- Joined
- Jun 30, 2004
- Messages
- 376
Finally bit the bullet on a band saw. Got the Milwaukee 6232-21 and fabricated a vertical mount pedestal table for it. followed the same concept as the swag off road table.
All metal is 3/16" thick. the table and base are 12x12". the riser is 4x3"
I used the bandsaw to cut the slot for the blade. once it hit the body of the saw I was able to trace the countour and mark the spot where the table inserts into the vent port. Ground the excess off and then finished cutting the slot the full length. Drilled a small hole at the end of the slot for the chips to fall through.
The saw is held in place with a single bolt which goes through the little mini table on the saw. Just loosen it up a bit and the saw can be removed and used as a portable saw again.
I'll get it painted tomorrow.
Cheers.
All metal is 3/16" thick. the table and base are 12x12". the riser is 4x3"
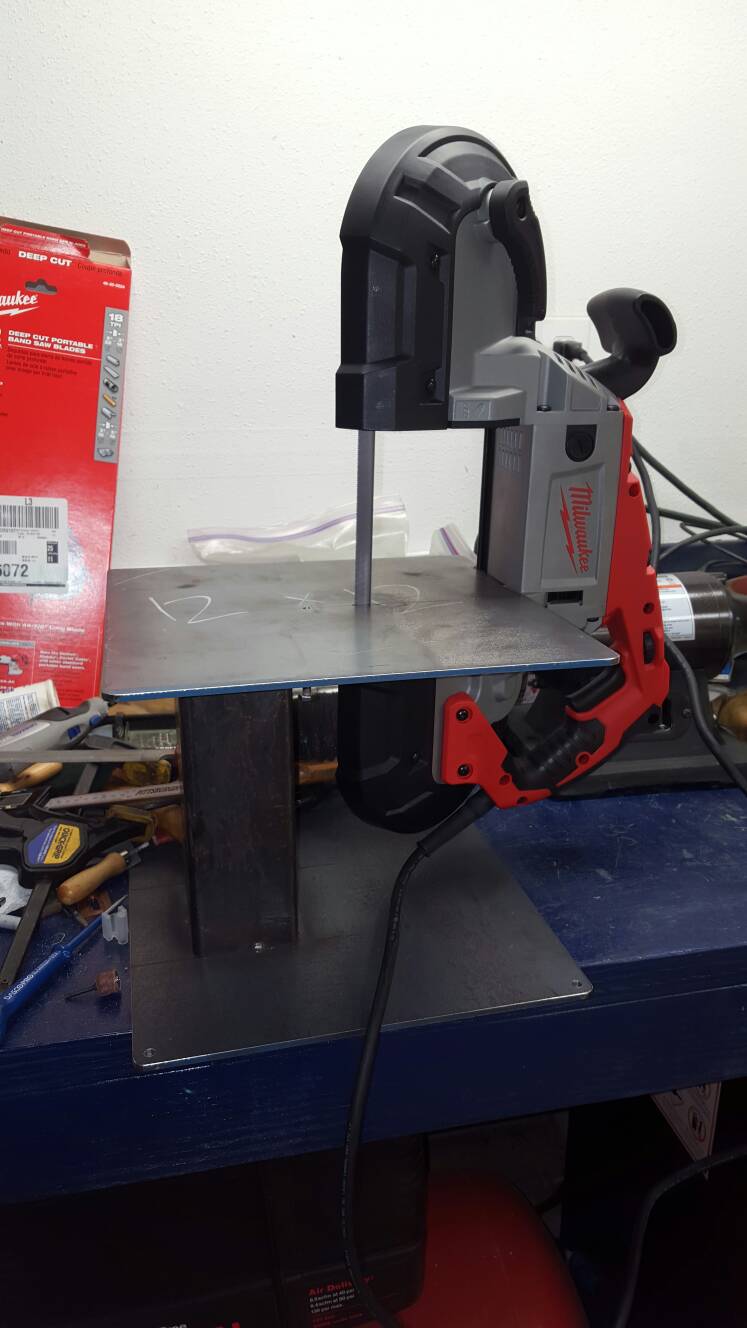
I used the bandsaw to cut the slot for the blade. once it hit the body of the saw I was able to trace the countour and mark the spot where the table inserts into the vent port. Ground the excess off and then finished cutting the slot the full length. Drilled a small hole at the end of the slot for the chips to fall through.
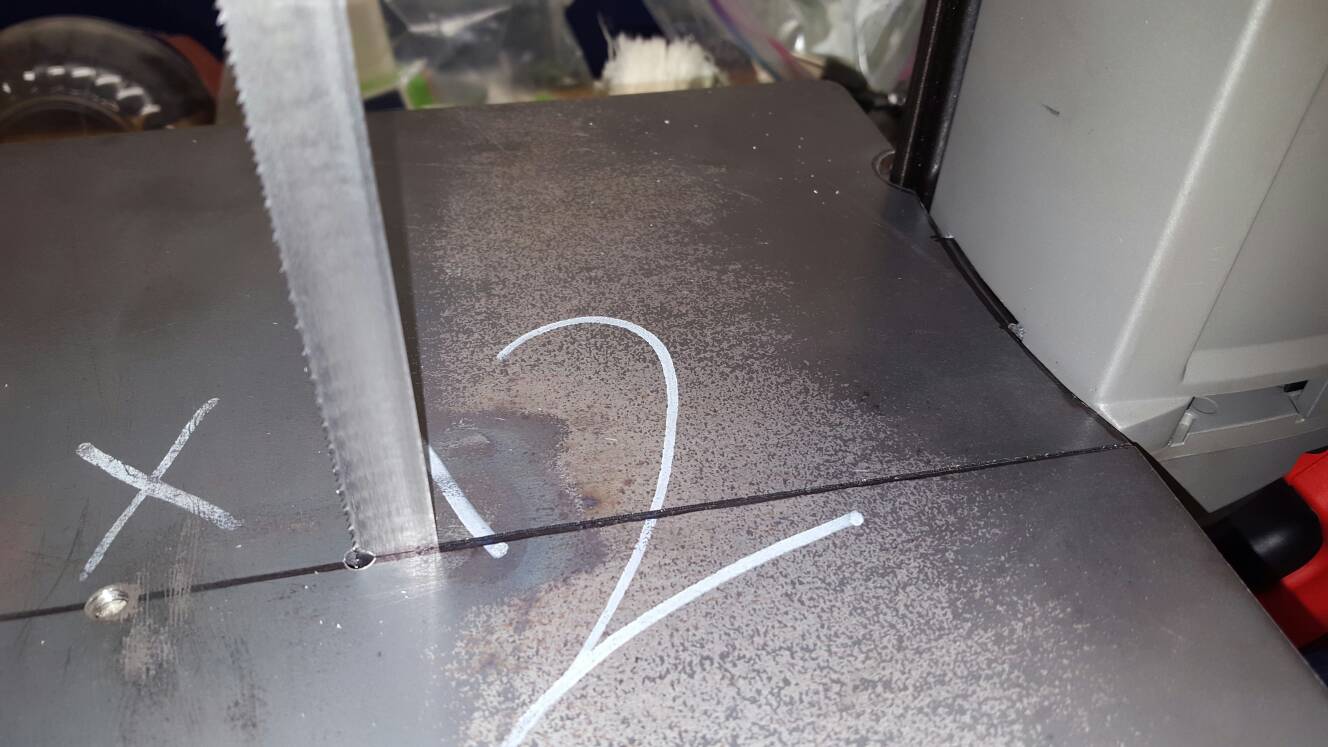
The saw is held in place with a single bolt which goes through the little mini table on the saw. Just loosen it up a bit and the saw can be removed and used as a portable saw again.

I'll get it painted tomorrow.
Cheers.