So I figured why not post a work in progress of an eerf grinder I started today. This is more of my element rather than knife making as I'm a welder, fabricator, welding inspector and a welding instructor for a community college. After I finished my knife yesterday and I'm out of blade material so I decided an upgrade of the ole harbor freight is in order. Today at work I saw a guy doing nothing, and it just so happens he runs the cnc plasma cutter so I decided he needed something to do. The plasma struggled to cut the thick plate but a bad kerf I can live with. The plasma also has a wide kerf so I decided I'd just drill or mill my bolt holes. I wanted to set this grinder apart from the crowd so I had my student put my initials in my grinder. I use the same symbol on all my stuff and will eventually be my makers mark on my blades. I have read just about all the threads out there about pulleys and VFD. For this grinder I'm going to go straight to vfd. It will have to wait until after Christmas to get up and going but I promise there will be some good stuff along the way.
On the cnc
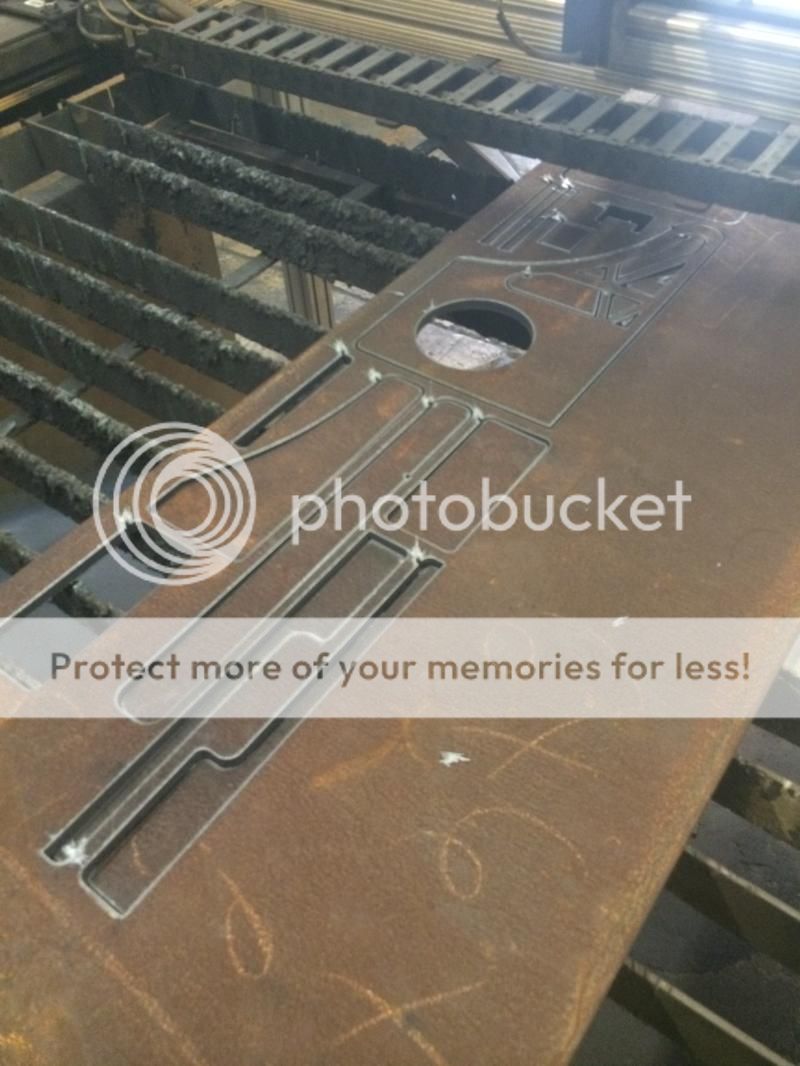
After dross removal and a quick pass on the wire wheel

Starting the drilling madness

As far as I got tonight.(yes I'm aware my garage is a pig sty but Christmas break is Thursday.)

On the cnc
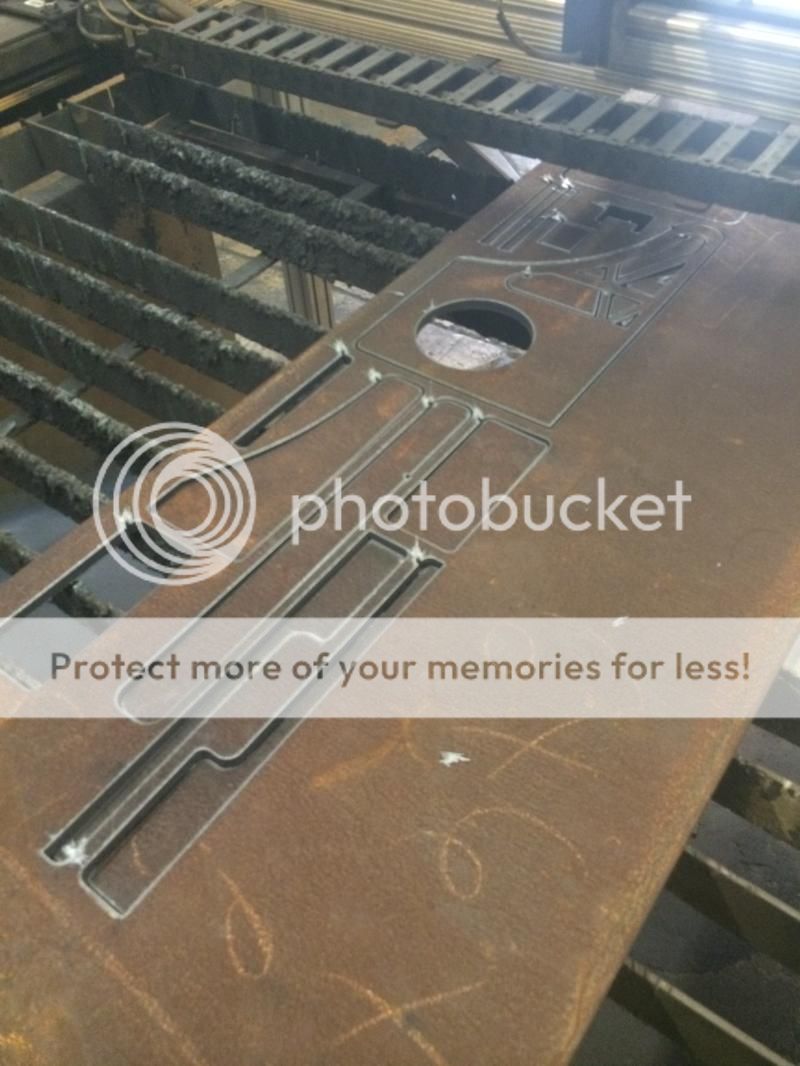
After dross removal and a quick pass on the wire wheel

Starting the drilling madness

As far as I got tonight.(yes I'm aware my garage is a pig sty but Christmas break is Thursday.)
