- Joined
- Jul 31, 2015
- Messages
- 3,118
If anyone uses this type of scale attachment, I would appreciate your input on the process you use. I have a process I believe will work, but it involves a good number of steps, and I'm thinking that someone has a simpler process (I like lowering the chance of error/ K.I.S.S.)
The hardware is 1/4" OD standoffs. 10-32 threads. Thanks in advance.
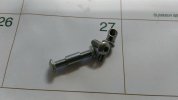
The hardware is 1/4" OD standoffs. 10-32 threads. Thanks in advance.
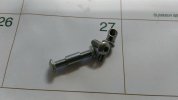