Much of what I said about wood polishing applies mainly to small pieces, as opposed to large furniture where the amount of work would be prohibitive. I have seen and sometimes acquired objects and animals carved in exotic woods that could be greatly enhanced by extreme polishing. It's just too time-consuming for the original artists to do, since they have to produce enough pieces to make a living.
I have also seen highly polished dressers and chests of drawers that were extremely beautiful, but they cost a small fortune. Like several thousand dollars for one piece of furniture, and these are usually made in specialty workshops.
As for the idea of achieving a high polish by applying many layers of varnish, lacquer or other finishing compound, all I can say is that the underlying wood has to be highly polished first. Otherwise you're getting a lot of light reflected from the varnish, but you are not seeing deep into the wood. There's just no comparison.
For an example, below are photos of a hippo carved from a very dense African hardwood with an incredibly complex and beautiful grain. When I bought this piece it had what most people would consider an adequate finish and was covered in a thick coat of varnish. I could barely see the underlying grain, but what I did see encouraged me to sand off the varnish -- a lot of work because of all the curves and crevices in the carving. I went through the laborious process of sanding the entire piece with increasingly finer sandpaper, up to 2000 grit. I worked on this thing on and off in spare time for weeks, often while watching television. After the sandpaper came rottenstone powder. By this point I had discovered a whole new grain pattern, like little spiderweb patterns in between the regular grain lines.
I also discovered how brilliant the African carvers were, because the curved grain followed the curves of the hippo from every angle: front, back, top, bottom and sides -- as you can see in the pictures below.
I finished the piece by rubbing in five very thin layers of tung oil compound, each layer a day or two apart, then continued rubbing for a week or so. The details in this wood are incredible, more than you can even see in the pictures, and the best of it would have been invisible if I had not gone through the polishing process. Eventually I mounted the hippo on a matching base of bubinga, which i polished the same way, except that it was much faster to do the flat, rectangular base. The piece is about 15" long and very heavy.
These are the best pictures I could take, but they still don't show all the grain detail:
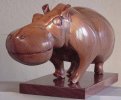