- Joined
- Mar 26, 2004
- Messages
- 1,617
Hi guys, I've finally made some rings and wanted to share how I've made them from scratch, I hope you'll enjoy the process!
Some drum cymbals pieces I had laying around from my other work (I fix drum parts)
Cutting some 100 x 35 mm pieces.
Different color cymbal pieces to make the resulting mokume look nice next to the forging capsule
Inside the forging capsule.
Putting the capsule in the over using a welded steel bar to hold it.
Getting it out of the oven at about 850C.
Pressing to weld the metals.
Already cold so I can keep working on it.
I use an angular grinder to cut the laterals.
Using the grinder, I also make it somewhat round so I can take it to the lathe.
Details of another bar.
Making the ingot round.
Drilling to the aproximated ring size.
Working to get to the desired ring size.
Ring about to be cut from the round bar.
Ring right out of the bar.
Placing the ring in a 50/50 solution of destiled water and ferric chloride to accelerate the oxidation and reveal the different colors of the metals.
Ring after the acid bath
Polished and finished rings.
For the copper/stainless rings it's pretty much the same process, only 900C in the oven, and they end up looking like this
I'll be making more in copper/brass, brass/stainless and stainless damascus.
For more pictures of the rings, please take a look at the Jewelry page on my website:
http://www.aescustomknives.com/docs/galleryjewelry.htm
Sign up for my Newsletter:
http://yourwebapps.com/WebApps/mail-list-subscribe.cgi?list=79955
Thanks for looking!
Ariel
Some drum cymbals pieces I had laying around from my other work (I fix drum parts)
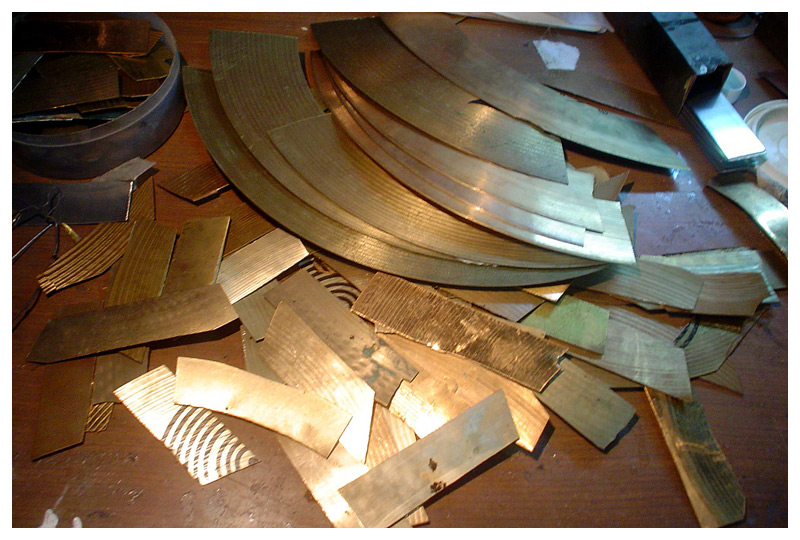
Cutting some 100 x 35 mm pieces.

Different color cymbal pieces to make the resulting mokume look nice next to the forging capsule
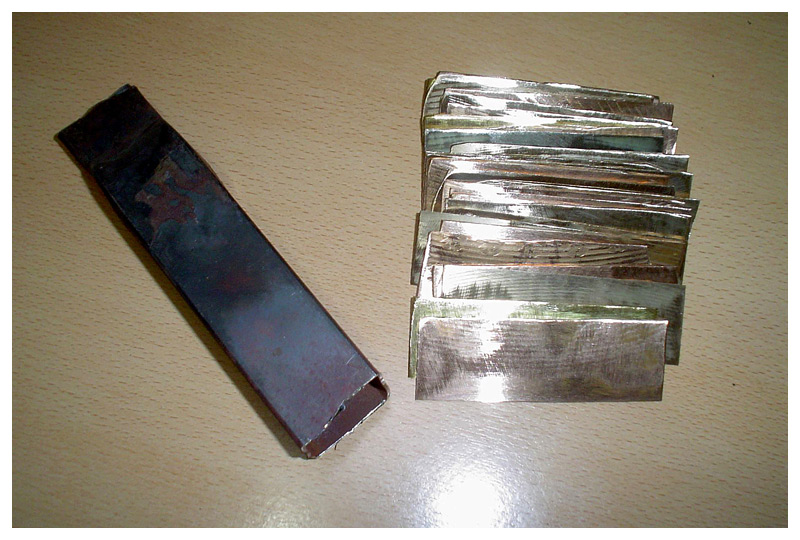
Inside the forging capsule.

Putting the capsule in the over using a welded steel bar to hold it.

Getting it out of the oven at about 850C.

Pressing to weld the metals.

Already cold so I can keep working on it.

I use an angular grinder to cut the laterals.

Using the grinder, I also make it somewhat round so I can take it to the lathe.
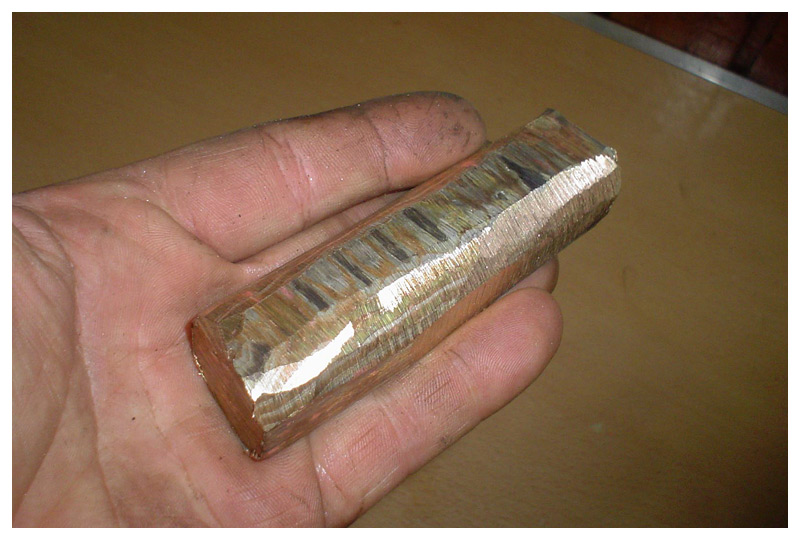
Details of another bar.
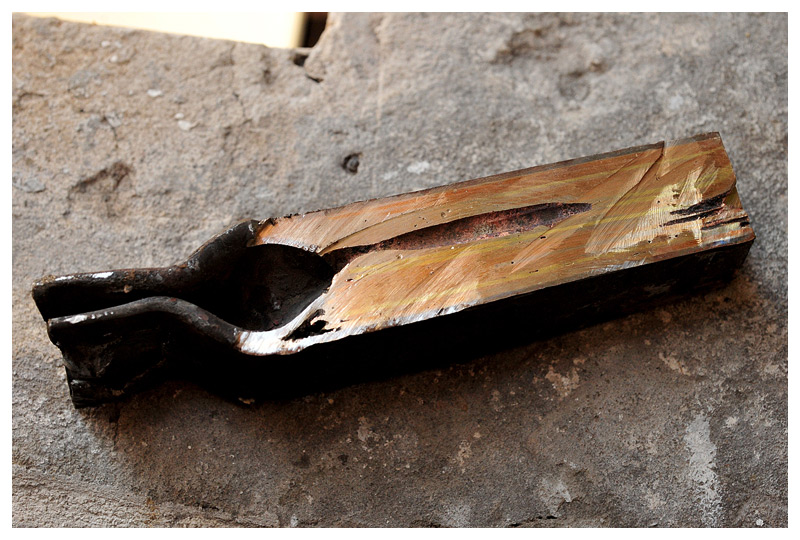

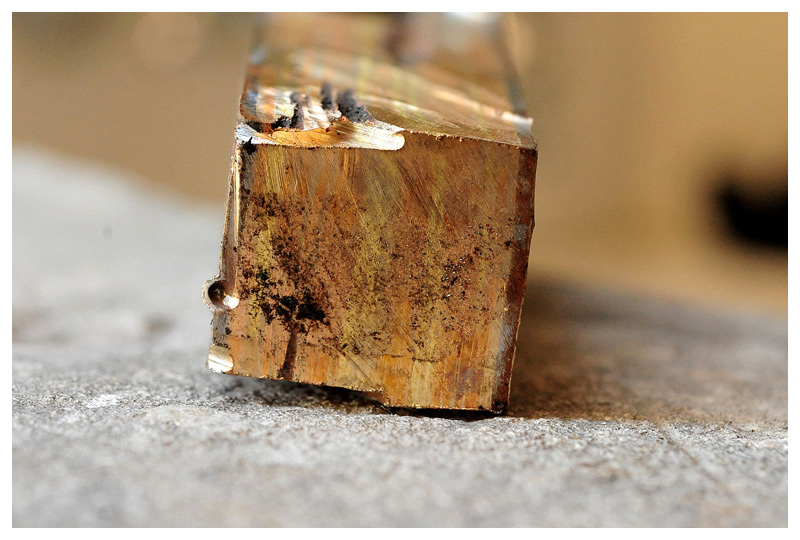

Making the ingot round.

Drilling to the aproximated ring size.

Working to get to the desired ring size.

Ring about to be cut from the round bar.
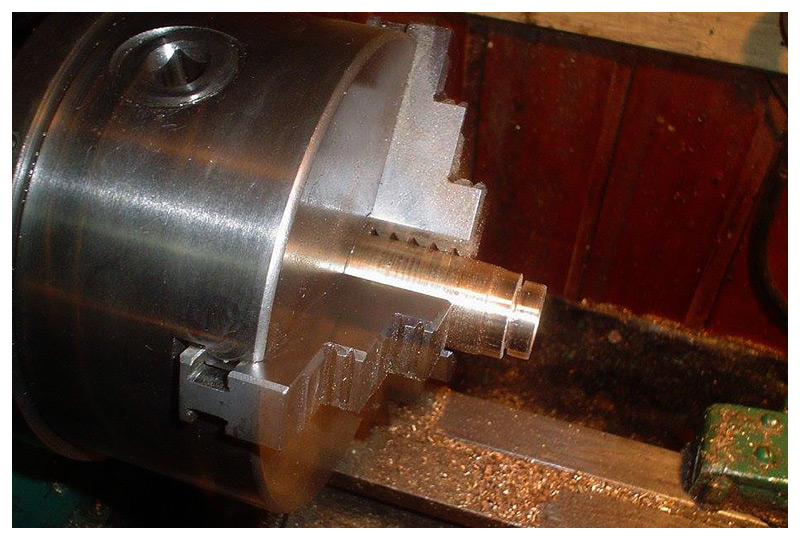
Ring right out of the bar.
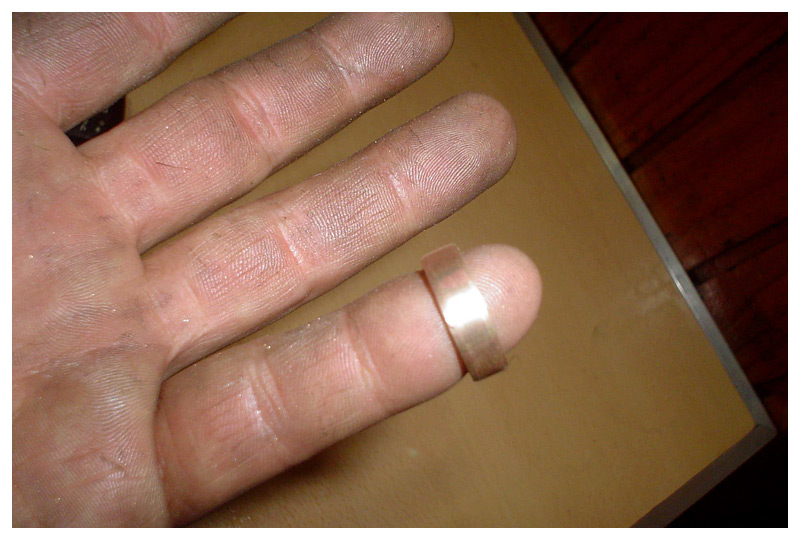
Placing the ring in a 50/50 solution of destiled water and ferric chloride to accelerate the oxidation and reveal the different colors of the metals.

Ring after the acid bath
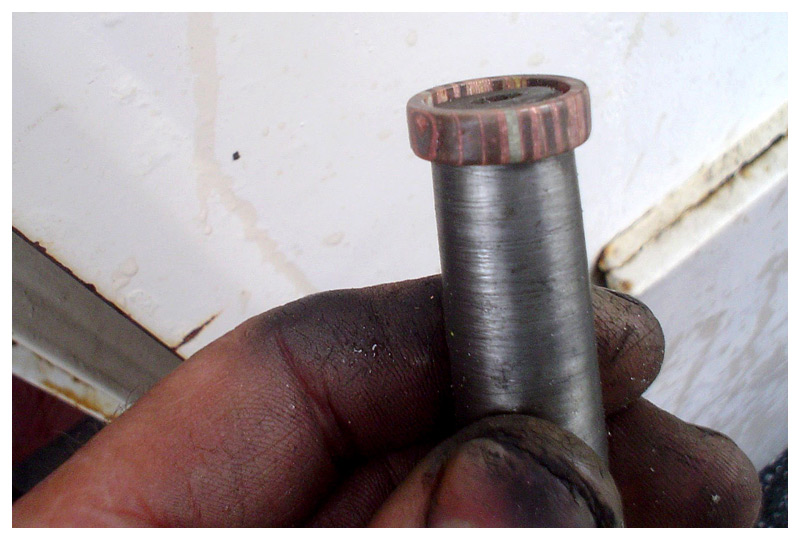

Polished and finished rings.

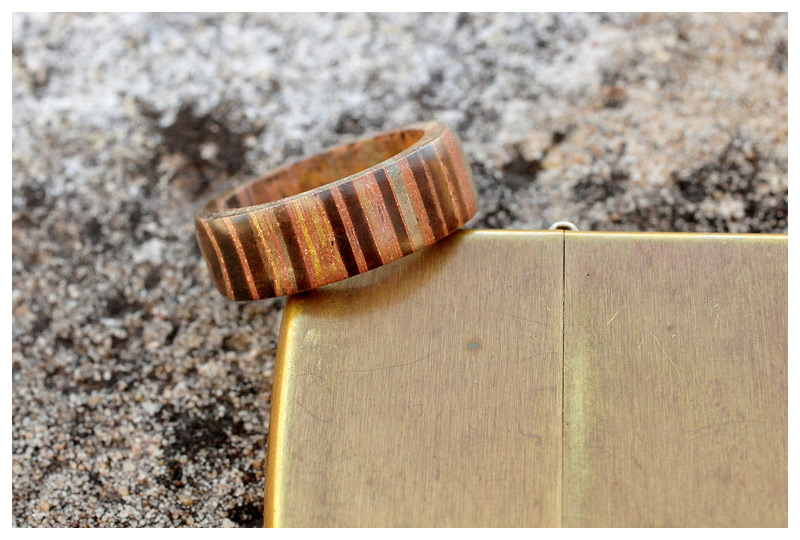

For the copper/stainless rings it's pretty much the same process, only 900C in the oven, and they end up looking like this
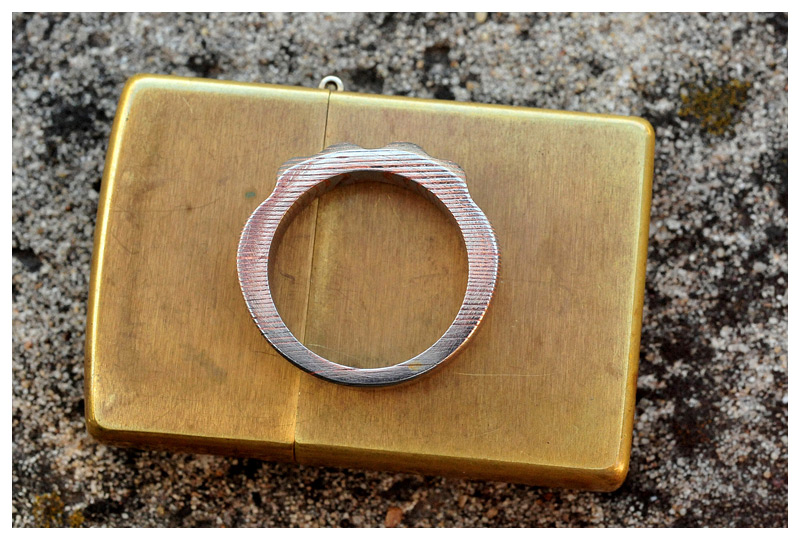
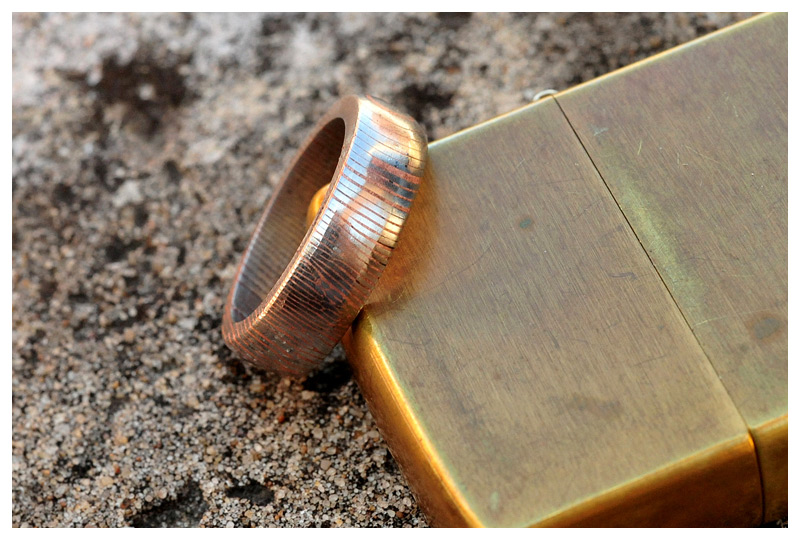
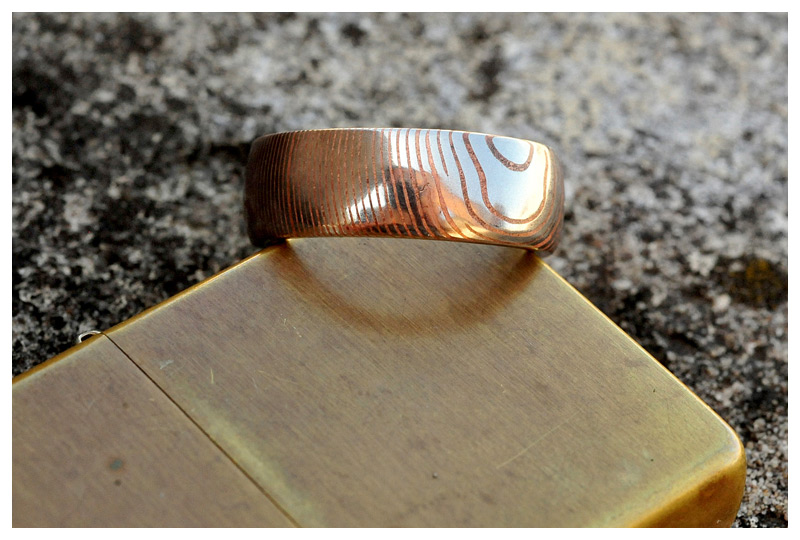
I'll be making more in copper/brass, brass/stainless and stainless damascus.
For more pictures of the rings, please take a look at the Jewelry page on my website:
http://www.aescustomknives.com/docs/galleryjewelry.htm
Sign up for my Newsletter:
http://yourwebapps.com/WebApps/mail-list-subscribe.cgi?list=79955
Thanks for looking!
Ariel