- Joined
- Apr 10, 2011
- Messages
- 153
Ok, here it goes!
I thought about waiting until the project was done, until the bow was a finished success. But, I decided that it might actually be more fun, and you might learn more, by watching it come together (or apart!) in nearly real time. This is a 74" black locust stave, and let me tell you, it has some issues! We've got weather checking, knots, bugs, rot, and what else we will find out as we go. I will be using my fine HI CAK for this project as my main tool. If you have questions as we go, post them up.
[/IMG]
What I've done here is expose, and select a ring on the end of the stave that will be the back of the bow. Sap wood on black locust has very little resistance to tension, so we have to dive down into the heart wood. You want as thick a late wood ring as you can find. That will make the back durable.
[/IMG]
Here, I'm just cutting through the rings until I reach the one I selected for the back.
Ok, I have to apologize for the quality of this picture; it was starting to get dark. I'm pointing at the end of the back ring with my karda, and outlined the edge of the edge of the early wood layer with a marker. Everything above that line will have to be removed, until the ring I've selected to be the back continues unbroken the entire length of the stave. That's it for tonight. I don't know if this stave will ultimately yield a working bow, but we will find out!
[/IMG]
I thought about waiting until the project was done, until the bow was a finished success. But, I decided that it might actually be more fun, and you might learn more, by watching it come together (or apart!) in nearly real time. This is a 74" black locust stave, and let me tell you, it has some issues! We've got weather checking, knots, bugs, rot, and what else we will find out as we go. I will be using my fine HI CAK for this project as my main tool. If you have questions as we go, post them up.

What I've done here is expose, and select a ring on the end of the stave that will be the back of the bow. Sap wood on black locust has very little resistance to tension, so we have to dive down into the heart wood. You want as thick a late wood ring as you can find. That will make the back durable.

Here, I'm just cutting through the rings until I reach the one I selected for the back.
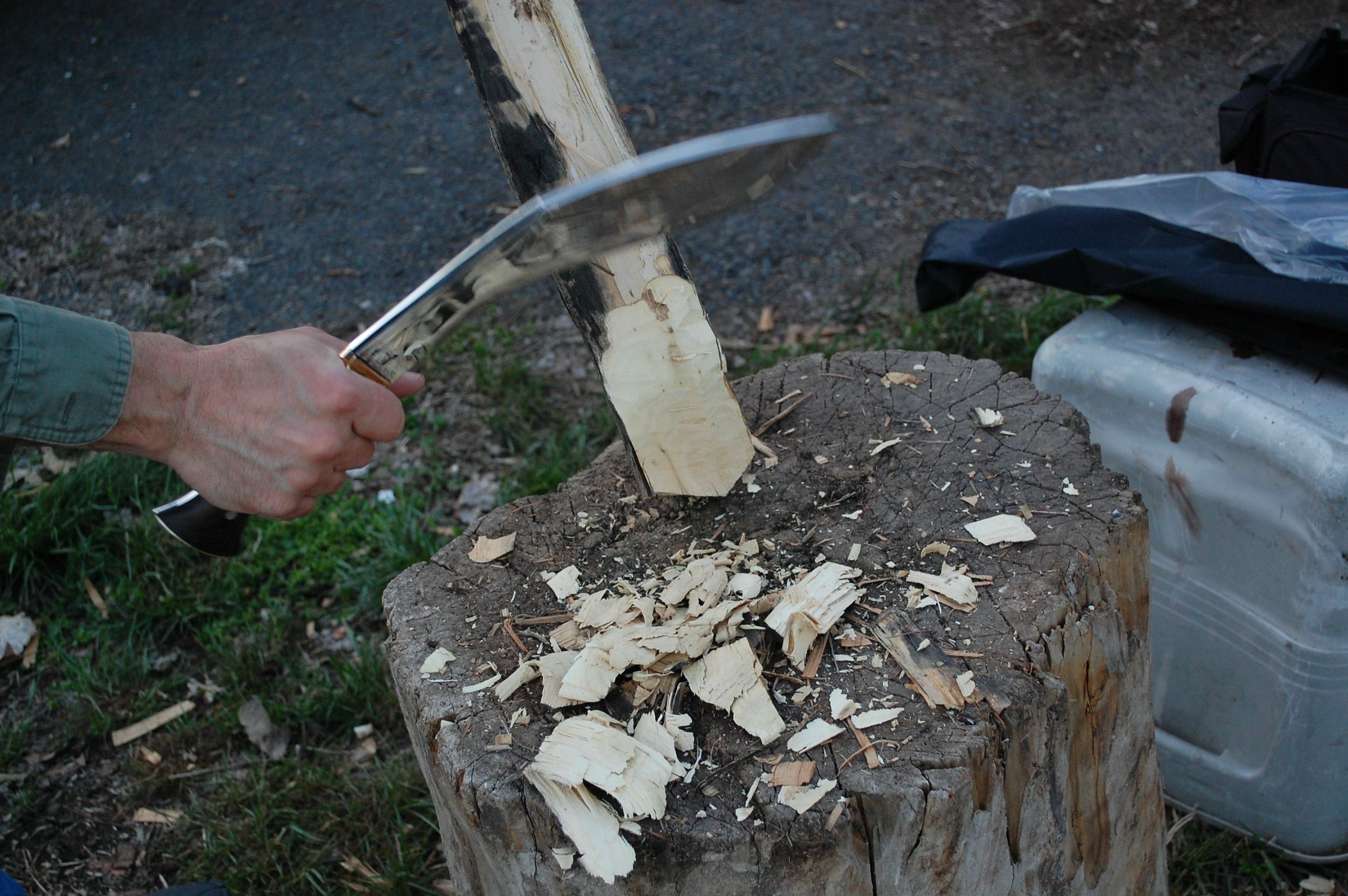
Ok, I have to apologize for the quality of this picture; it was starting to get dark. I'm pointing at the end of the back ring with my karda, and outlined the edge of the edge of the early wood layer with a marker. Everything above that line will have to be removed, until the ring I've selected to be the back continues unbroken the entire length of the stave. That's it for tonight. I don't know if this stave will ultimately yield a working bow, but we will find out!
