- Joined
- Apr 12, 2021
- Messages
- 22
Hi, still kinda new at this. Can you help with a 2x72 build? I liberated the motor from a treadmill…its destiny is to power a grinder.
The motor has a threaded 1.25” arbor, and I can’t find a drive wheel for it. Everything seems to be 3/4, 5/8 or 7/8.
The motor has a threaded 1.25” arbor, and I can’t find a drive wheel for it. Everything seems to be 3/4, 5/8 or 7/8.
- Can I get a drive wheel that fits?
- I found an adapter…are there downsides to using one?
- Is destiny unavoidable?
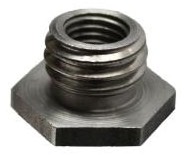
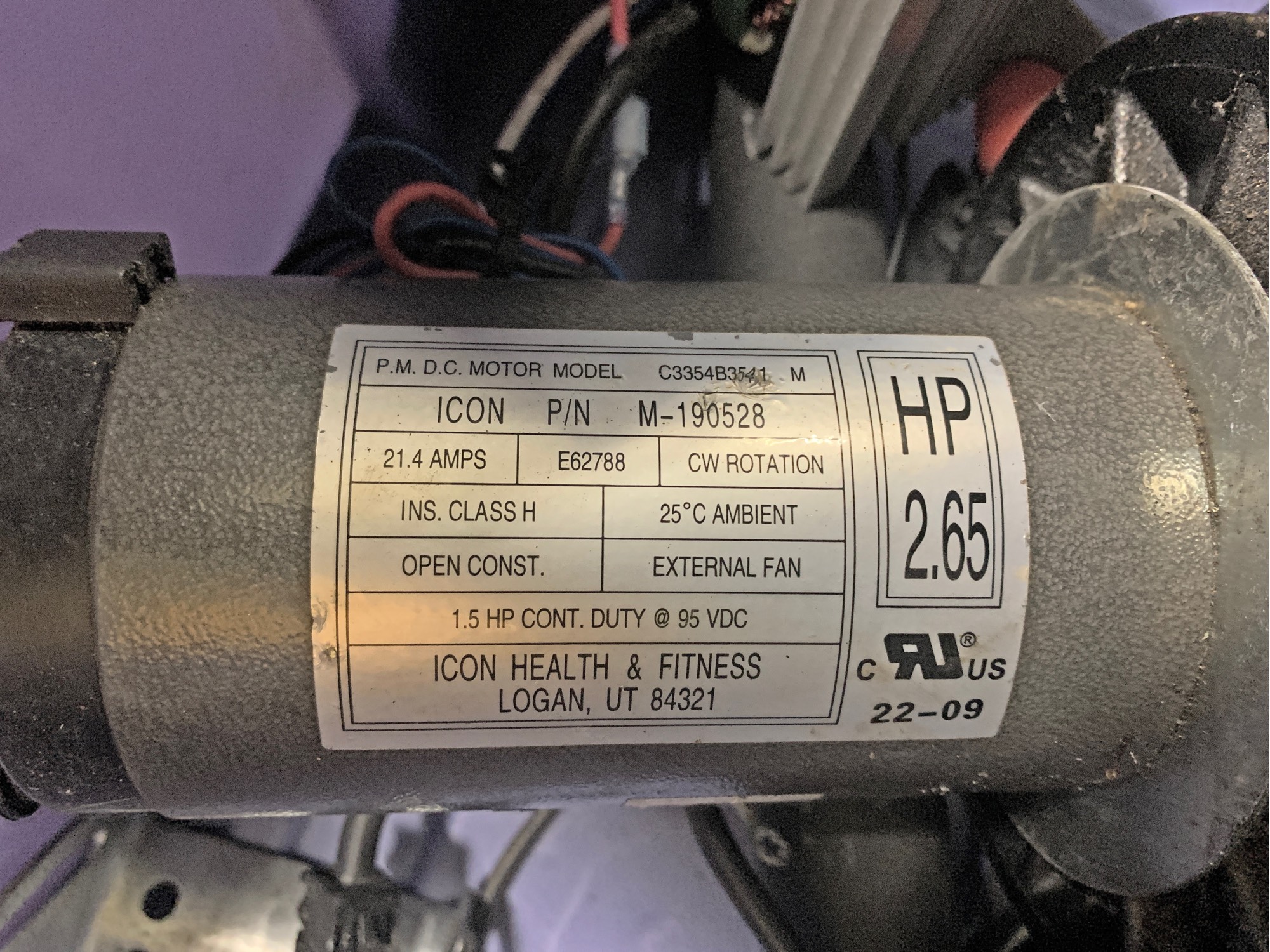
Last edited: