Square_peg
Gold Member
- Joined
- Feb 1, 2012
- Messages
- 13,826
Here's the full story of restoring an old Walters and creating a knob end handle for it. The inspiration for this build came from an old thread we had last Spring:
Full size single bit design
https://www.bladeforums.com/threads/full-size-single-bit-design.1480730/#post-17035485
I started with a perfect hickory stave sent to me by Quinton. Air dried, perfectly straight grained and about 39" long - enough to do whatever I pleased with.
I have never worked with a hickory stave before. It's not available here in the NW. First thing I learned is that it is tough! Even the bark is miserably tough. A draw knife wouldn't touch it. I had to chisel the bark off with a heavy slick and I was still beating the slick until I got to the last 1/2" from the end of the piece. Amazing stuff that hickory bark. I learned it is used for weaving chairs. My friends wife does some weaving so I called her and she actually needs some hickory bark to repair an old chair so the bark is claimed.
After de-barking I rough shaped the stave with a Lancelot carving tool on my angle grinder. A Lancelot is a real wood eater.
Next I power planed it just enough to give me flat surfaces to lay out my pattern. I shaped the swell similar to some Walters hafts that 300Six posted on these forums.
Then I cut kerfs 3/16" short of my pattern and chiseled off the chunks. I designed for a 36" haft from top of eye to top tip of the grip. The swell adds another 1/2"
Next I sanded close to my lines with a 16 grit disc on a 7-1/4" angle grinder. This made quick work. I switched to a 60 grit disc and cleaned it up to lay out my next profile.
I scribed a center line off the flattest side of the stave and laid out my pattern from that.
Again I kerfed, chipped and sanded.
At this point I had a pretty good handle blank. I set my axe on the blank, aligned the bit to the haft and traced the eye on the end of the haft. Some of you may have run across axes where the eye didn't align perfectly with the bit. By tracing the eye with the bit aligned to the haft I avoid trouble here.
I cut out the eye with the disc sander.
Now I can reference bit alignment the whole time I'm shaping this haft. The shaping was done from here with rasps. Small half round rasps for the swell, larger flat rasps for the haft. Rough work is smoothed out with a 10" 4-in-hand rasp.
Occasionally I would stop and sight down the haft to make sure I was keeping it straight and symmetrical.
After about 8 hours work I had a finished handle.
Axe restoration work in my next post.
Full size single bit design
https://www.bladeforums.com/threads/full-size-single-bit-design.1480730/#post-17035485
I started with a perfect hickory stave sent to me by Quinton. Air dried, perfectly straight grained and about 39" long - enough to do whatever I pleased with.
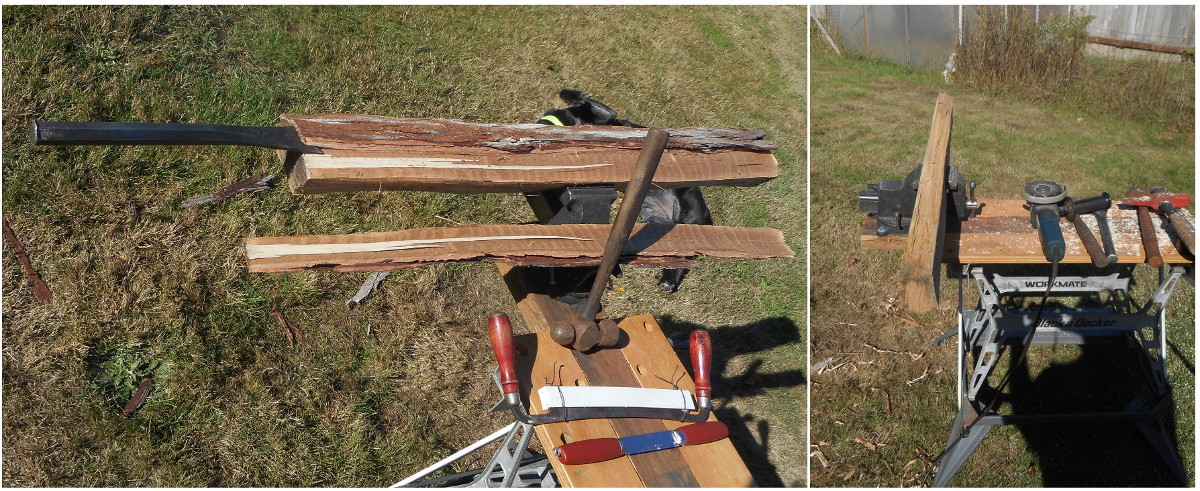
I have never worked with a hickory stave before. It's not available here in the NW. First thing I learned is that it is tough! Even the bark is miserably tough. A draw knife wouldn't touch it. I had to chisel the bark off with a heavy slick and I was still beating the slick until I got to the last 1/2" from the end of the piece. Amazing stuff that hickory bark. I learned it is used for weaving chairs. My friends wife does some weaving so I called her and she actually needs some hickory bark to repair an old chair so the bark is claimed.
After de-barking I rough shaped the stave with a Lancelot carving tool on my angle grinder. A Lancelot is a real wood eater.
Next I power planed it just enough to give me flat surfaces to lay out my pattern. I shaped the swell similar to some Walters hafts that 300Six posted on these forums.
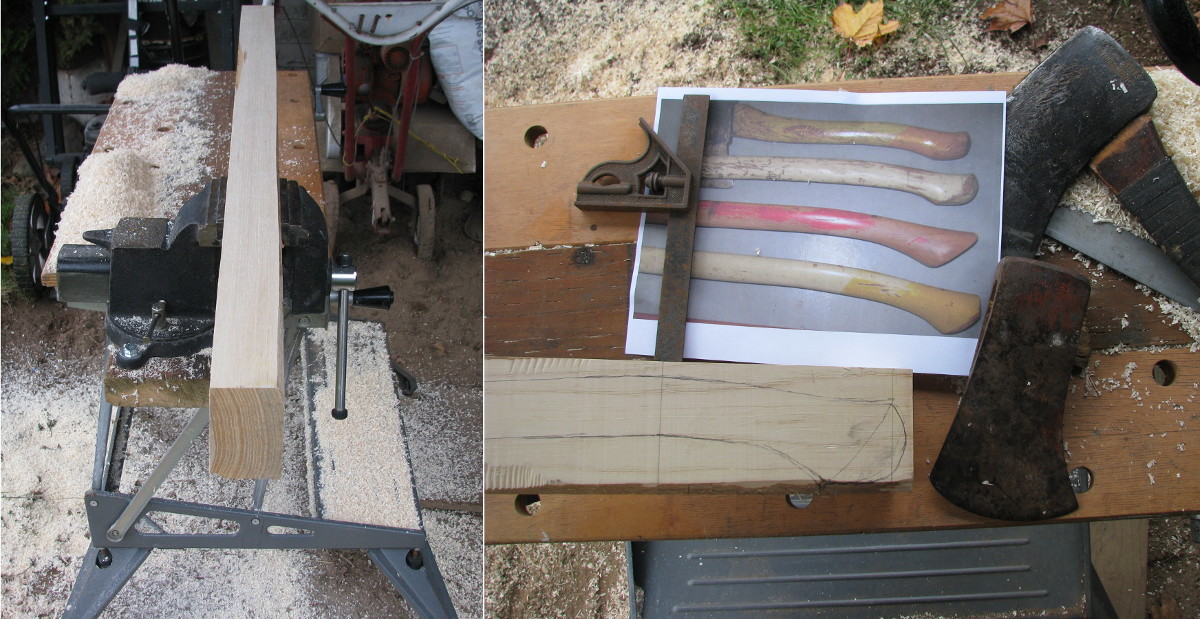
Then I cut kerfs 3/16" short of my pattern and chiseled off the chunks. I designed for a 36" haft from top of eye to top tip of the grip. The swell adds another 1/2"
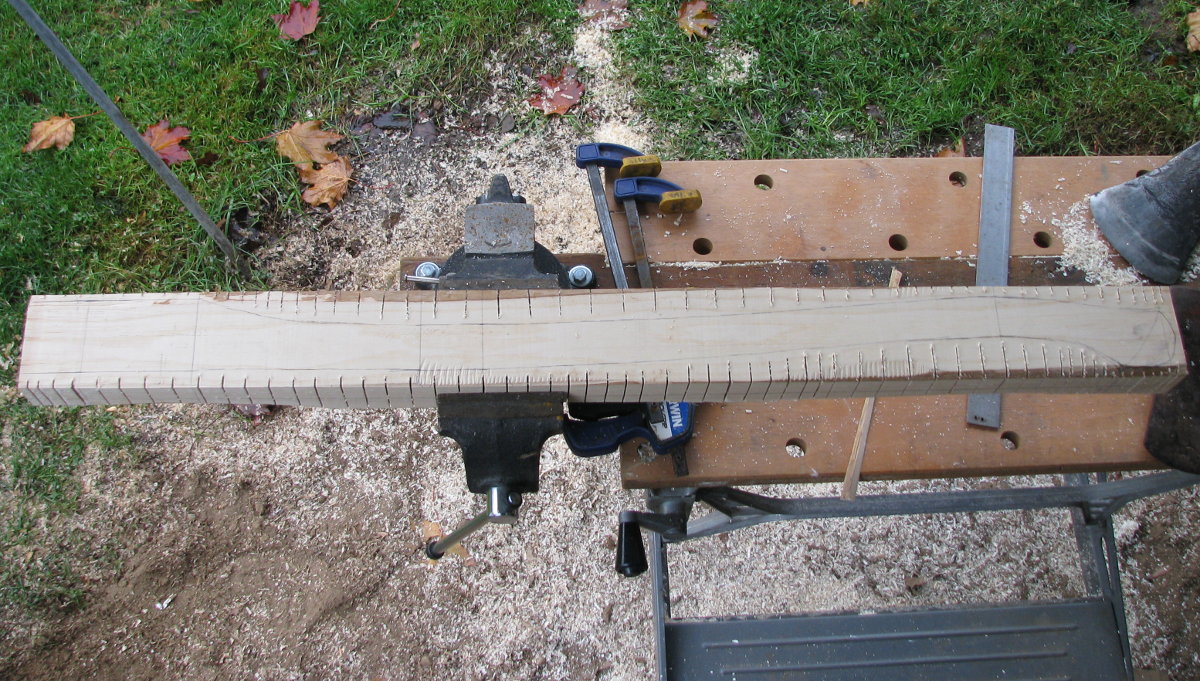
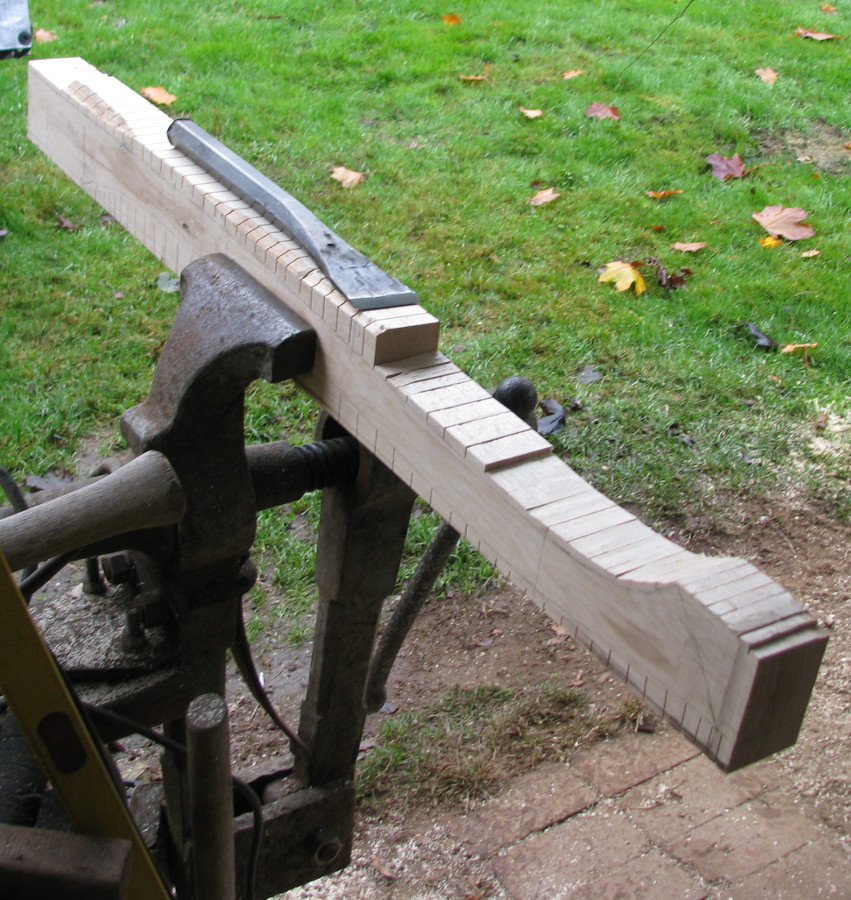
Next I sanded close to my lines with a 16 grit disc on a 7-1/4" angle grinder. This made quick work. I switched to a 60 grit disc and cleaned it up to lay out my next profile.
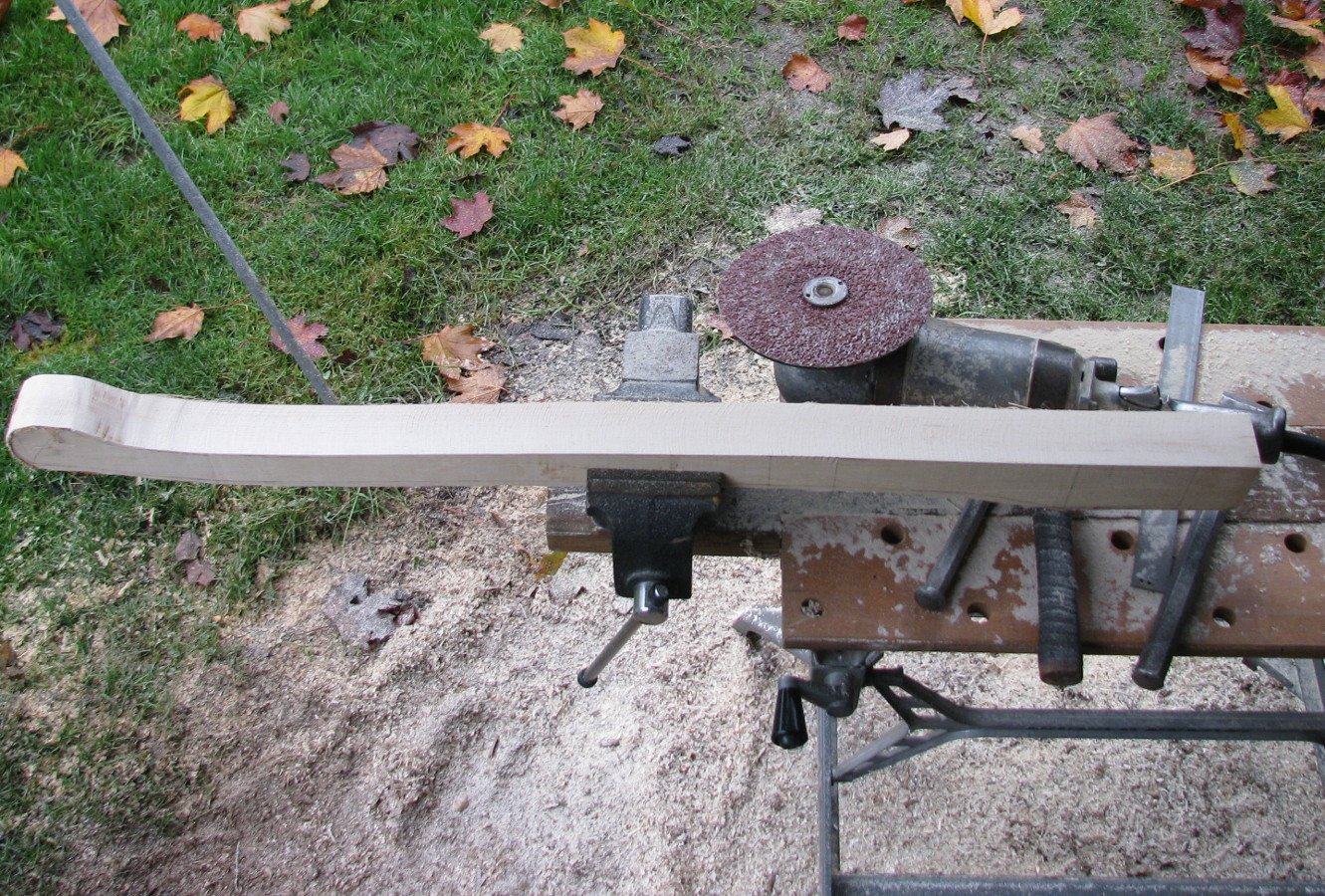
I scribed a center line off the flattest side of the stave and laid out my pattern from that.
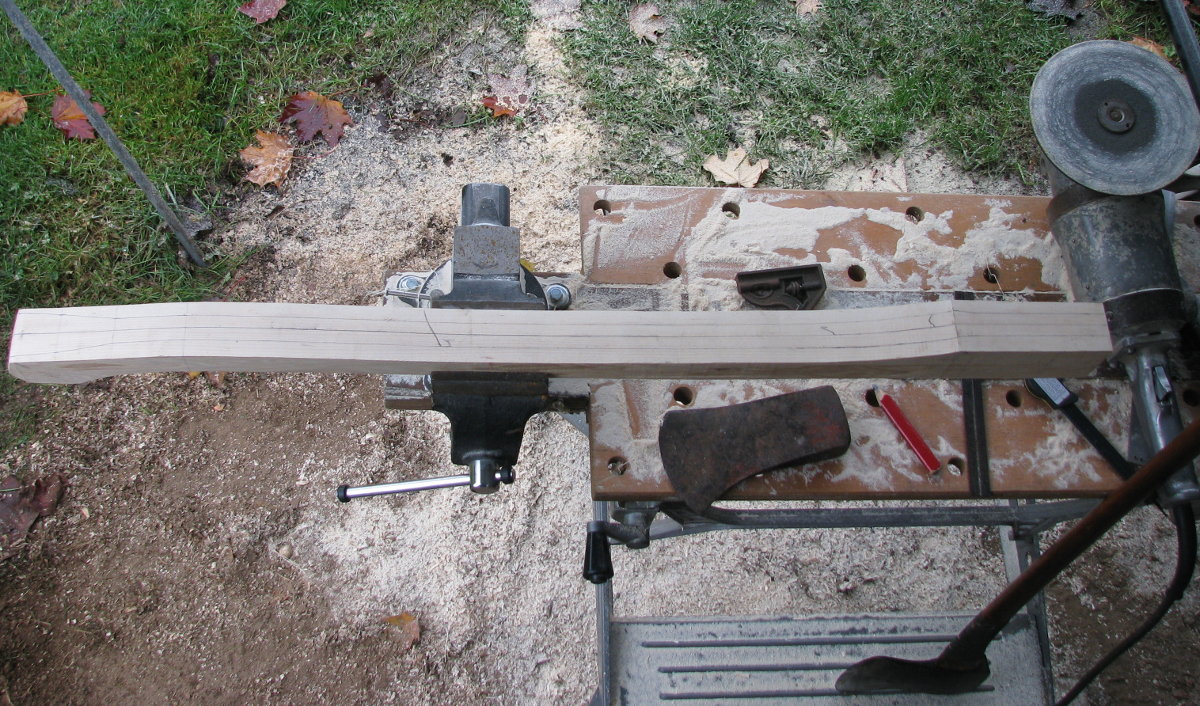
Again I kerfed, chipped and sanded.
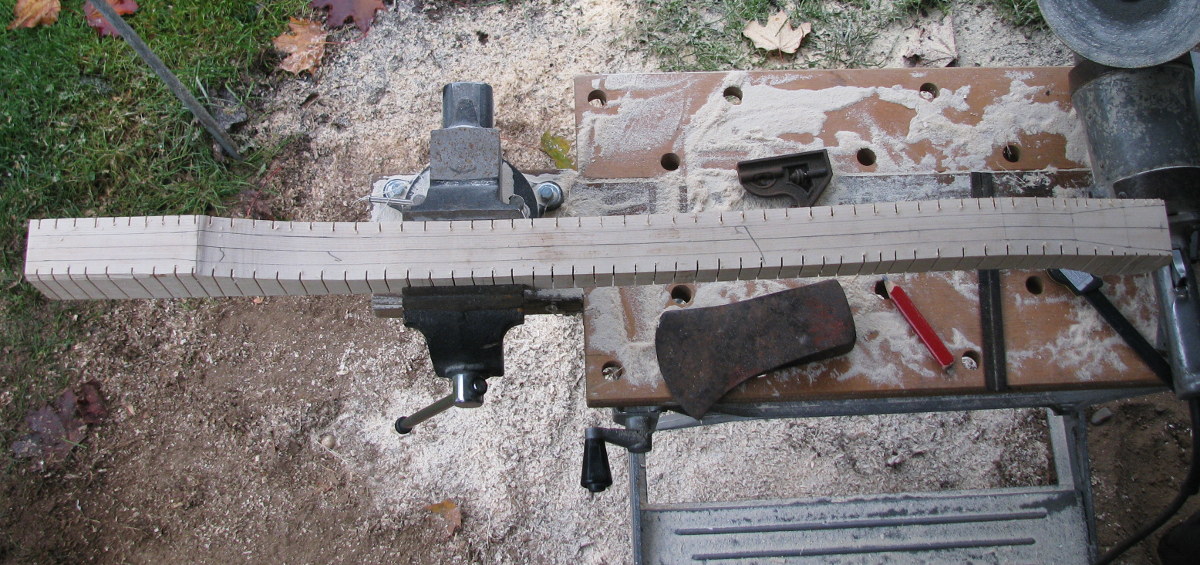
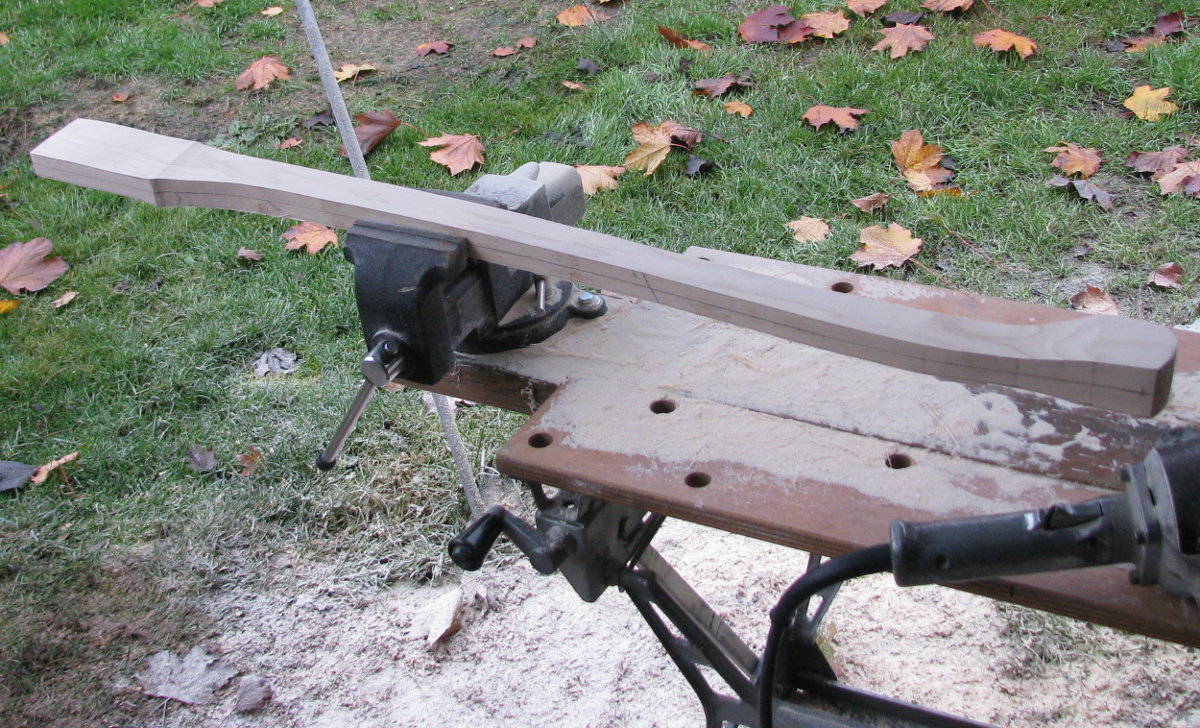
At this point I had a pretty good handle blank. I set my axe on the blank, aligned the bit to the haft and traced the eye on the end of the haft. Some of you may have run across axes where the eye didn't align perfectly with the bit. By tracing the eye with the bit aligned to the haft I avoid trouble here.
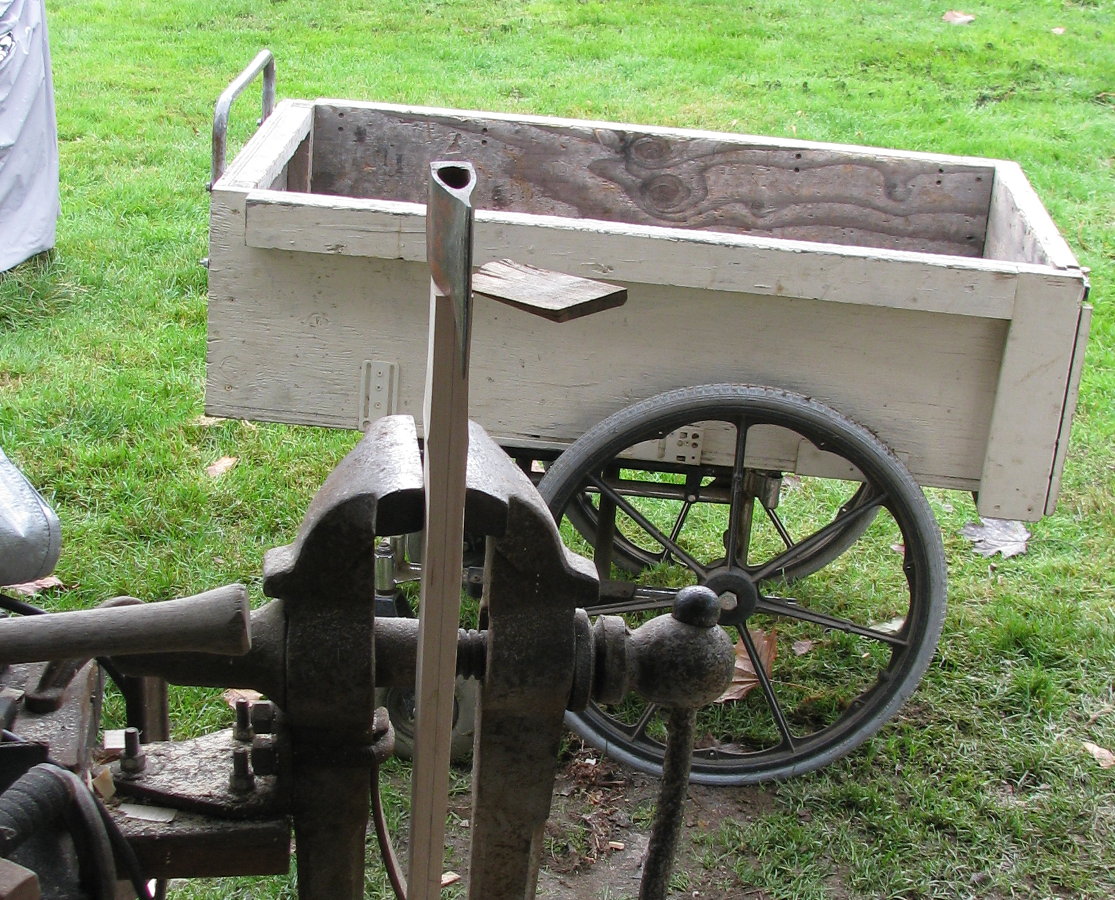
I cut out the eye with the disc sander.
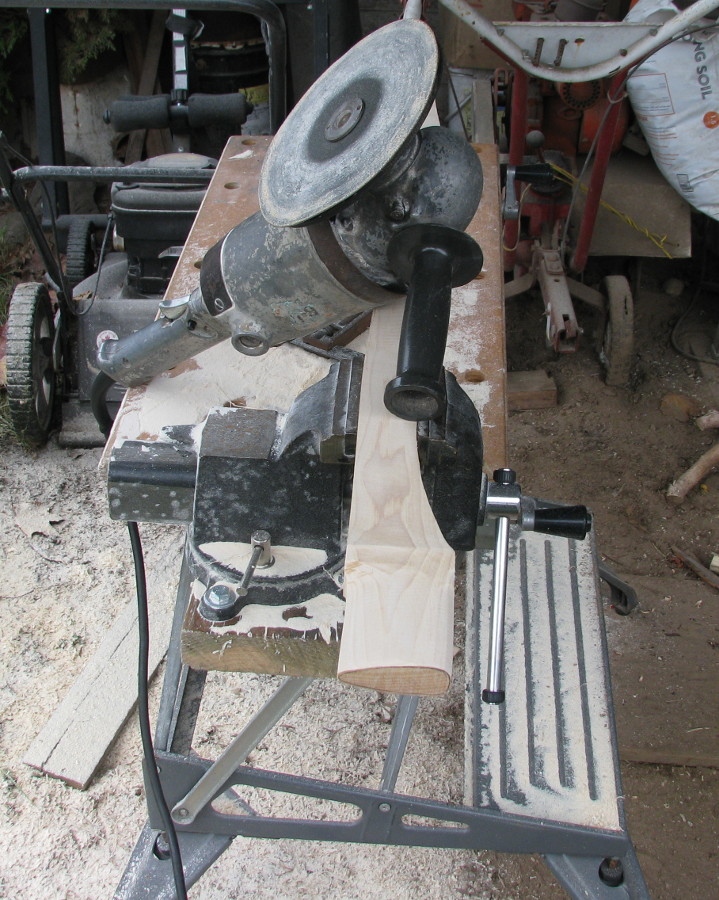
Now I can reference bit alignment the whole time I'm shaping this haft. The shaping was done from here with rasps. Small half round rasps for the swell, larger flat rasps for the haft. Rough work is smoothed out with a 10" 4-in-hand rasp.
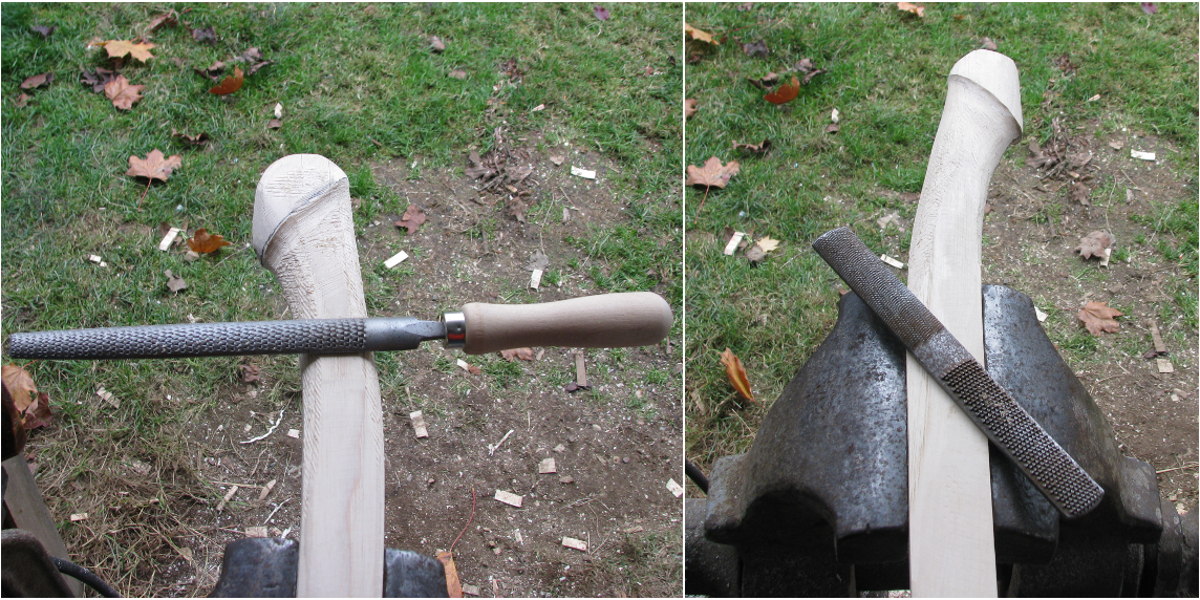
Occasionally I would stop and sight down the haft to make sure I was keeping it straight and symmetrical.
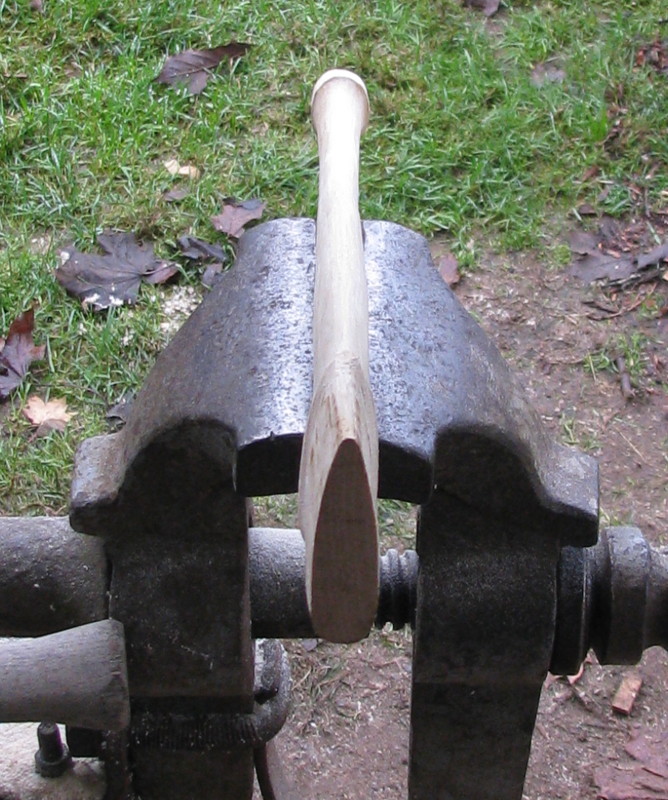
After about 8 hours work I had a finished handle.
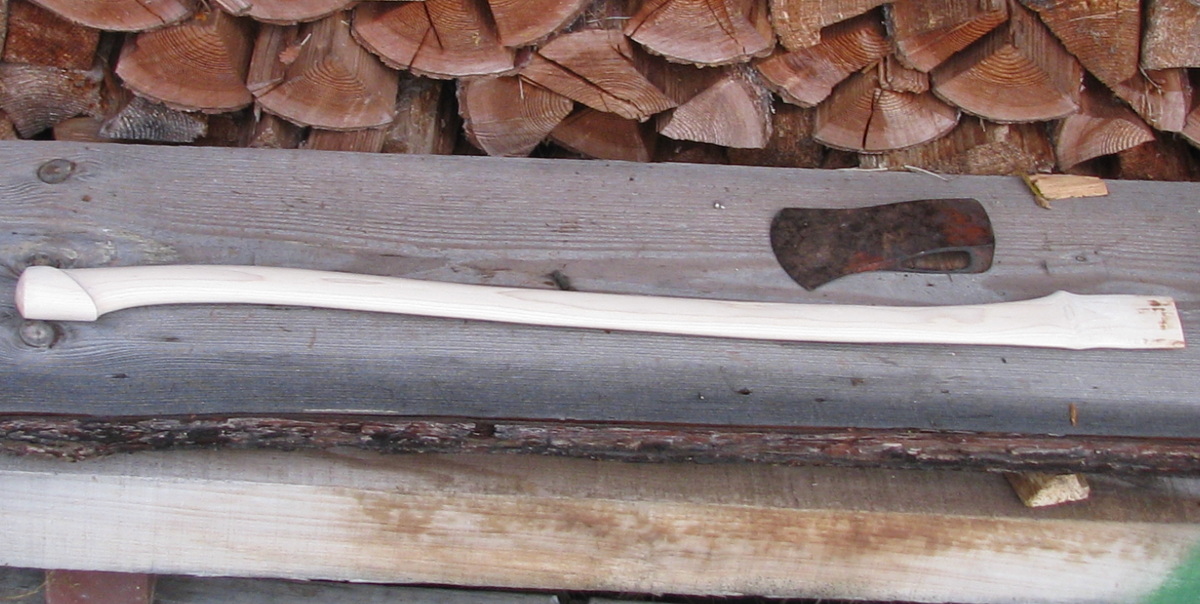
Axe restoration work in my next post.
Last edited: