I'm pretty much finished with the knife. I'll make a leather sheath for it a little later.
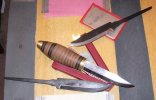
I really like this knife. It is the sharpest knife that I own. I finished the leather with 220 grit sand paper then used a liberal amount of SNO-SEAL on it. Baked it in the oven at 170 degrees F for 10-20 minutes and reapplied the SNO-SEAL. Did it 3 times then applied a final coat and rubbed it hard for 15-20 minutes. Wiped it off with a paper towel and let it set for a couple of days and wiped it off again. It just barely cuts the tissue paper but that is sharper than I've gotten any knife before. It took the hair off my arm with almost no resistance.
I followed the advice given by Bladsmth except I left it in the compression jig for a day before I riveted the tang.
If you rivet the tang while the leather is under compression you would not need to glue the leather. I fitted each piece of leather to the location on the tang where is was supposed to go. When it is compressed it locks in tight.
I would not use JB Weld to seal the bolster for this shiny blade as the black color stands out against the brass and steel. Non issue for a working knife but a huge issue for a presentation knife.
I used a rasp to rough out the handle. It took a long time. Likewise with trying to shape the pommel. The belt sander with 50 grit probably cuts the time by 90%. I'd finish by hand as the sander seems to take material off fast.
Thanks to everyone who helped or offered to help me with this project.
Bo Thomas
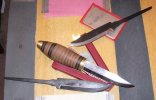
I really like this knife. It is the sharpest knife that I own. I finished the leather with 220 grit sand paper then used a liberal amount of SNO-SEAL on it. Baked it in the oven at 170 degrees F for 10-20 minutes and reapplied the SNO-SEAL. Did it 3 times then applied a final coat and rubbed it hard for 15-20 minutes. Wiped it off with a paper towel and let it set for a couple of days and wiped it off again. It just barely cuts the tissue paper but that is sharper than I've gotten any knife before. It took the hair off my arm with almost no resistance.
I followed the advice given by Bladsmth except I left it in the compression jig for a day before I riveted the tang.
If you rivet the tang while the leather is under compression you would not need to glue the leather. I fitted each piece of leather to the location on the tang where is was supposed to go. When it is compressed it locks in tight.
I would not use JB Weld to seal the bolster for this shiny blade as the black color stands out against the brass and steel. Non issue for a working knife but a huge issue for a presentation knife.
I used a rasp to rough out the handle. It took a long time. Likewise with trying to shape the pommel. The belt sander with 50 grit probably cuts the time by 90%. I'd finish by hand as the sander seems to take material off fast.
Thanks to everyone who helped or offered to help me with this project.
Bo Thomas