- Joined
- Nov 3, 2017
- Messages
- 109
New guy here - so go easy. I actually forged a rambo knife back in 84, and loved the whole process - even "set" the teeth prior to hardening / tempering.
Anyway, I recently developed a process to mold unidirectional CF and Kevlar fiber into wood figure like "flame" and "Quilted" figure because fiber replicates wood figure chatoyance exactly. I machine the panels flat, then any shape or roundover edge shows the light refractivity (Chatoyance) all the way through. So wild I even patented the process (why I'm in serious debt).
Waayyyy wilder than marbled or swirled uni, because there is a pattern in the waviness, not random, as I made the molds based on actual fiddleback and quilted figure, where viewers subconsciously equate the pattern to burled or curly figured wood, but the chatoyance is greater than that of the deepest figured quilted maple or burl walnut.
Currently marketing these sheets for fretboards and body "veneers" in the guitar industry, but always thought knife handles would be a potential market, although small, so never really pursued it until now that I have a few products like my Opalescent acrylic sheets in addition to the new solid figured CF.
I am assuming most won't see the advantage over common woven CF or marbled uni, which is why I am posting here to see if this has market value. I've seen woven and marbled CF at 40 bucks per 2 x 6 blank, and thought I could easily go less than that, but is it worth it for a few sq ft a year when my business is geared toward thousands in the architectural surfacing market.
Then there is my older product - Dichrolam Burls, which are optically identical to Australian Fire Opal, and I used to only make it in glass, but now in thick acrylic but markets are slim for that. Not sure if acrylic would work in knife handles. Maybe other resins - need help there.
I paid my membership as maker so I can post this inquiry. If this has any potential in knife handles let me know. The solid figured CF machines like any other CF, no voids, polishes to high luster - same as any other CF. Planning to mold a panel next week with Kevlar (gold) interleafed within every three layers of CF so when machined you get a zebra-striped effect. Gotta stay tuned to this thread to see that when I post pics.
Thickness are currently about 1/8" to 5/16". Can easily go thicker, or epoxy to standard CF plate. Master panels are 20 x 24 (Solid CF / Kevlar curly), 24 x 48 in Fire Burl, White Burl, Red Burl etc, and 33 x 57 in Quilted figure (resin filled, not solid yet).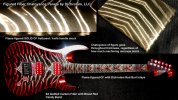
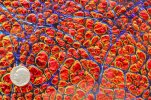
Anyway, I recently developed a process to mold unidirectional CF and Kevlar fiber into wood figure like "flame" and "Quilted" figure because fiber replicates wood figure chatoyance exactly. I machine the panels flat, then any shape or roundover edge shows the light refractivity (Chatoyance) all the way through. So wild I even patented the process (why I'm in serious debt).
Waayyyy wilder than marbled or swirled uni, because there is a pattern in the waviness, not random, as I made the molds based on actual fiddleback and quilted figure, where viewers subconsciously equate the pattern to burled or curly figured wood, but the chatoyance is greater than that of the deepest figured quilted maple or burl walnut.
Currently marketing these sheets for fretboards and body "veneers" in the guitar industry, but always thought knife handles would be a potential market, although small, so never really pursued it until now that I have a few products like my Opalescent acrylic sheets in addition to the new solid figured CF.
I am assuming most won't see the advantage over common woven CF or marbled uni, which is why I am posting here to see if this has market value. I've seen woven and marbled CF at 40 bucks per 2 x 6 blank, and thought I could easily go less than that, but is it worth it for a few sq ft a year when my business is geared toward thousands in the architectural surfacing market.
Then there is my older product - Dichrolam Burls, which are optically identical to Australian Fire Opal, and I used to only make it in glass, but now in thick acrylic but markets are slim for that. Not sure if acrylic would work in knife handles. Maybe other resins - need help there.
I paid my membership as maker so I can post this inquiry. If this has any potential in knife handles let me know. The solid figured CF machines like any other CF, no voids, polishes to high luster - same as any other CF. Planning to mold a panel next week with Kevlar (gold) interleafed within every three layers of CF so when machined you get a zebra-striped effect. Gotta stay tuned to this thread to see that when I post pics.
Thickness are currently about 1/8" to 5/16". Can easily go thicker, or epoxy to standard CF plate. Master panels are 20 x 24 (Solid CF / Kevlar curly), 24 x 48 in Fire Burl, White Burl, Red Burl etc, and 33 x 57 in Quilted figure (resin filled, not solid yet).
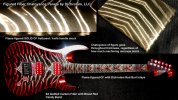
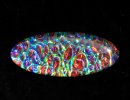
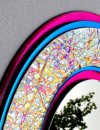
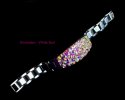
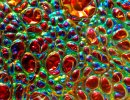
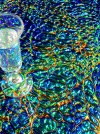
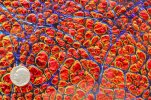