- Joined
- Apr 1, 2010
- Messages
- 261
I posted on here years ago planning to make a knife from a railroad spike. Unfortunantly life got in the way, and then I lost the spikes during a move.
Now I finally have time to try and make a few knives. This time I intend to do stock removal. My uncle heard and gave me this piece of tool steel he had in his garage. He didn't remember where it came from just that it was tool steel.
The first part is obviously the measurements. Based on the second have I assume it is D2. Is that a safe assumption?
Now 1/2 inch is much to thick for knives so I intend to look into having a local machine shop cut it down. Since D2 is an air hardening steel, water jet cutting seems to me the best option. Am I correct, would laser or some other cutting method be better?
Lastly, is this plan even reasonable? Should I just set this steel aside until I start forging? From what I understand D2 is difficult to forge and needs to be kept between 1700° and 1900° ferinheight, ideal at 1800°.
Now I finally have time to try and make a few knives. This time I intend to do stock removal. My uncle heard and gave me this piece of tool steel he had in his garage. He didn't remember where it came from just that it was tool steel.
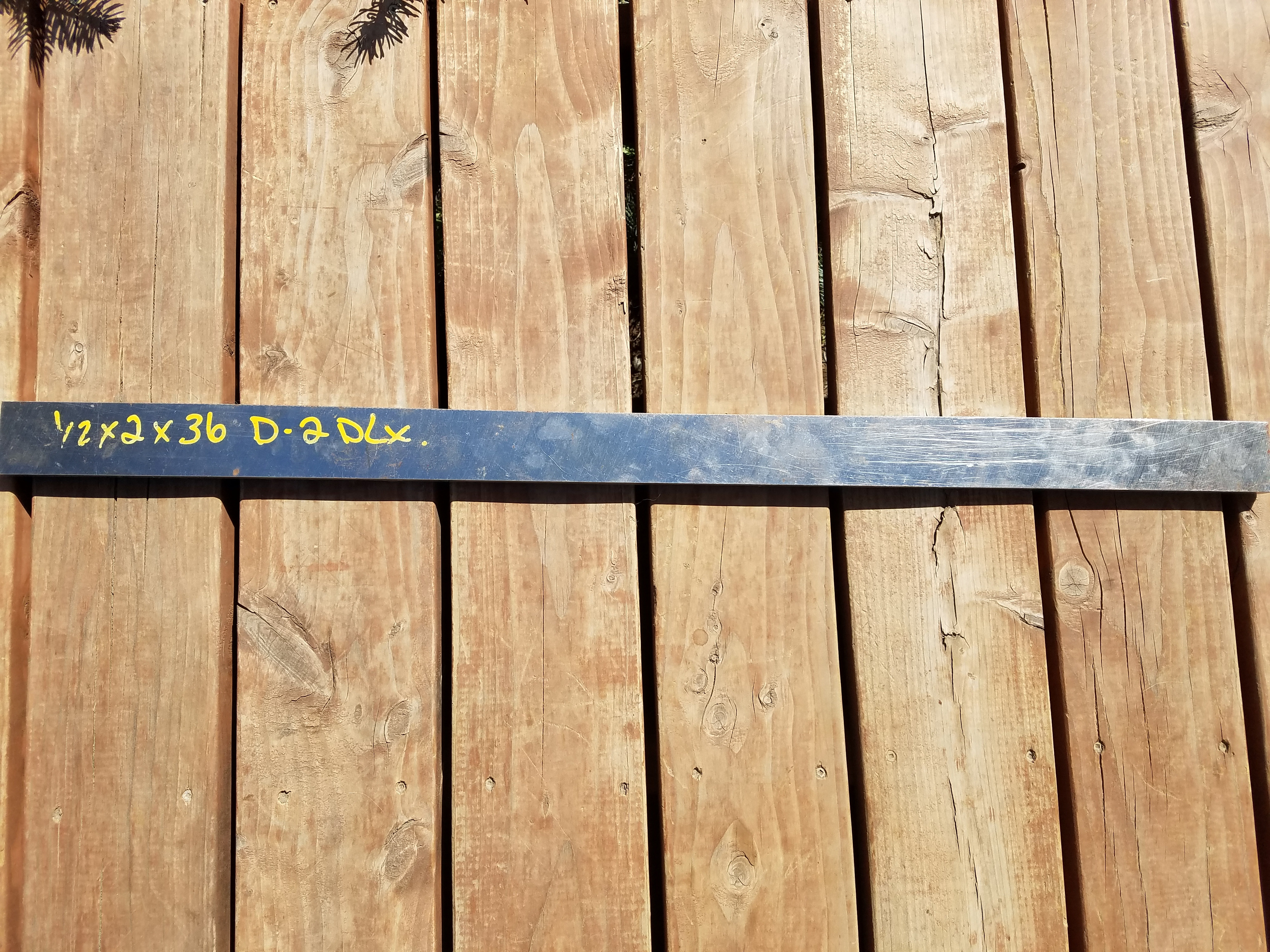
The first part is obviously the measurements. Based on the second have I assume it is D2. Is that a safe assumption?
Now 1/2 inch is much to thick for knives so I intend to look into having a local machine shop cut it down. Since D2 is an air hardening steel, water jet cutting seems to me the best option. Am I correct, would laser or some other cutting method be better?
Lastly, is this plan even reasonable? Should I just set this steel aside until I start forging? From what I understand D2 is difficult to forge and needs to be kept between 1700° and 1900° ferinheight, ideal at 1800°.