sweetcostarica
BANNED
- Joined
- Jan 18, 2012
- Messages
- 619
That turned out really nice. 100% improvement. Wondered if it was sacrilege to improve or make a handle finish nicer. Guess it depends on the person and how rare the blade might be.
Good job on that handle fix Ray. It should be a permanent fix but that depends on the wood (if it was treated, correctly stabilized, etc). I have a huge unfixed crack in an old Goorkha Army Khukuri (GAK). Actually it has another smaller crack just opposite on the other side of the handle. It has been swung, shaken, leveraged lightly and guess what... the handle is rock solid in the over 100 year old Kukri. So I think as long as the "Laha" (Nepali Traditional Glue) was made right that will keep your handle securely attached to the tang no matter how many splits in the wood, horn, or other material, within reason.
Below 100 year old hidden tang Kukri with solidly attached handle
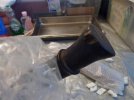
Bawanna I'm with Jake (aka Steely_Gunz) on the sanding, fitting the grip to your hand, basically modifying the grip to your own hand. I have been told that in Nepal if you wanted a Kukri you would go to the Kami and he would make the Kukri 1st to your specifications (wood, horn, long, short, and so on) and 2nd fit the blade to your type and handle to your hand. Probably doing a lot of measuring and educated guessing. The process is like the Himalayan Import's Special Order but much more involved as if you were going to the tailor to have a suit made.
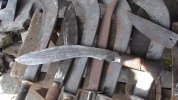
Above photo: average farm tools in Nepal
Again top notch job Raymond. Even if the repair doesn't hold up, the handle will stay on tightly if the Laha is good. And if it's a user who cares what it looks like as long as it works :thumbup:. Enjoy that Kukri while you can because the handmade Kukri skill is a dying art in Nepal.
Below paragraph is from lyndon2742 on an older thread about Laha:
"The laha which I prefer to call Himalayan epoxy is collected from trees by what Pala called "jungle men". Pala and almost all shops and kamis buy the stuff commercially rather than trying to collect it themselves. It is basically tree gum. It is boiled and then poured into the desired places of the khukuri. The advantages it has are it sets up very quickly, allowing the kami to continue working on his khukuri without setting it aside for 24 hours to let the epoxy set up, and it is also quite strong."
Last edited: