- Joined
- May 2, 2013
- Messages
- 1,711
Hello all, I had to take a break from knifemaking for a while due to some family issues, then some day job responsibilities, but finally got to get back in the shop for a reasonable amount of time and hopefully back on track. I have to say, I have been spot-lurking from time to time and there have been some VERY nice pieces turned out lately. Certainly some drool candy.
Well, my equipment is fairly archaic, and I don't use jigs or even patterns most of the time so I might not win any precision contests, but I think I can turn out a good usable blade from time to time. The one below started off as a request for an edc blade from a co-worker. He wanted it to be small enough to be useful but large enough to be used defensively if needed.
This project meant a couple of firsts for me, one being copper plating with copper sulfate solution to make the snaps I had match the copper rivets on the sheath. It seemed all the copper snaps I could find elsewhere were antiqued or had some sort of pattern on them. And second was the copper rivets themselves. They like to bend and move while being peened, so they did crawl a little in the leather, but not enough to cause any issues.
The steel is 3/16" thick 1095, flat ground, with a bit of a unique HT. It left a nice hamon diagonally across the upper blade and ricasso down to the choil. See below for my curiosities about the HT... The blade is flat ground. Measurements came in at 8" overall, 3.5" blade with a 4" cutting surface. Blade is about 1.25" wide, and handle a scant 1" wide. The scales are dyed and stabilized fleck sycamore. They resemble brook trout skin to me, but I fly fish so... The pins and lanyard tube are 1/8" and 1/4" copper respectively.
Anyway, here it is, feel free to criticize as necessary... I welcome honest input as this is how we learn. And I believe life should always be a learning process.
Pardon the picture quality. They are cell phone pics. My Galaxy does well, but still isn't as good as the real camera.
Here is the blade right out of the quench. You can see the coloration running back through the blade. The edge easily passes a brass rod test, however the body of the blade still has some nice flex to it. Anyone of the HT artists here can feel free to confirm or discount what happened during the HT of the blade. My hope and belief is that the heat held in the body of the blade ran back toward the blade edge tempering it as it went. It was an interrupted quench in hot water. This blade takes and holds one of the best edges I have achieved, and the thin blade profile makes it a real slicer.
Here is the snap I copper plated. Pretty proud of how this turned out... I like playing with electricity and chemicals!...
Finished knife and sheath.
Knife and matching lanyard bead.
Other side.
In the sheath.
Other side. You can see how the copper crawls while being peened... The holes were centered well however the bases tended to move... Need more practice with those.
Here are some detail shots of the wood scales. I polished them to 2500 grit and then with the buffer on up to jeweler's rouge... However this proved to be too slick. The knife was actually hard to hold onto... lol. Ended up knocking them back to about 1500-2000 grit so they had a little stick. Still, the polished up scales were striking IMHO.
Thanks for looking. Extremely glad to be back in the shop slinging steel and making sparks fly...
Well, my equipment is fairly archaic, and I don't use jigs or even patterns most of the time so I might not win any precision contests, but I think I can turn out a good usable blade from time to time. The one below started off as a request for an edc blade from a co-worker. He wanted it to be small enough to be useful but large enough to be used defensively if needed.
This project meant a couple of firsts for me, one being copper plating with copper sulfate solution to make the snaps I had match the copper rivets on the sheath. It seemed all the copper snaps I could find elsewhere were antiqued or had some sort of pattern on them. And second was the copper rivets themselves. They like to bend and move while being peened, so they did crawl a little in the leather, but not enough to cause any issues.
The steel is 3/16" thick 1095, flat ground, with a bit of a unique HT. It left a nice hamon diagonally across the upper blade and ricasso down to the choil. See below for my curiosities about the HT... The blade is flat ground. Measurements came in at 8" overall, 3.5" blade with a 4" cutting surface. Blade is about 1.25" wide, and handle a scant 1" wide. The scales are dyed and stabilized fleck sycamore. They resemble brook trout skin to me, but I fly fish so... The pins and lanyard tube are 1/8" and 1/4" copper respectively.
Anyway, here it is, feel free to criticize as necessary... I welcome honest input as this is how we learn. And I believe life should always be a learning process.
Pardon the picture quality. They are cell phone pics. My Galaxy does well, but still isn't as good as the real camera.
Here is the blade right out of the quench. You can see the coloration running back through the blade. The edge easily passes a brass rod test, however the body of the blade still has some nice flex to it. Anyone of the HT artists here can feel free to confirm or discount what happened during the HT of the blade. My hope and belief is that the heat held in the body of the blade ran back toward the blade edge tempering it as it went. It was an interrupted quench in hot water. This blade takes and holds one of the best edges I have achieved, and the thin blade profile makes it a real slicer.
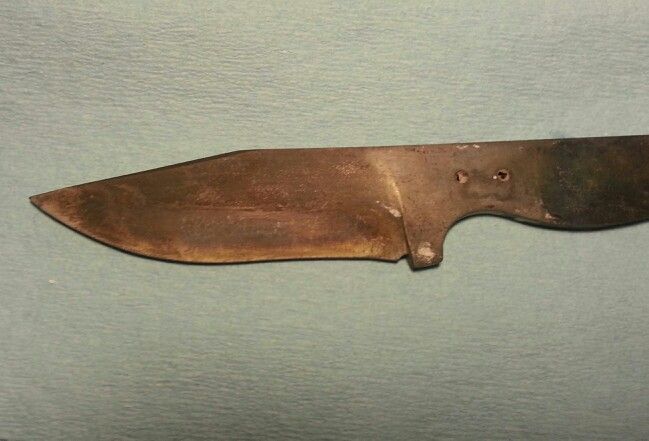
Here is the snap I copper plated. Pretty proud of how this turned out... I like playing with electricity and chemicals!...

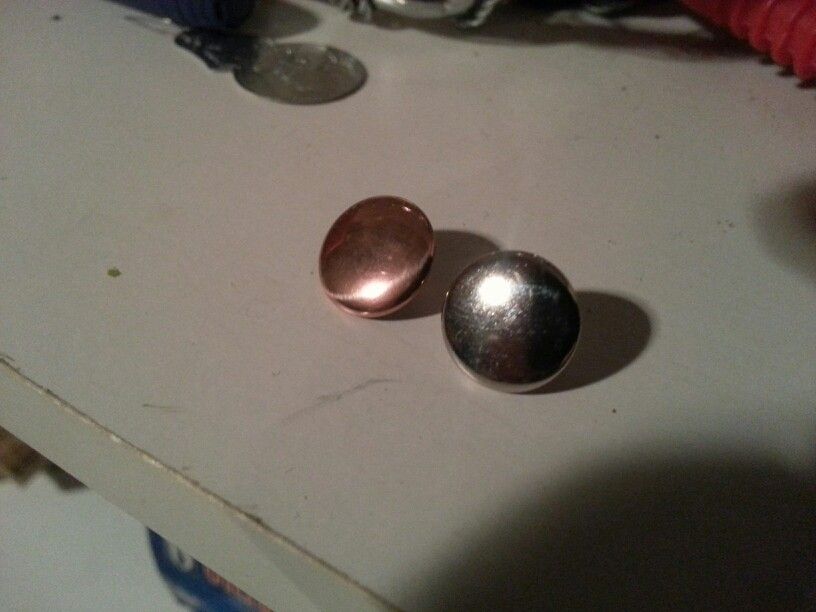
Finished knife and sheath.
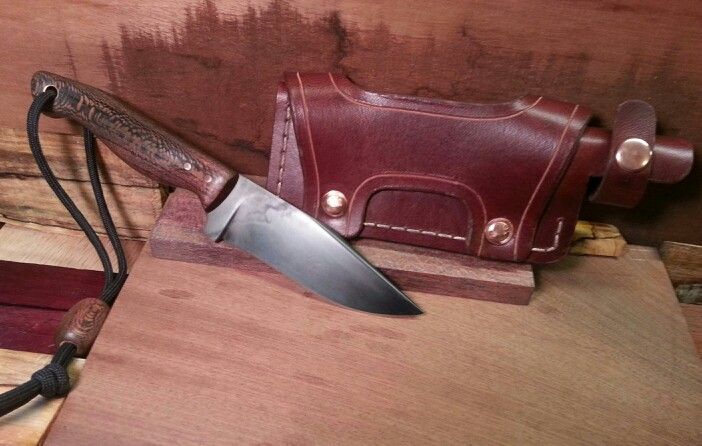
Knife and matching lanyard bead.
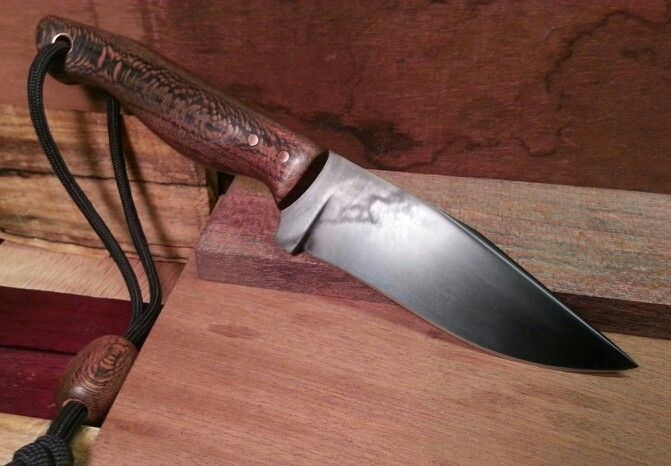
Other side.
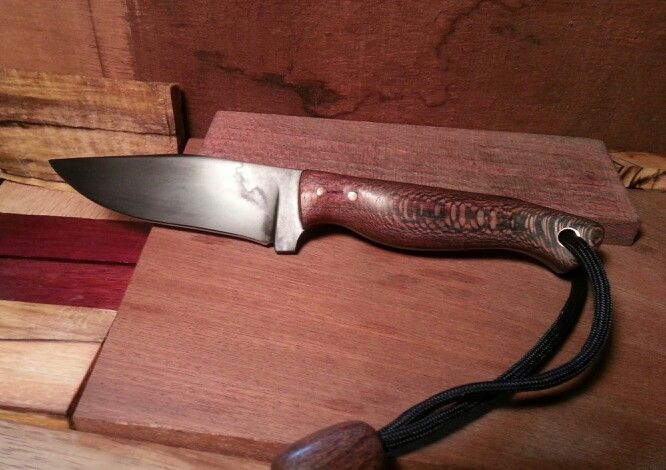
In the sheath.
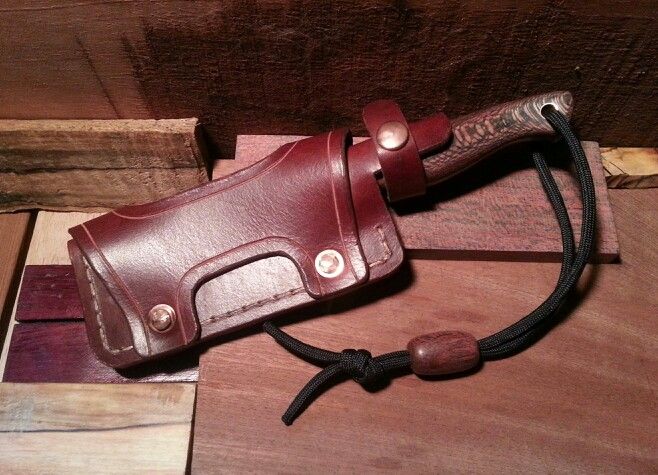
Other side. You can see how the copper crawls while being peened... The holes were centered well however the bases tended to move... Need more practice with those.
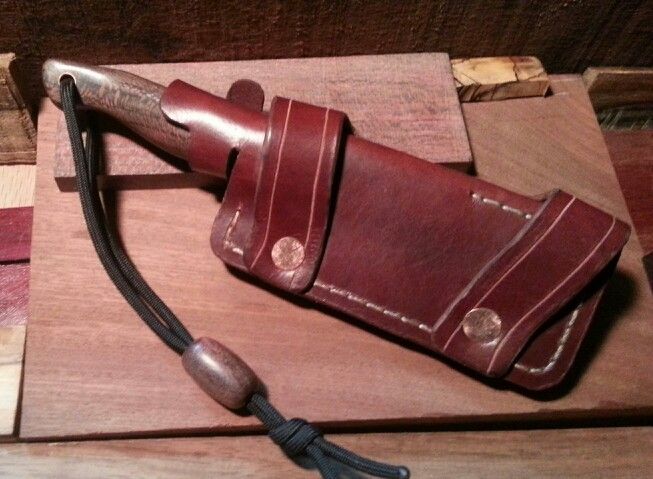
Here are some detail shots of the wood scales. I polished them to 2500 grit and then with the buffer on up to jeweler's rouge... However this proved to be too slick. The knife was actually hard to hold onto... lol. Ended up knocking them back to about 1500-2000 grit so they had a little stick. Still, the polished up scales were striking IMHO.

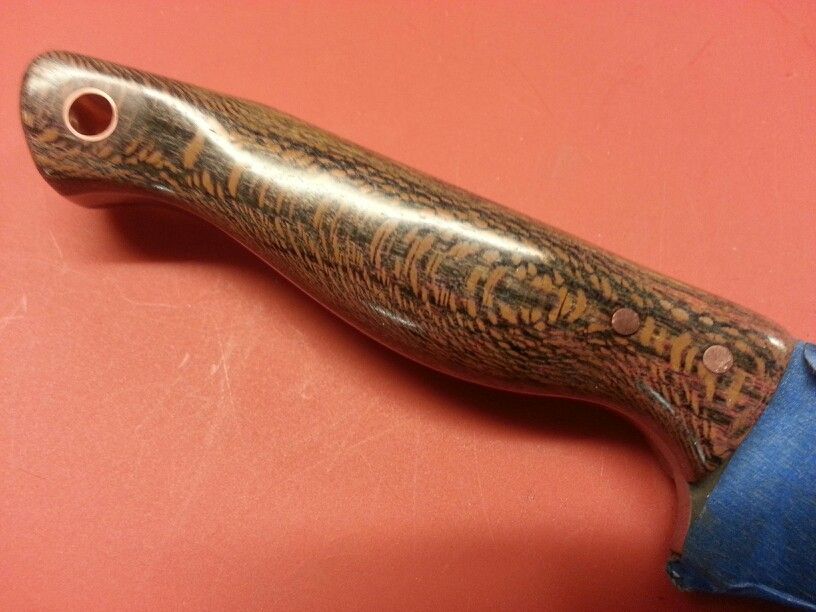
Thanks for looking. Extremely glad to be back in the shop slinging steel and making sparks fly...