- Joined
- Jun 23, 2007
- Messages
- 2,142
A fellow BladeForums member commissioned a pair of Damascus Dogbone knives to feature Walrus handles from the same tusk, bought at Blade last year.
He asked me to keep him photographically informed as I worked, was able to visit the shop several times along the way, and suggested I share the results with our fellow members.
Here's an overview of the construction of the first of the two, a 4-bar/9-bar composite D-Guard Bowie, finer and more "Mosaic" appearing than my usual.
The second knife will be a matching Dagger. Both will have creamy Walrus scales with brown highlights, Damascus fittings, with Sterling Silver spacers, frame liners, and domed pins.
Here's a magnificent Buddy Thomason photo of the finished D-Guard and it's fantastic Paul Long sheath.
]
The blade began with two billets, a 15 layer "flat," and a 13 layer "W."
Welding was done with a 25 lb, 1947 Moloch hammer, the 15 layer forged up to 60 layers. and the 13 layer 'W" to a "13 x 12"
Both billets were then drawn out on the Uncle Al press.
to two, 9/16ths x 9/16ths bars.
The bars were cut into matching six inch lengths, and arranged into a 9-bar billet. You should be able to see the arrangement, with a 60 layer "flat" in the center, and at each corner, and a "W" in the middle of each side.
Tacked together, welded to a handle,
the 9-bar was welded,
drawn out to another 9/16ths x 9/16th bar, 32 inches long.
This 9-bar was then cut into four 8 inch bars, and twisted tightly, two right-handed, and two left handed.
Here they are after re-squaring, grinding clean on the matching faces, and readied for welding into two right/left billets.
Next will come fabricating the 4-bar blade billet from the four 9-bars.
He asked me to keep him photographically informed as I worked, was able to visit the shop several times along the way, and suggested I share the results with our fellow members.
Here's an overview of the construction of the first of the two, a 4-bar/9-bar composite D-Guard Bowie, finer and more "Mosaic" appearing than my usual.
The second knife will be a matching Dagger. Both will have creamy Walrus scales with brown highlights, Damascus fittings, with Sterling Silver spacers, frame liners, and domed pins.
Here's a magnificent Buddy Thomason photo of the finished D-Guard and it's fantastic Paul Long sheath.

The blade began with two billets, a 15 layer "flat," and a 13 layer "W."

Welding was done with a 25 lb, 1947 Moloch hammer, the 15 layer forged up to 60 layers. and the 13 layer 'W" to a "13 x 12"

Both billets were then drawn out on the Uncle Al press.

to two, 9/16ths x 9/16ths bars.

The bars were cut into matching six inch lengths, and arranged into a 9-bar billet. You should be able to see the arrangement, with a 60 layer "flat" in the center, and at each corner, and a "W" in the middle of each side.

Tacked together, welded to a handle,

the 9-bar was welded,

drawn out to another 9/16ths x 9/16th bar, 32 inches long.

This 9-bar was then cut into four 8 inch bars, and twisted tightly, two right-handed, and two left handed.
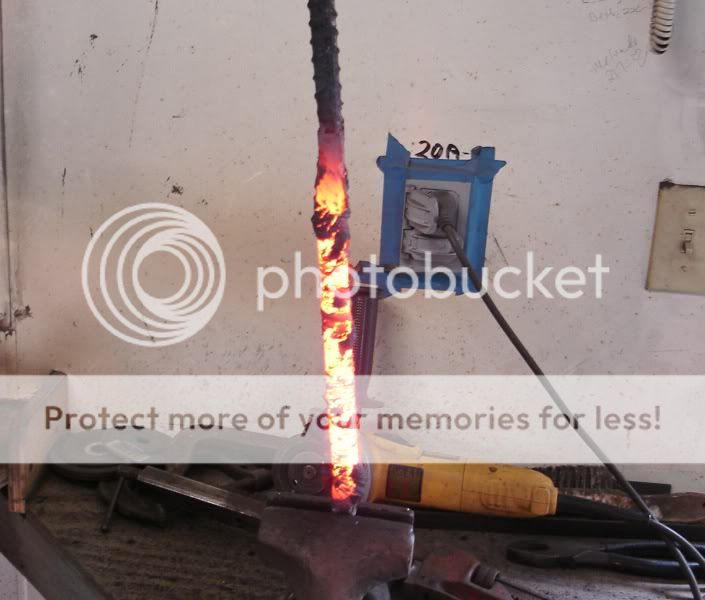
Here they are after re-squaring, grinding clean on the matching faces, and readied for welding into two right/left billets.

Next will come fabricating the 4-bar blade billet from the four 9-bars.
Last edited: