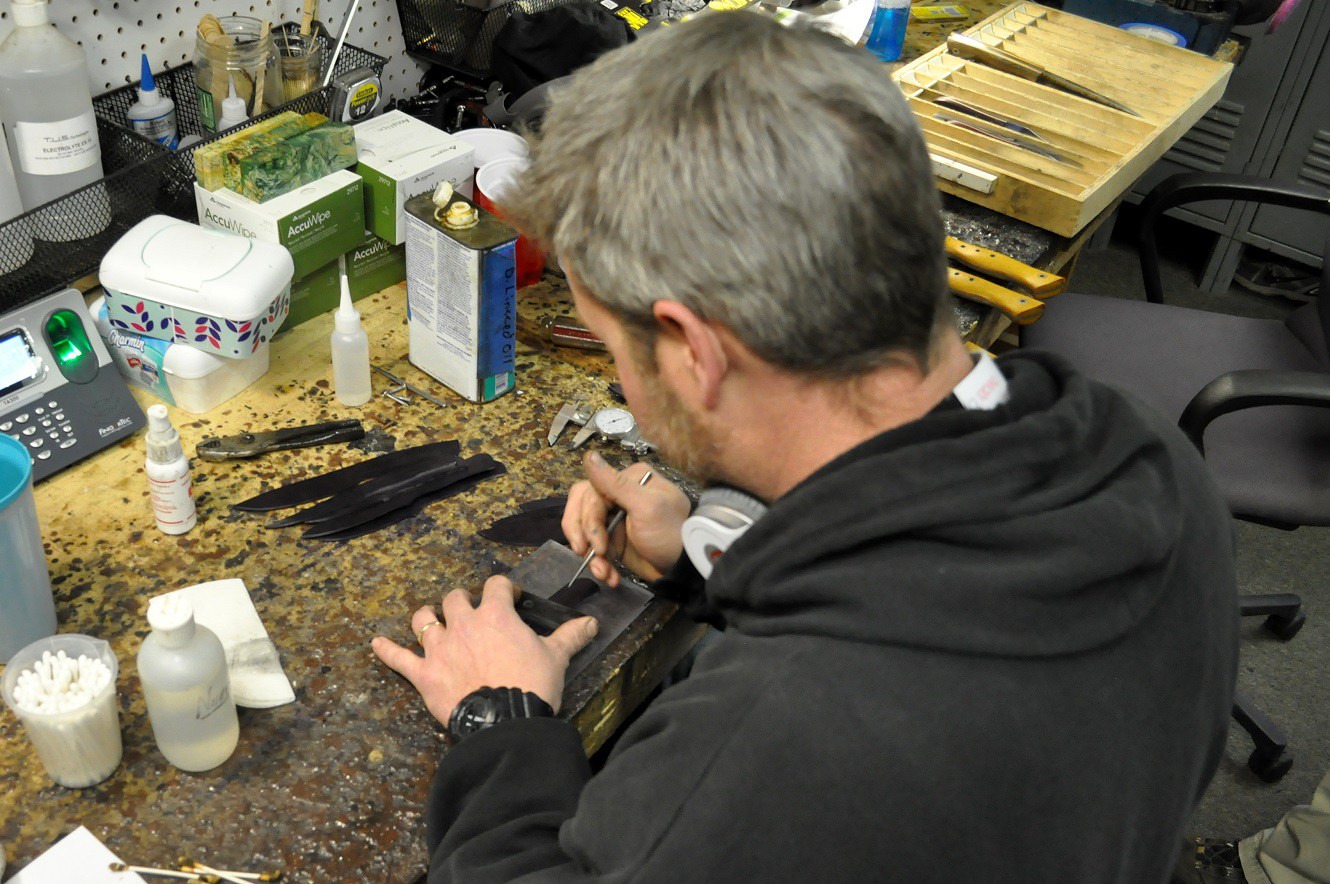
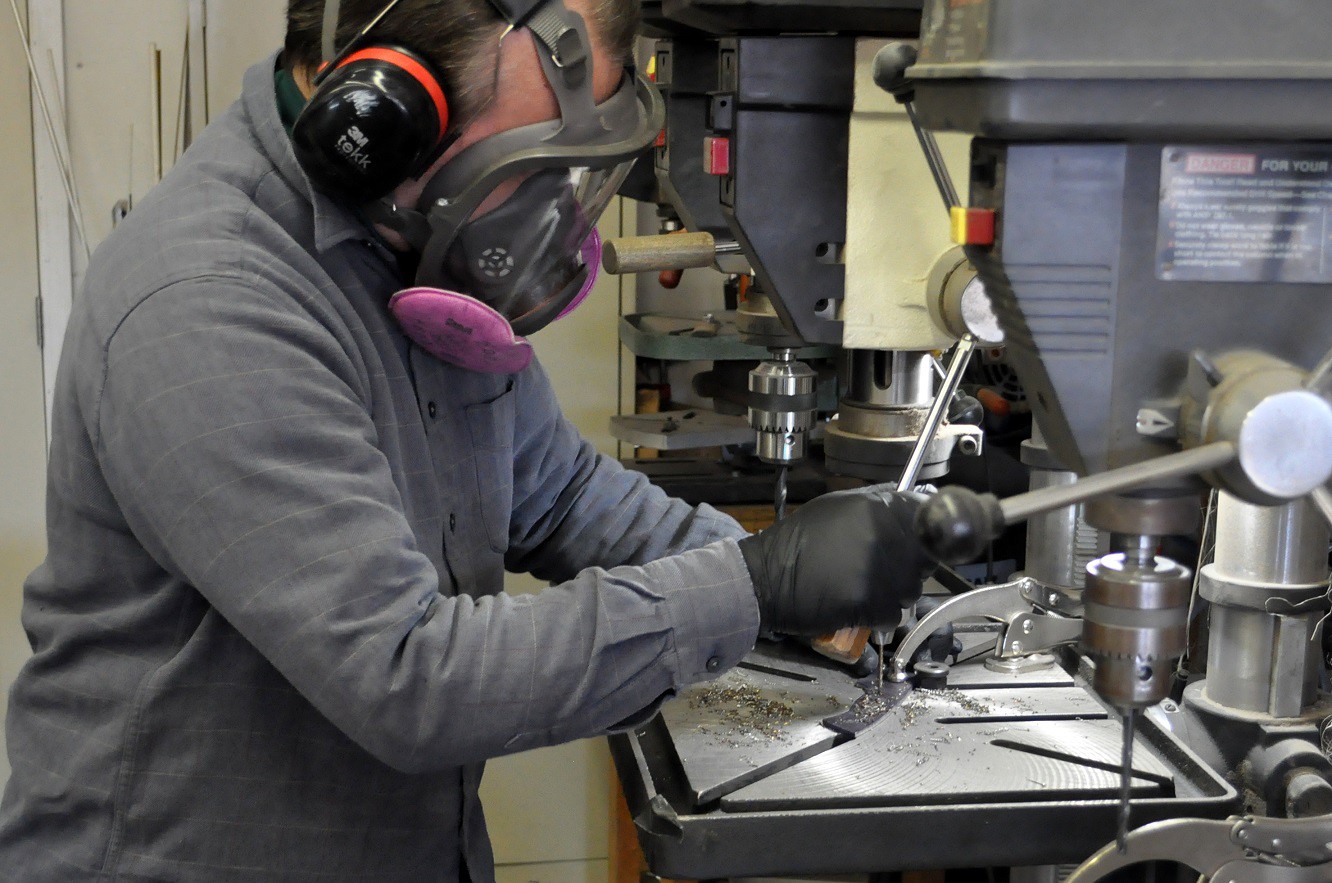
As you can see, the dykem is also applied the the blade end of the blank on the opposite for the grinding of the primary bevels. The the tangs are tapered and the primary bevels ground. Watching Andy grind the bevels was something to see. The man is very talented.
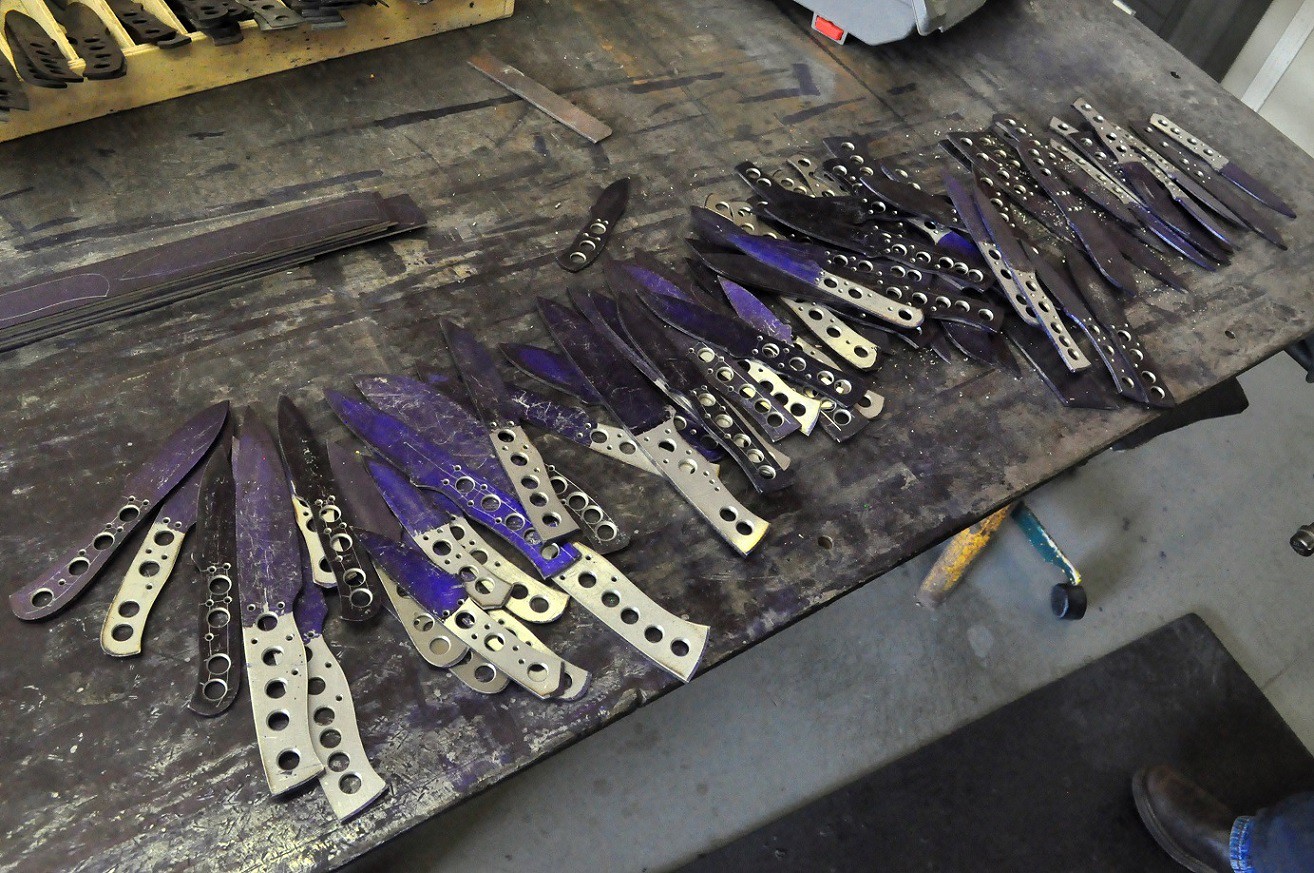
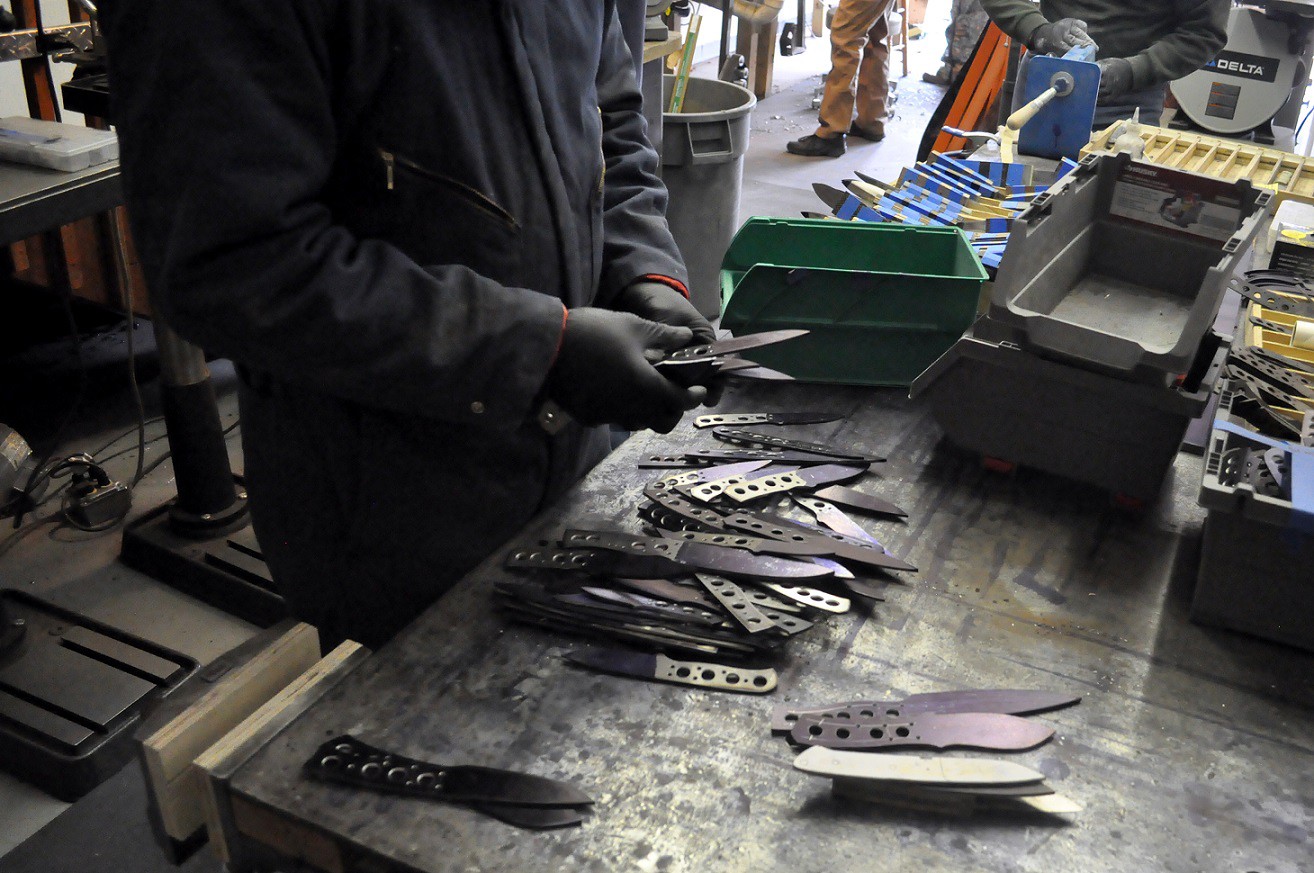
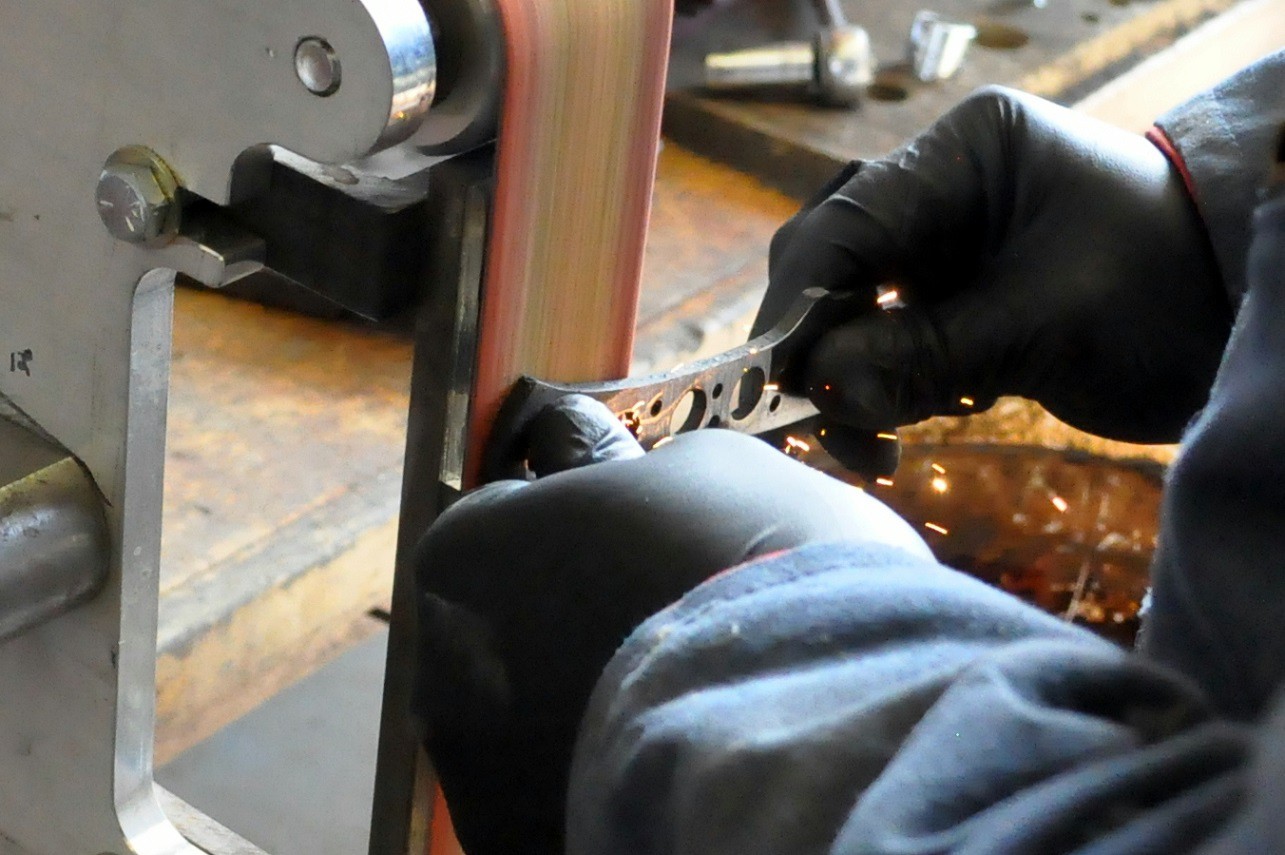
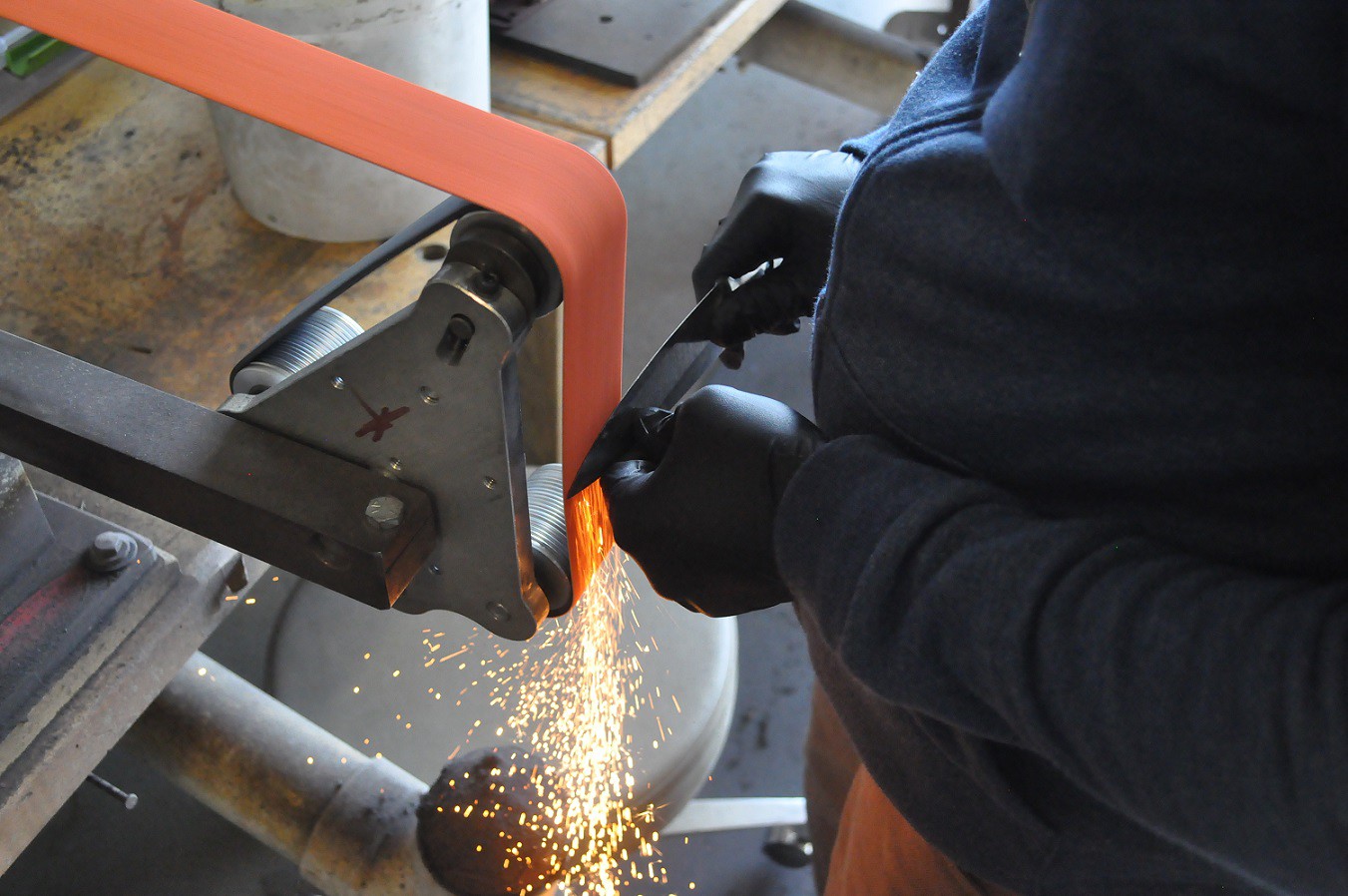
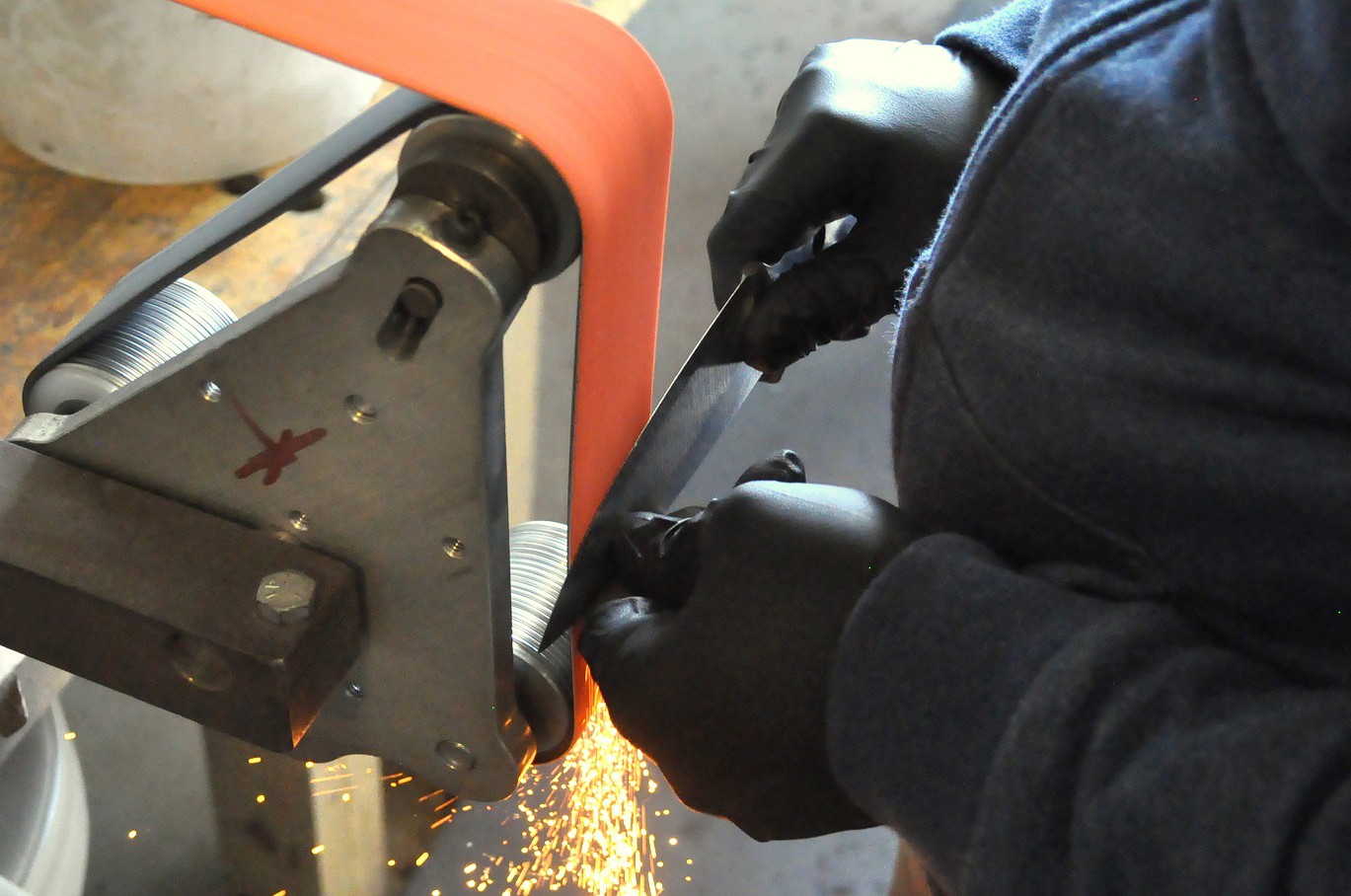
Next, the shaped blanks go into the oven for heat treatment, then the quench, and afterward allowed to cool.
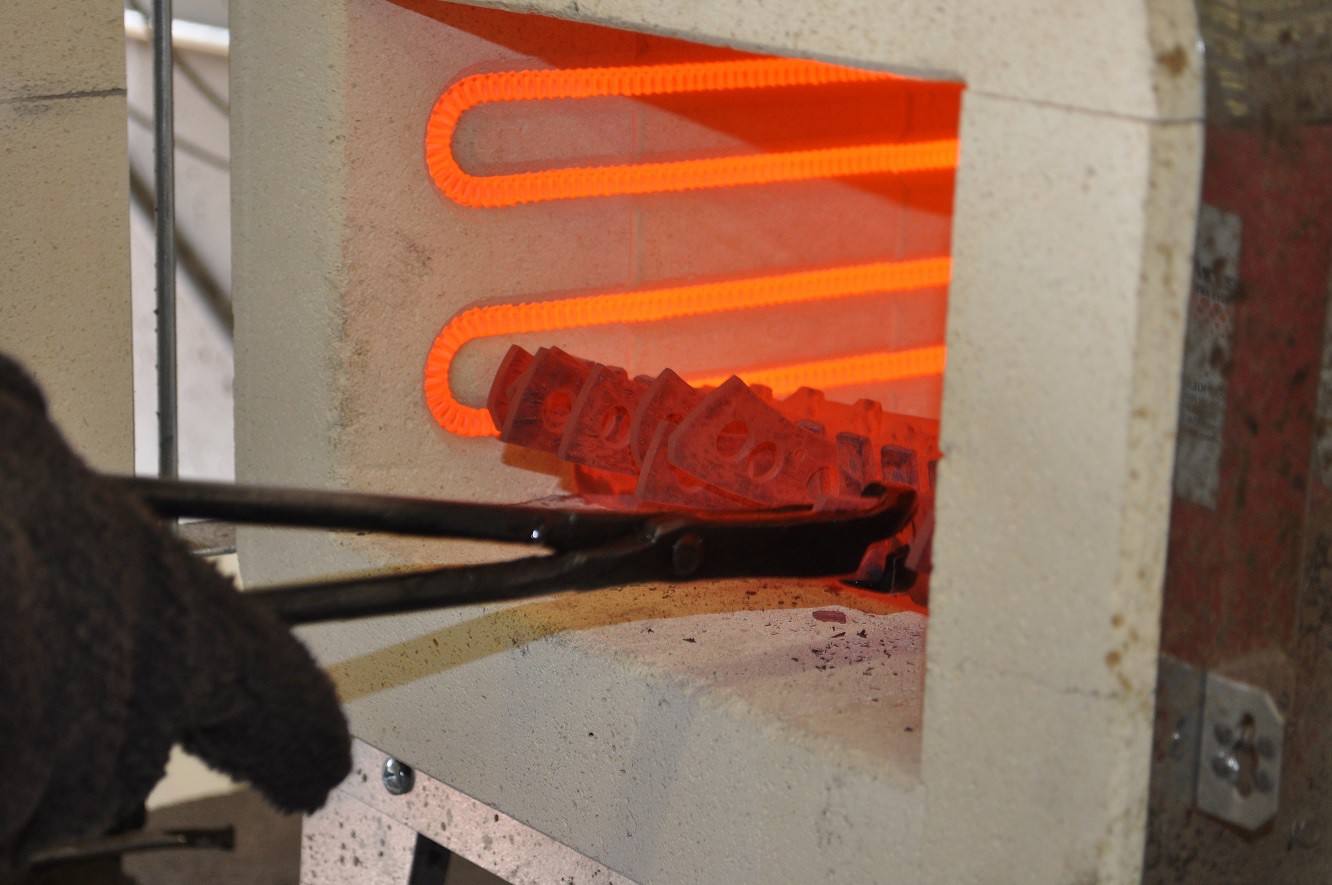
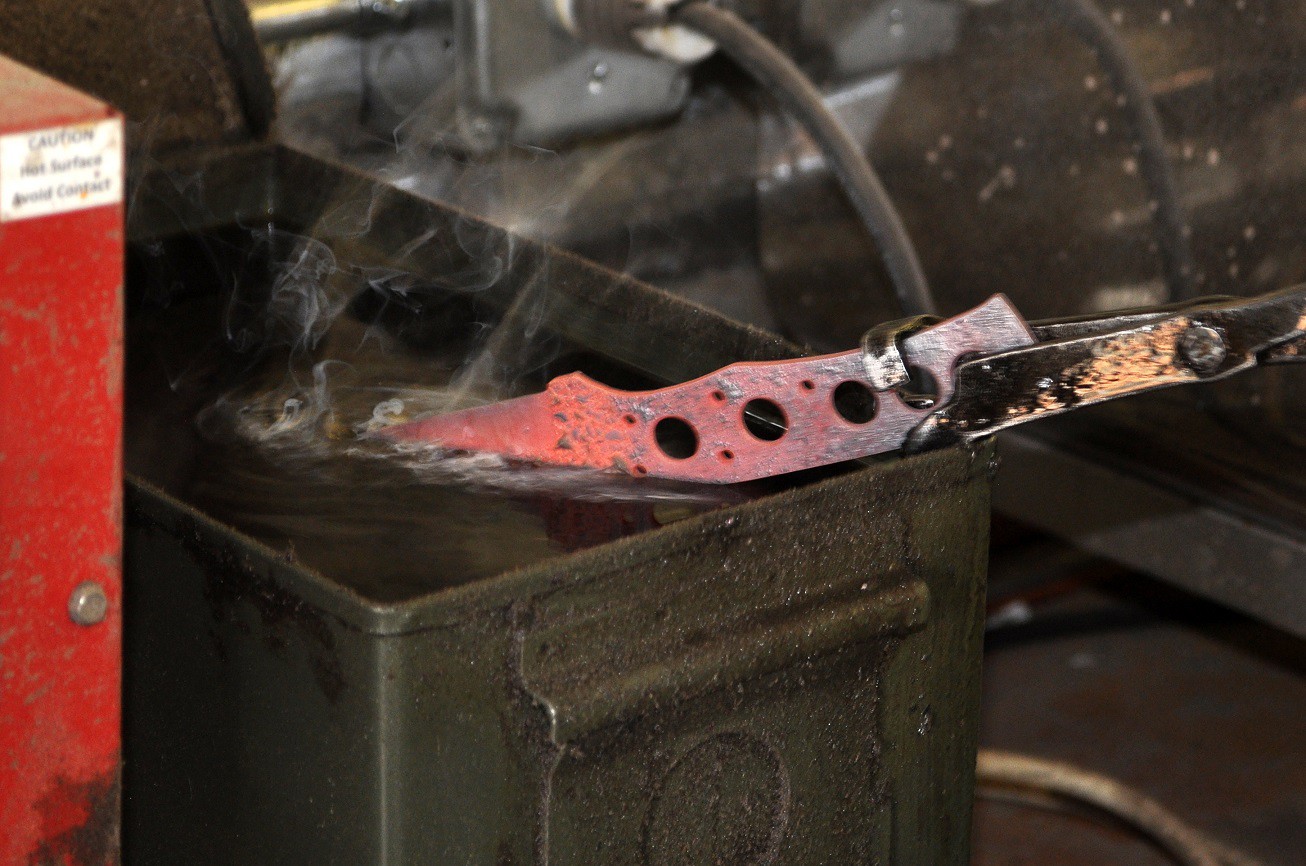
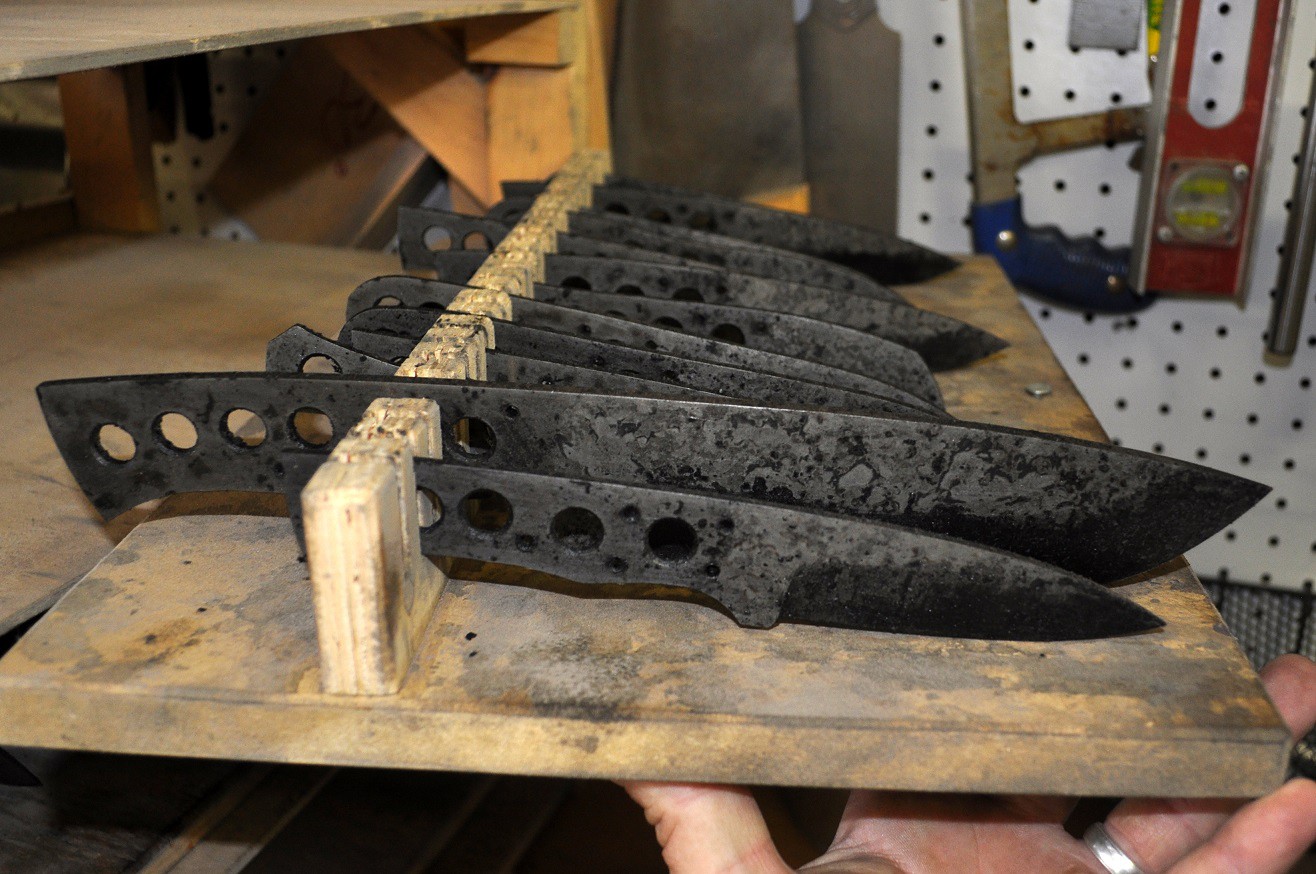
The heat treated blanks are then scribed for grinding, and then they are cleaned up with the grinds being taken to the next stage.
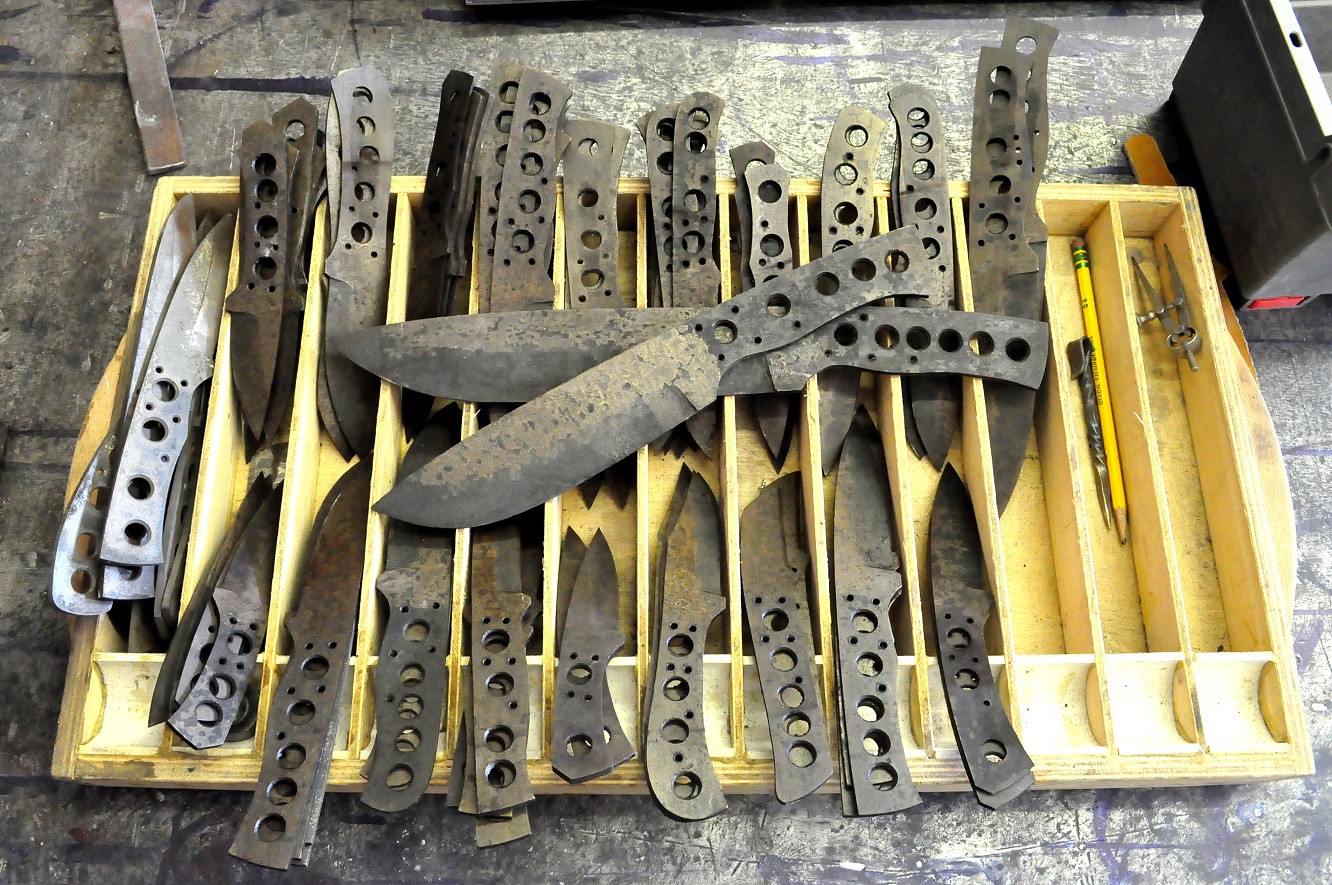
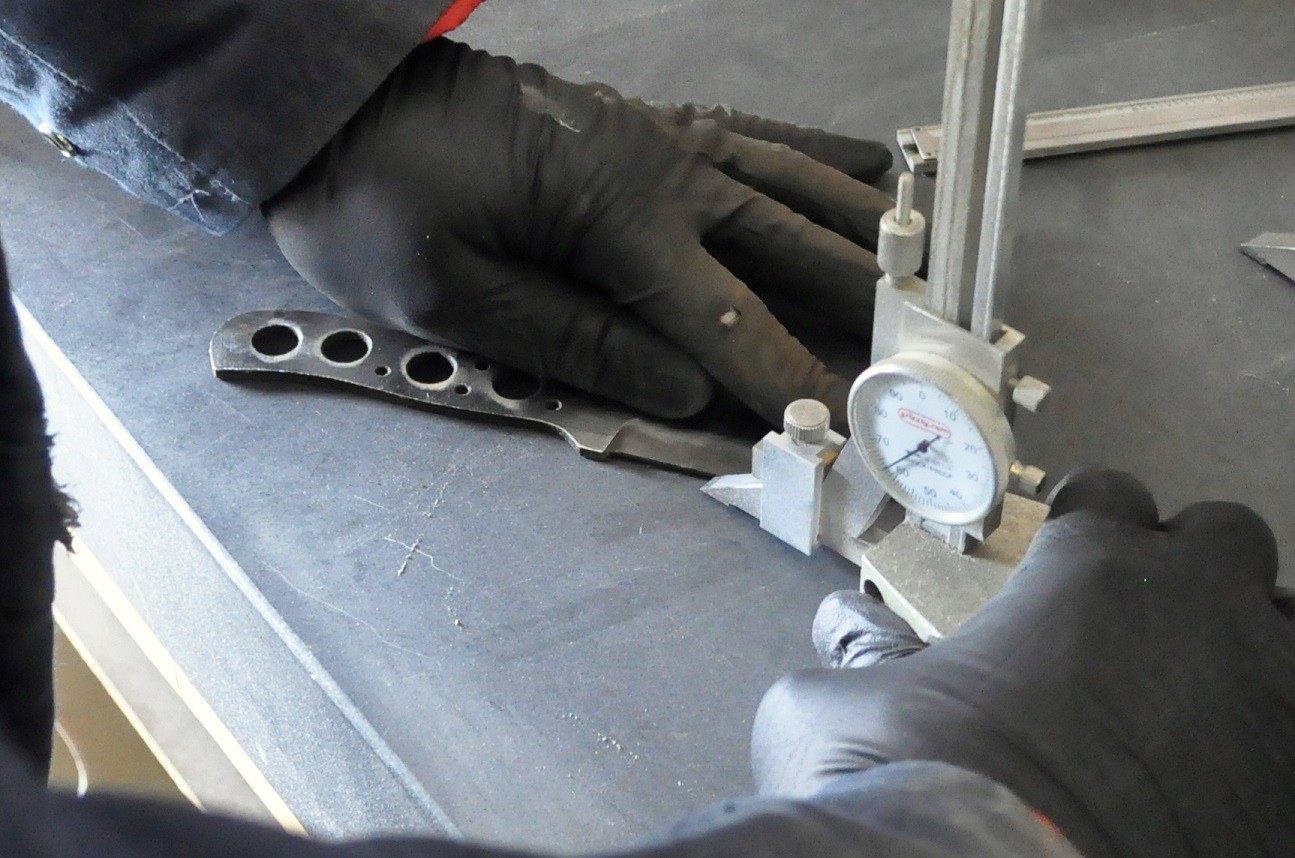
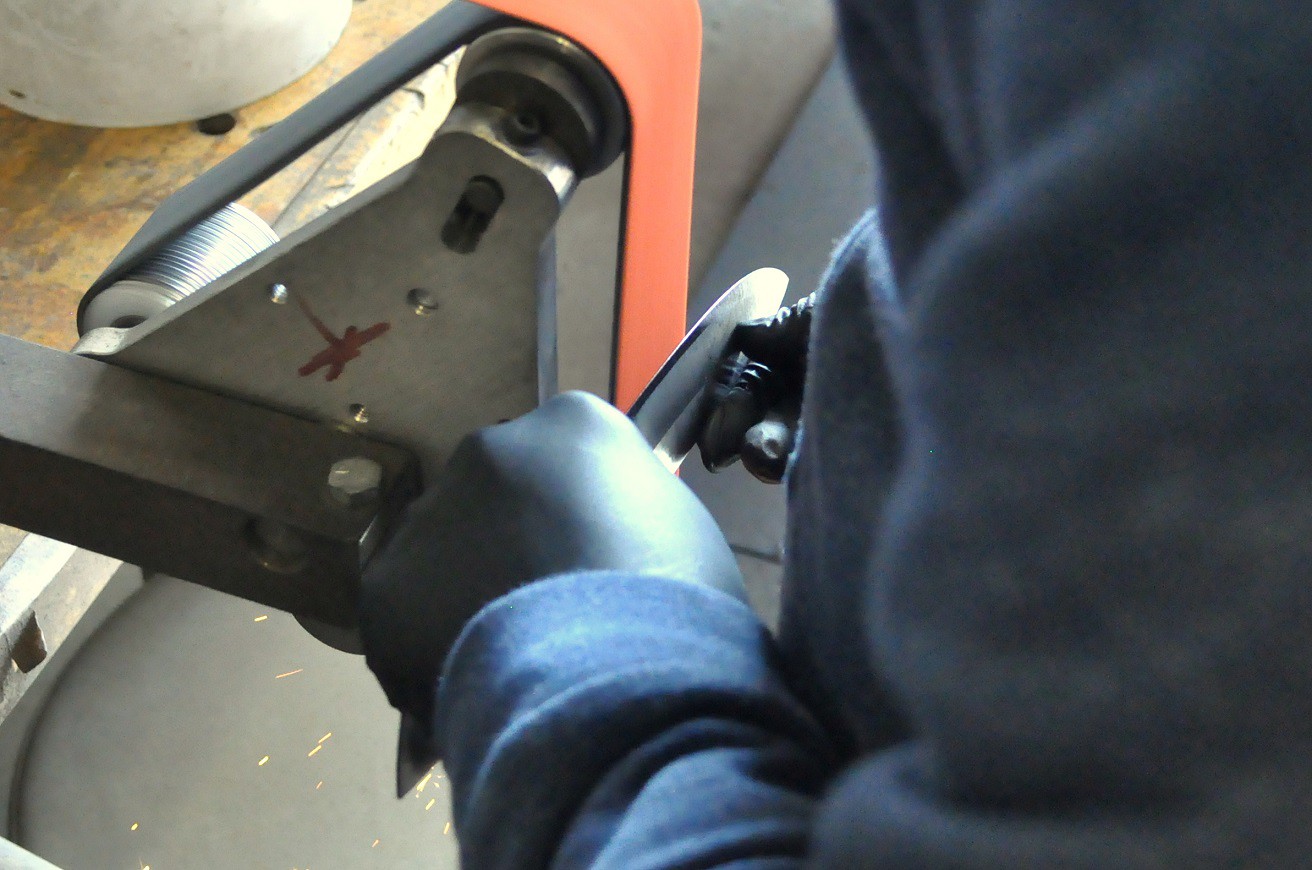
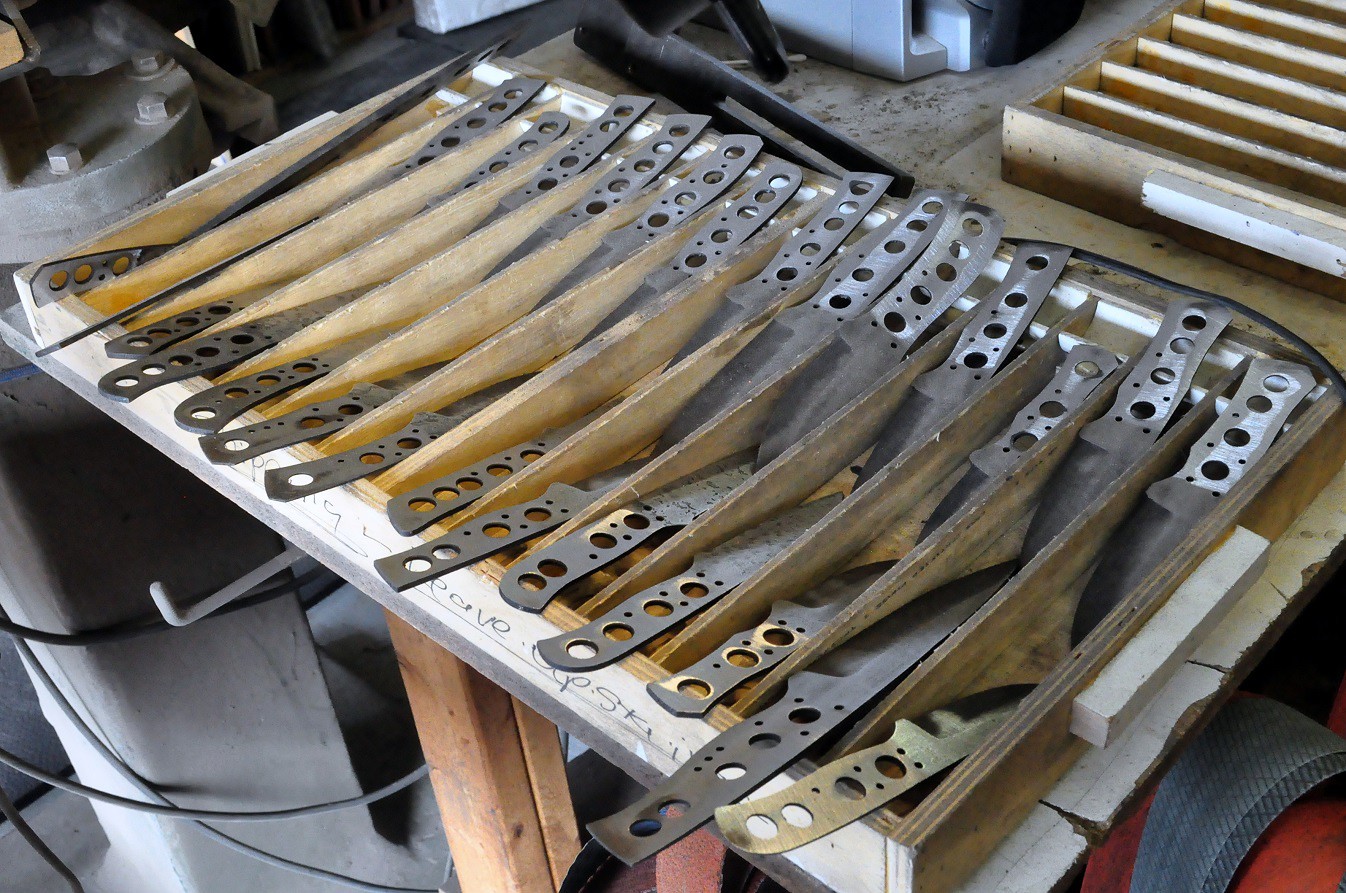
Last edited: